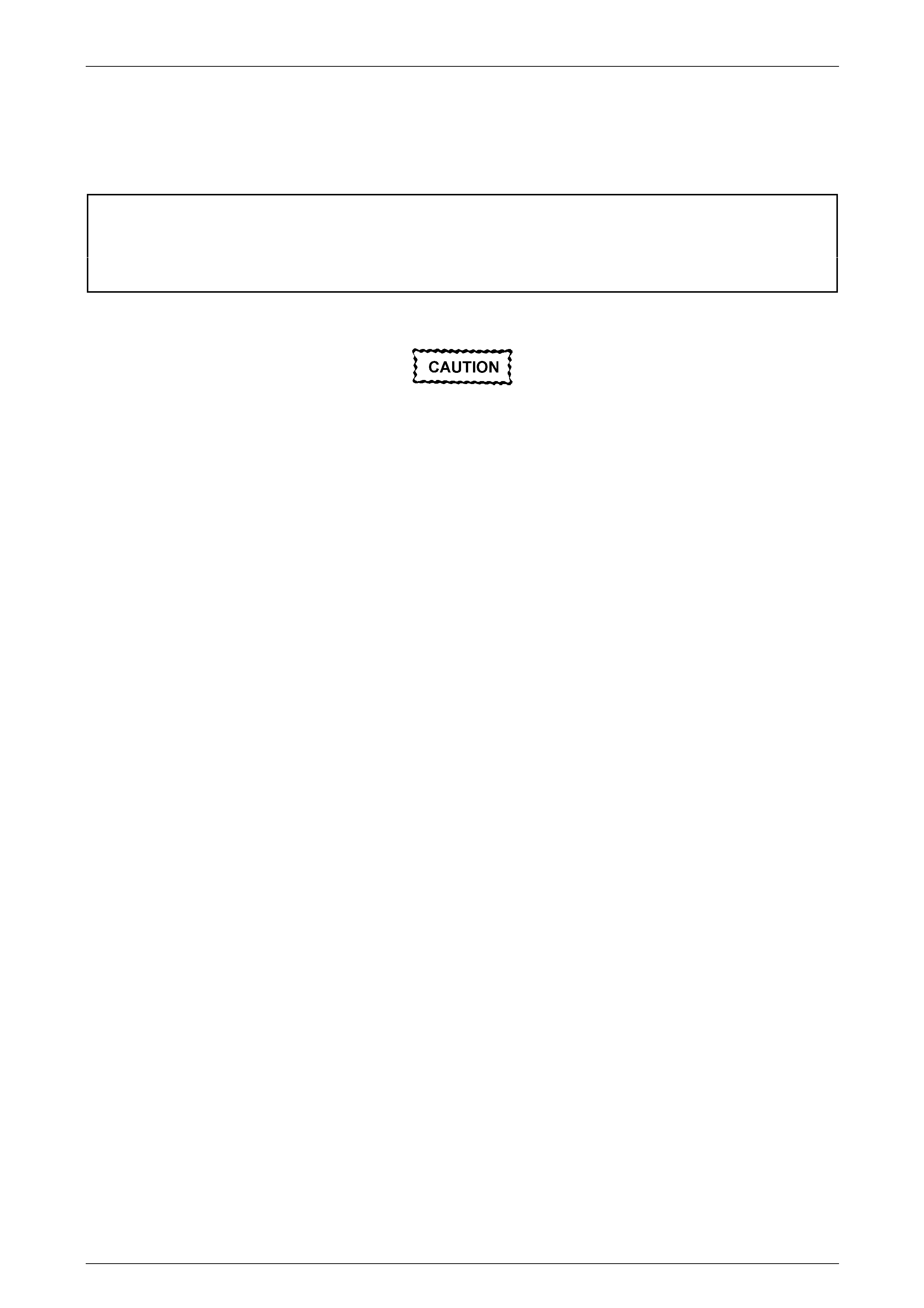
3 Body Construction Page 3–1
Page 3–1
Section 3
Body Construction
ATTENTION
Before performing any service operation or other procedure described in this Section, refer to Section 2
Precautions in this Supplement and Section 00 Warnings, Cautions and Notes in the MY2005 WL Service
Information for correct workshop practices with regard to safety and/or property damage.
The structure of the body shell has been
developed using complex design and
development techniques. In addition to
meeting all required standards, the vehicle
body is also a critical part of the overall safety
systems. It is therefore imperative the repair
procedures described here are adhered to
during all vehicle body repairs.
1 General Information ...............................................................................................................................3
1.1 Body Structure Part Refinishing........................................................................................................................... 3
1.2 Anti-Corrosive Treatment...................................................................................................................................... 4
1.3 Paint Refinishing.................................................................................................................................................... 5
Panel Refinishing................................................................................................................................................... 5
Paint Code.............................................................................................................................................................. 5
2 Body Structure Panels...........................................................................................................................6
2.1 Front End and Underbody..................................................................................................................................... 7
2.2 Upperbody Structure – Excluding Roof Structure.............................................................................................. 9
2.3 Roof Structure...................................................................................................................................................... 11
2.4 Body Structure..................................................................................................................................................... 12
3 Body Dimensions.................................................................................................................................14
3.1 Underbody Dimensions – Projected .................................................................................................................. 14
3.2 Upperbody Dimensions – Actual........................................................................................................................ 16
Front...................................................................................................................................................................... 16
Side and Interior................................................................................................................................................... 17
Rear....................................................................................................................................................................... 18
4 Body Margins........................................................................................................................................19
5 Body Sealing, Adhesives And Deadeners.........................................................................................22
5.1 Acrylic Spot Weld Sealer (Item 2)....................................................................................................................... 24
Acrylic Spot Weld Sealer (Item 2) Continued .................................................................................................... 25
5.2 Joint Sealer (Item 3)............................................................................................................................................. 26
Joint Sealer (Item 3) Continued.......................................................................................................................... 27
Joint Sealer (Item 3) Continued.......................................................................................................................... 28
Joint Sealer (Item 3) Continued.......................................................................................................................... 29
Joint Sealer (Item 3) Continued.......................................................................................................................... 30
Joint Sealer (Item 3) Continued and Hand Putty (Item 4) ................................................................................. 31