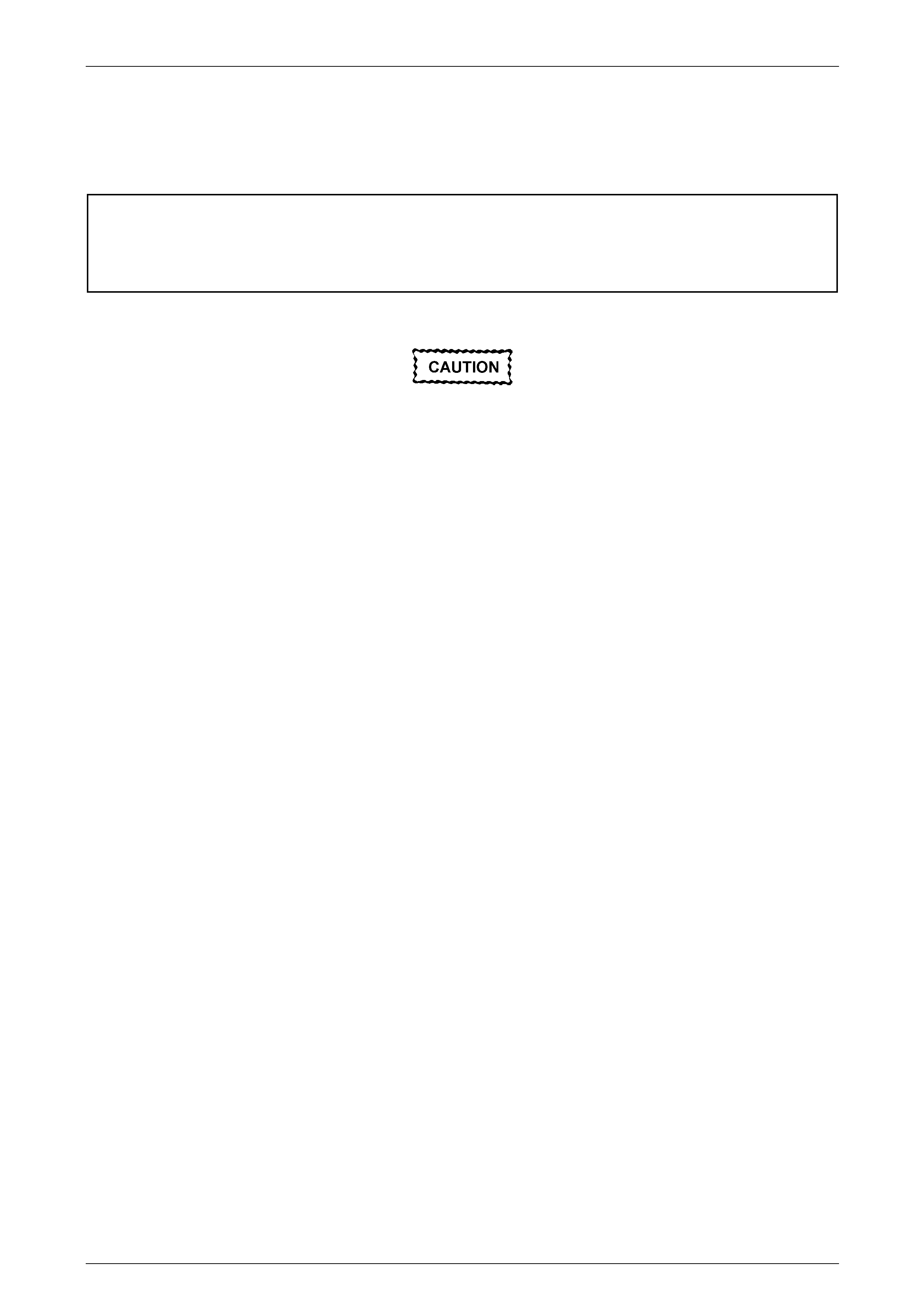
1 General Information Page 1-1
Page 1-1
Section 1
General Information
ATTENTION
Before performing any service operation or other procedure described in this Section, refer to Section 2
Precautions in this Supplement and Section 00 Warnings, Cautions and Notes in the MY2005 VZ Service
Information for correct workshop practices with regard to safety and/or property damage.
The structure of the body shell has been
developed using complex design and
development techniques. In addition to
meeting all required standards, the vehicle
body is also a critical part of the overall safety
systems. It is therefore imperative the repair
procedures described here are adhered to
during all vehicle body repairs.
1 Introduction.............................................................................................................................................2
2 Body Components .................................................................................................................................3
Sedan...................................................................................................................................................................... 3
Wagon..................................................................................................................................................................... 3
Utility....................................................................................................................................................................... 4
Coupe...................................................................................................................................................................... 4
Regular Cab............................................................................................................................................................ 5
Crew Cab ................................................................................................................................................................ 5
AWD Wagon ........................................................................................................................................................... 6
3 Repair Procedures .................................................................................................................................7
3.1 Frame Straightening.............................................................................................................................................. 7
3.2 Rough Cutting........................................................................................................................................................ 8
3.3 Cutting MIG Welds................................................................................................................................................. 9
3.4 Spot Weld Cutting................................................................................................................................................ 10
3.5 Lap Jointing.......................................................................................................................................................... 11
3.6 Repairing the Body Alignment............................................................................................................................ 12
4 Weld Repair Methods...........................................................................................................................13
4.1 General Information............................................................................................................................................. 13
4.2 Spot Welding........................................................................................................................................................ 14
Spot Welder.......................................................................................................................................................... 15
Panel Condition.................................................................................................................................................... 16
Number of Welds ................................................................................................................................................. 16
Weld Testing......................................................................................................................................................... 16
4.3 Plug Welding........................................................................................................................................................ 17
4.4 Fusion Welding.................................................................................................................................................... 18
Butt Welded Joints .............................................................................................................................................. 18
Lap Welded Joints............................................................................................................................................... 18
Bronze Welds....................................................................................................................................................... 19
Warp Prevention on Long Welds........................................................................................................................ 19
4.5 Welding Legend................................................................................................................................................... 20