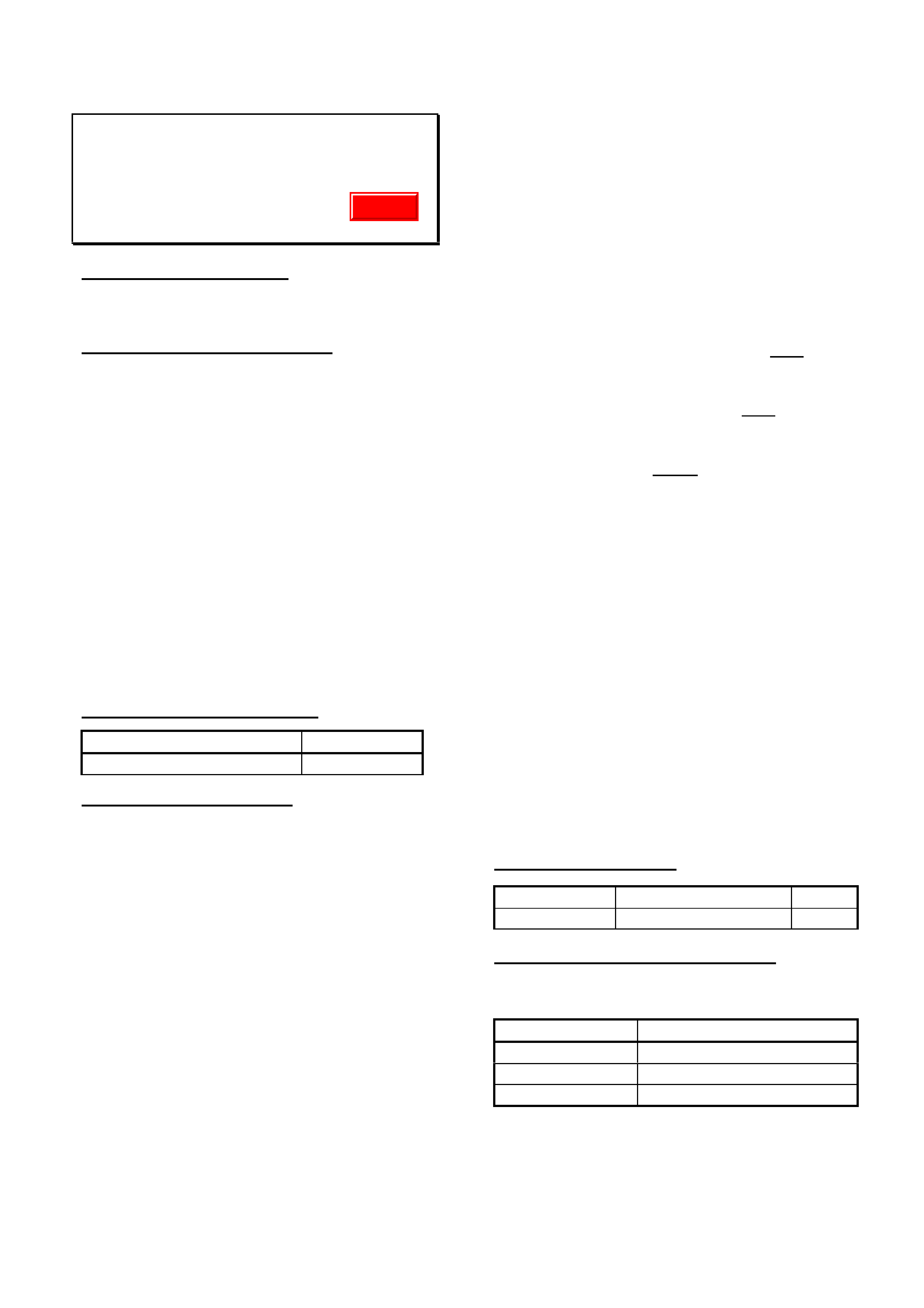
HOLDEN SERVICE TECHLINE ____________________________________________________________ JULY 2001
12
TURBO (SHAFT) FAILURE
UBS JACKAROO with 4JX1 DIESEL
ENGINE
(GROUP 6A) TL107-6A01
PROBLEM DESCRIPTION
The engine loses power and emits an
abnormal amount of smoke.
PRODUCTION RECTIFICATION
A revised turbocharger assembly has been
developed - revisions include:
• increased oil supply orifice diameter at
the turbo bearing;
• high speed balancing process introduced
in production to reduce the load on turbo
shaft bearings;
• finer mesh strainer used in the primary
pump oil pick-up to prevent foreign
material damaging the oil pressure relief
valve, causing a reduction in oil pressure.
This finer strainer is a product
improvement and the existing strainer
does not require replacement when a
turbo is replaced.
PRODUCTION BREAK POINT
ISOVIN: Build Date:
JACUBS73GY7106740 July 2000
SERVICE RECTIFICATION
Where a turbocharger has failed, procure a
new turbo assembly from HSPO, and fit to
the vehicle, using the following guidelines:
When fitting a new turbo you must:
§ To prevent further bearing failures,
confirm that the injector seal rework has
been carried out on the vehicle (position
C1 on the Vehicle Service History Label -
located on the drivers A pillar, between the
door hinges). Complete the injector seal
rework if required, refer All Dealer Letter
IGM 04/00.
§ Never run the vehicle before priming
the turbo bearings with oil and, never
run the vehicle with the oil supply to
the turbo disconnected.
§ Check the oil supply to and from the turbo
before fitting the new turbo assembly.
Disable the vehicle by disconnecting the
cam sensor and check oil supply at
cranking speed. Oil flow tests are easier to
complete with the failed turbo removed.
These are approximate values to use as
a guide only. Oil viscosity, temperature,
battery condition, etc, will cause results to
vary between vehicles.
ü Oil should flow from the turbo feed pipe
within approx. 17 seconds of cranking;
ü Approximately 25ml of oil should flow
from the turbo lubrication feed pipe for
every 1 second of cranking (once the
oil flow has commenced);
ü Check the oil return from the turbo to
the crank case. When oil is poured into
the return hose it should flow freely into
the crank case.
§ Prime the turbo by adding 100ml of oil to
the turbo oil lubrication inlet. Rotate the
turbo shaft slowly by hand, this will
ensure the turbo bearings are lubricated
at initial start up.
Detailed fitting instructions for removal and
installation of the turbo unit are in LCV SIP.
Once in SIP follow the path:
§ UBS Jackaro
§ Engine – 4JX1
§ Section 6A – Engine Mechanical
§ Engine Assembly
§ Turbocharger
PARTS INFORMATION
Part No.: Description: Qty:
8972503640 Turbo Assembly 1
WARRANTY CLAIM INFORMATION
Use existing warranty information in LCV SIP
as below.
Description Turbo Asm - Replace
Labour Op. No. J586300
Time 2.2 hr
Failure Code 85