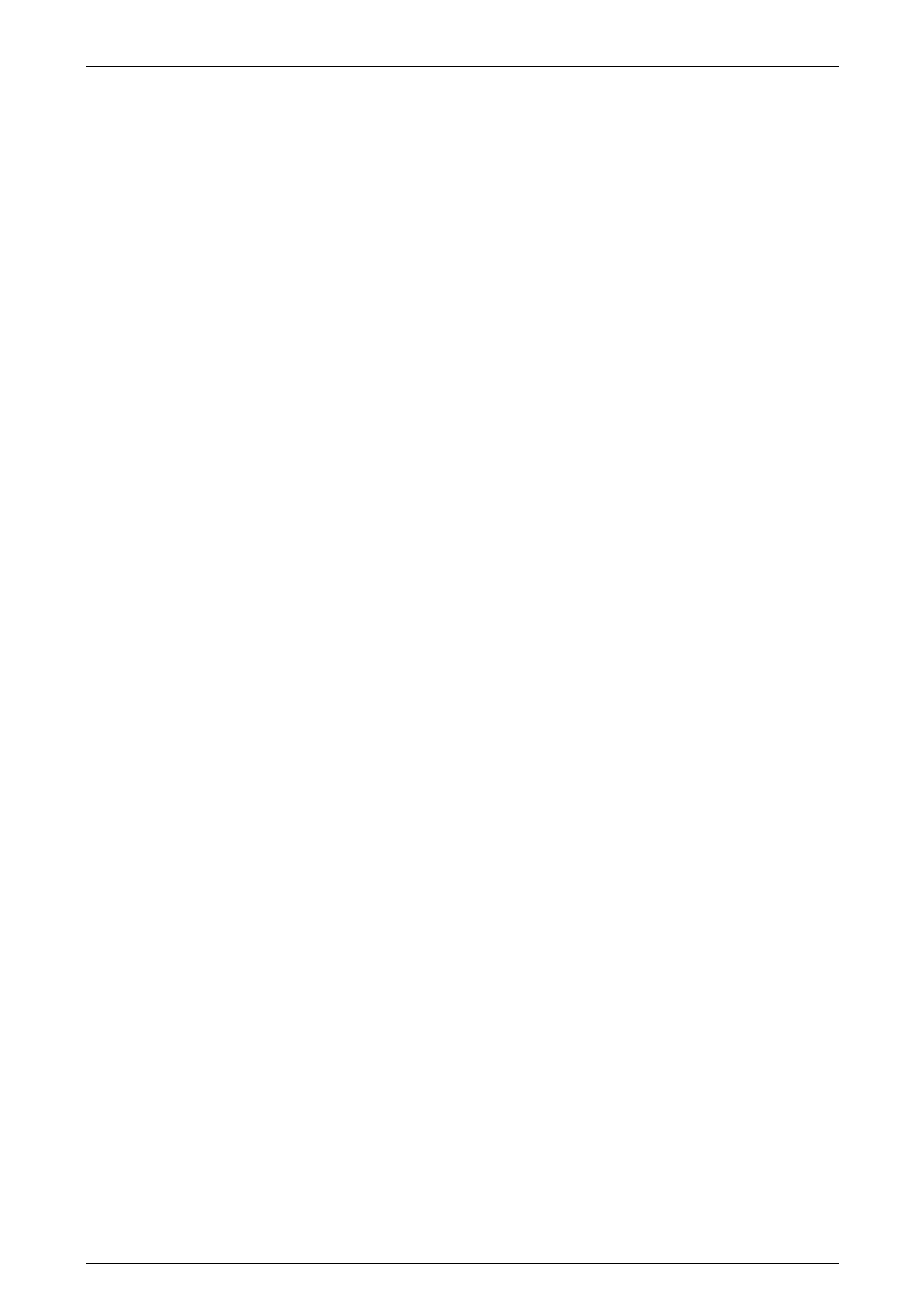
2 Precautions Page 2-2
Page 2-2
6 Jacking Precautions ............................................................................................................................22
Sedan, Wagon, Utility, Coupe and AWD Wagon ............................................................................................... 22
Regular Cab.......................................................................................................................................................... 23
Crew Cab .............................................................................................................................................................. 23
7 Towing Precautions .............................................................................................................................24
7.1 Towing On Four Wheels...................................................................................................................................... 24
7.2 Towing On Two Wheels....................................................................................................................................... 25
8 Plastic Components.............................................................................................................................26
8.1 Common to all Vehicles ...................................................................................................................................... 26
Exterior............................................................................................................................................................. 26
Interior.............................................................................................................................................................. 29
8.2 Sedan Unique....................................................................................................................................................... 31
Exterior............................................................................................................................................................. 31
Interior.............................................................................................................................................................. 31
8.3 Wagon Unique...................................................................................................................................................... 32
Exterior............................................................................................................................................................. 32
Interior.............................................................................................................................................................. 32
8.4 Utility Unique........................................................................................................................................................ 34
Exterior............................................................................................................................................................. 34
8.5 Regular Cab Unique............................................................................................................................................. 35
Exterior............................................................................................................................................................. 35
8.6 Crew Cab Unique................................................................................................................................................. 37
Exterior............................................................................................................................................................. 37
8.7 Coupe Unique....................................................................................................................................................... 39
Exterior............................................................................................................................................................. 39
8.8 AWD Wagon Unique............................................................................................................................................ 40
Exterior............................................................................................................................................................. 40
8.9 Plastic Types........................................................................................................................................................ 41
9 Special Steel Precautions....................................................................................................................42
9.1 Pre-Coated Steel.................................................................................................................................................. 42
9.2 Re-phosphorised Steel........................................................................................................................................ 43
9.3 High Strength Low Alloy Steel............................................................................................................................ 44
10 Cavity Foam..........................................................................................................................................46
Sedan and Wagon................................................................................................................................................ 47
Utility..................................................................................................................................................................... 48
Coupe.................................................................................................................................................................... 49
10.1 Cavity Foam – Replace........................................................................................................................................ 50
Hinge Pillar........................................................................................................................................................... 50
Centre Pillar, Sedan and Wagon......................................................................................................................... 50
Centre Pillar, Utility.............................................................................................................................................. 51
Centre Pillar, Coupe............................................................................................................................................. 51
Lock Pillar, Sedan................................................................................................................................................ 52
Lock Pillar, Coupe................................................................................................................................................ 52
Body Lock Pillar, Utility....................................................................................................................................... 53
Rocker Panel, Utility............................................................................................................................................ 53