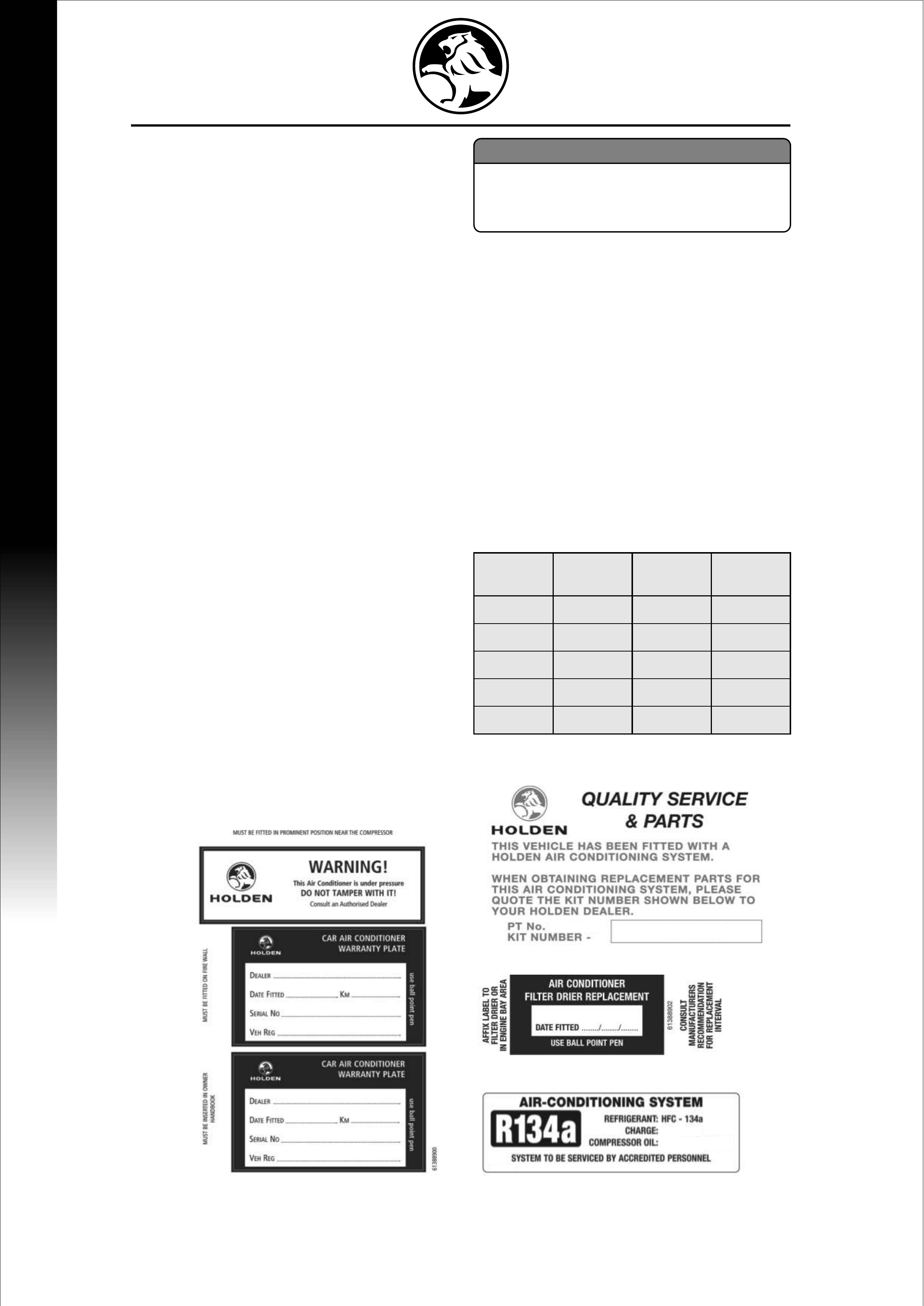
2
PREPARATIONPREPARATION
PREPARATION
Read through these fitting
instructions prior to beginning the
installation. Then carefully follow
these instructions throughout
installation from Step 1.0 to
charging and testing the system.
POINTS TO CHECK
a) Open and inspect kit for any damage to
parts.
b) Check all parts are present in the kit using
the contents list supplied.
c) Check the vehicle for any damage to the
interior and exterior.
d) Check function of Ventilation Blower Fan,
Temperature Control Door, Horn, Light,
Headlamps.
INSTALLATION PRECAUTIONS
a) This system has been designed to suit
standard wiring by the vehicle manu-
facturer, the wiring of non-approved
accessories could result in malfunction of
the unit or damage to the vehicle.
b) Disconnect neg. lead from the battery.
c) Route all refridgerant hoses, tubes and
wiring harnesses to avoid fouling.
LABELS
d) To prevent entry of foreign moisture into
the system do not remove shipping plates
or plugs until immediately before
installation of the components.
e) O-Rings do not require lubrication as they
are pre-fitted to most tubes/hoses and
pre-lubricated with silicon at the
manufacturer.
f) Use two spanners when tightening
fittings.
g) Use torques as specified.
h) Use only specific R134a charging
equipment and leak detector.
1.4 TORQUE CHART
HOSE & TUBE FITTINGS
NOTE:
This system uses a specific lubricating
oil - Polyalklene Glycol (PAG). This oil
is highly hygroscopic, adhere to step D
1.1
1.2
1.3
SIZE
No.5
No.6
No.8
No.10
No.12
5/16
3/8
1/2
5/8
3/4
9/16-18
5/8-18
3/4-16
7/8-14
1-1/6-12
13.0-15.0
11.0-16.0
18.0-23-0
24.0-30.0
30.0-38.0
TUBE
O.D THREAD
-UNF TORQUE
Nm
1.5
92148131
25187352
25187353
+
-
700 25g700 25g
PAG 1 (230ml)PAG 1 (230ml)