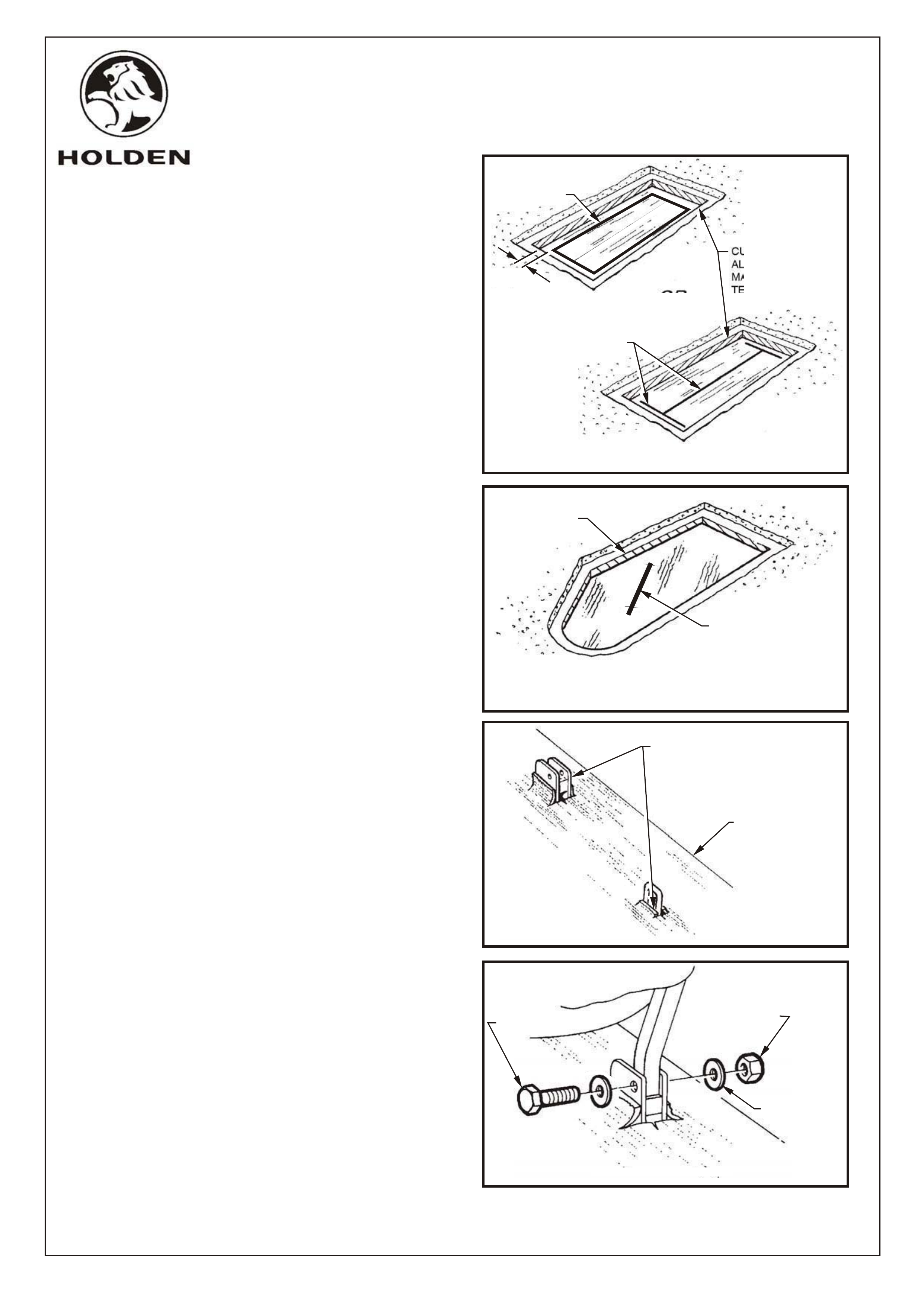
FIGURE 11
ALIGN SLOTS IN CARPET
OVER PIVOT MOUNTS
AND STRIKERS
REFIT CARPET
AND SPARE WHEEL
COVER ASSEMBLY
FIGURE 12
NYLOC
NUT M8
FLAT WASHER
BOLT M8
RH SHOWN, LH OPPOSITE
28. Use a short 3.0dia. drill. Drilling depth must be limited
to 4.0 +0.0 -0.75mm to prevent drilling through carpet.
Use an appropriate length of copper tube slipped over
and crimped to the drill bit (up to the chuck), for a
spacer.
29. Drill at 4-5mm intervals around perimeter of marks.
Ensure the drill does not go through the carpet.
30. Use a blunt chisel, 12mm wide, to crack plastic all
around perimeter. DO NOT CUT THROUGH
CARPET. Remove plastic cut-out.
NOTE: The plastic is glued to the carpet.
31. Insert chisel or srewdriver under one edge of the
perforated cut-out in the masonite and lever piece out.
Clean up edge of hole.
NOTE: The masonite is glued to the carpet.
32. Place rear striker cut-out pieces of template in the
holes appropriate to them. Approximation may be
required , depending on accuracy of hole.
33. Use a chisel on a block of wood to cut through the
carpet in the places indicated on the template.
FIGURE 10
SLIT CARPET
HERE FOR
STRIKER LOOP
RH STRIKER CUTOUT SHOWN,
LH SIMILAR
CUT PLASTIC ALONG
MARKED LINE
FIGURE 9
SLIT CARPET
HERE
CUT MASONITE
ALONG LINE
MARKED OFF
TEMPLATE
OR
CUT OUT
SECTION
OF CARPET
CUTOUT FOR FRONT PIVOT MOUNTS
5.0mm
NOTE: One of two methods may be used to trim carpet
around front pivot mounts. If method 34a. is used a hole
will be left in floor carpet if 3rd seat is ever removed,
whereas with method 34b. the carpet flaps will lie back
down to fill the hole.
34a.Trim carpet 5mm inside perimeter of hole cut in
masonite, refer figure 9.
OR
34b.Slit carpet along centre of hole in masonite and
across each end of hole, refer figure 9.
NOTE: A short slit in the carpet(as indicated on the
template), is all that is required at rear striker locations, to
allow striker loop to protrude through carpet, refer figure
10.
35. Refit carpet and spare wheel cover assembly to rear
compartment over 3rd seat pivot and striker mounts,
refer figure 11. Replace fir tree fasteners.
36. Install 3rd seat front leg mounts and install bolts.
Attach washers and "Nyloc" nuts (2 places), refer
figure 12.
NOTE: Do not over tighten leg mount nuts.
COPYRIGHT
Page 5 of 8
HOLDEN SERVICE PARTS OPERATIONS
Reproduction in whole or part
prohibited without written approval
Division of HOLDEN Ltd ACN 006 893 232
FD840
25OC02
G727