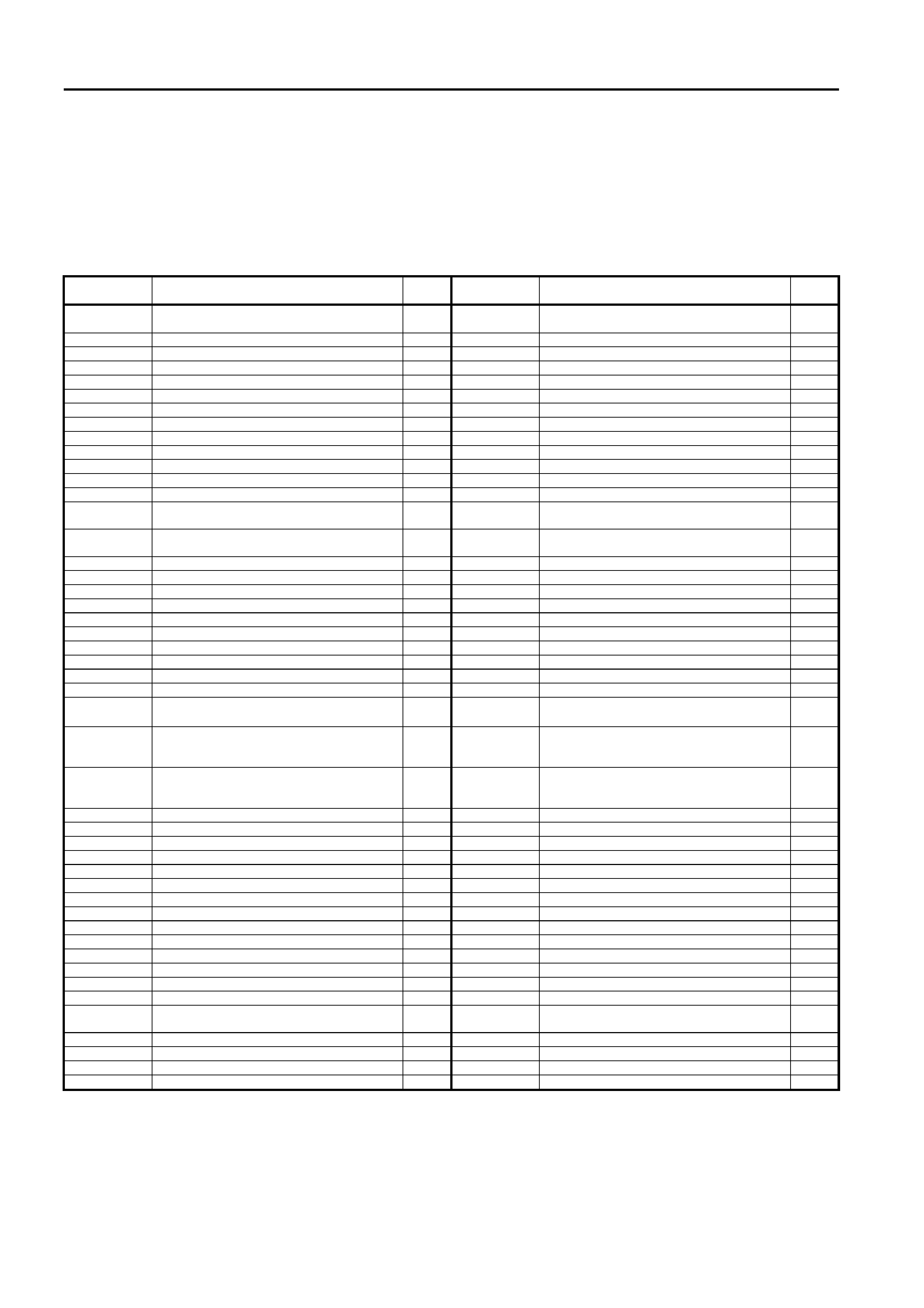
6-2 PARTS LIST
PARTS LIST - VY2 (Build January 2004 onwards)
NOTE: For VY2 series vehicles built in or after January 2004, a unique Euro 2 configured mixer assembly with tamper proof
idle mixture screw and cap is used. This mixer is the same as that used on Euro 2 configured WK LPG systems.
VY2 V6 vehicles built from the start of 2004 can be identified by their exhaust system, which incorporates two close-coupled
catalytic converters, mounted along the front exhaust assembly pipes close to the manifold flange joints.
For VY2 V6 vehicles built before 2004, the mixer assembly supplied with the LPG installation kit is identical to that used on
VY V6 vehicles. The exhaust system on these vehicles incorporates a single catalytic converter, mounted along the front
pipes close to the intermediate to front pipe flange.
PART NO DESCRIPTION QTY PART NO DESCRIPTION QTY
92060732 BOLT/SCREW-LPG VAPORIZER HEATER
HOSE CLAMP 14 92055739 VENT TUBE-JOIN TO FLOOR FLANGE 1
92052506 DUCT ASM-AIR METER TO MIXER 1 92138003 CLAMP, VALVE BOX/VENT PIPE 4
92055702 INDUCTION TUBE 1 92138061 CLAMP-FILLER HOSE VENT TUBE 2
92052498 CLAMP-INDUCTION TUBE-MIXER TO 3 92138551 SCREW-POCKET FLANGE (M6x2) 2
92100188 BRACKET-CONVERTOR MOUNT 1 92138212 STRAP 14
92087758 NUTSERT-M6x1 1 92076450 CONVOLUTED TUBE-H/T LEAD 3
09440004 NUT-CONVERTER BRACKET TO BODY 5 92119976 SUPPLEMENT, OW NERS SERVICE 1
92078978 SLEEVE, HEAT 1 92077227 CAP-FUEL FILLER 1
92081623 HEAT SHIELD-CONVERTER 1 92141575 CLAMP 1
92056796 SUPPORT-HEAT SHIELD-FRONT 1 92055731 REMOTE FILLER ASM-LPG CYL 1
92056797 SUPPORT-HEAT SHIELD-REAR 1 92055733 HOSE ASM-LPG CYL FILLER 1
92088197 VAPOUR HOSE-CONVERTER TO MIXER 1 92055736 VENT TUBE-LPG CYL TO JOIN 1
92094519 CLAMP - HOSE 25-38MM 3 92058201 POCKET FLANGE, FUEL 1
92055705 HOSE-HEATER WATER VALVE TO
CONVERTER 1 92145288 PIPE, REAR ASSEMBLY 1
92055706 HOSE-CONVERTER TO ENG. W ATER
INLET 1 92145289 PIPE, MID ASSEMBLY 1
92138004 CLAMP-HOSE TO CONVERTER 3 92145290 PIPE, FRONT ASSEMBLY 1
92055707 CLAMP-HOSE TO BODY 4 92049210 AIR CLEANER, UPPER 1
92138020 SCREW 1 11084962 SCREW, FLANGE 4
92055708 CONVOLUTED TUBE-HOSE PROTECTOR 7 92049008 ADAPTOR, AIR CLEANER 1
92057573 GROMMET-THROTTLE BODY 1 92023739 ADAPTOR, AFM 1
92057558 HOSE, CRANKCASE VENT 1 92032690 GASKET, AIR CLEANER 1
92083934 HOSE-CONV. TO PURGE VALVE 1 92053006 HOUSING, AIR CLEANER BOTTOM 1
92083935 HOSE-MIXER TO PURGE VALVE 1 92058202 WASHER, FILLER VALVE 1
92083936 HOSE-CONV. TO MIXER BALAN 1 92058203 NUT, FILLER VALVE 1
92083937 VAPOUR HOSE INSULATOR 1 92055737 VENT TUBE, LPG FILLER TO JOINER 1
92083938 For VY2 Built before Jan 2004:
MIXER ASM-COMPLETE 1 92056801 JOINER, VENT TUBE 1
92165980 For VY2 Built Jan 2004 and onwards:
MIXER ASM-COMPLETE
(Euro 2 tamper proof)
1 92041796 ELEMENT ASM - A/CL 1
92165981 For VY2 Built Jan 2004 and onwards:
CAP-CARB IDLE MIX NEEDLE
(With tamper proof mixer idle adjust cap)
1 92056798 BRACKET ASM -A/CL 1
92083939 CONVERTER ASM-COMPLETE 1 11063471 NUT - A/CL 3
1997278 VALVE ASM-PURGE 1 09281374 INSULATOR ASM-A/CL 3
92055714 HEAT SHIELD-LPG SUPPLY PIPE 1 92056550 DUCT, FRT INT AIR 1
92138381 RIVET 25 92053315 DUCT ASM - RR INLET AIR 1
92055723 LABEL-LPG 4 92076145 HOSE - INLET AIR MASS METER 1
92055724 LABEL-LPG INSTRUCTION 1 92120937 LABEL TYRE PRESSURE 1
92091859 REGO LABEL ASM-LPG 2 92113477 SWITCH, LPG 1
92055725 TANK ASSEMBLY-LPG SEDAN 1 92111640 ESCUTCHEON 1
92055726 BRACKET-LPG CYLINDER ATTACH-RH 1 92111636 SWITCH, BLANK 3
92055727 BRACKET-LPG CYLINDER ATTACH-LH 1 92159343 HARNESS, LPG PATCH 1
11090684 SCREW: M8 x 1.25 x 25 8 92055741 SPRINGS - RR 2
92055728 REINF-LPG CYL ATTACH RHS 1 92057566 CLAMP, LPG SUPPLY 2
92055729 REINF-LPG CYL ATTACH-LHS 1 92092925 LABEL, TRAC WARNING 1
92138241 SCREW, REINF TO LPG TANK 2 92141576 CLAMP, HOSE 9MM 9
11095803 NUT-CONELOCK-REINFORCEMENT TO
LPG 2 92103564 STRAP-R/CMPT LID LATCH RELEASE
CABLE 1
11086952 NUT-8MM 1 92159346 CARD, WARRANTY 1
92058200 GROMMET - VENT HOSE 1 92159345 INSTRUCTIONS, FITTING 1
92057565 FITTING-5/16 SAE STRAIGHT 2 92159344 PLATE, LPG ID 1
92055738 FLOOR FLANGE-VENT TUBE ATTACH 1