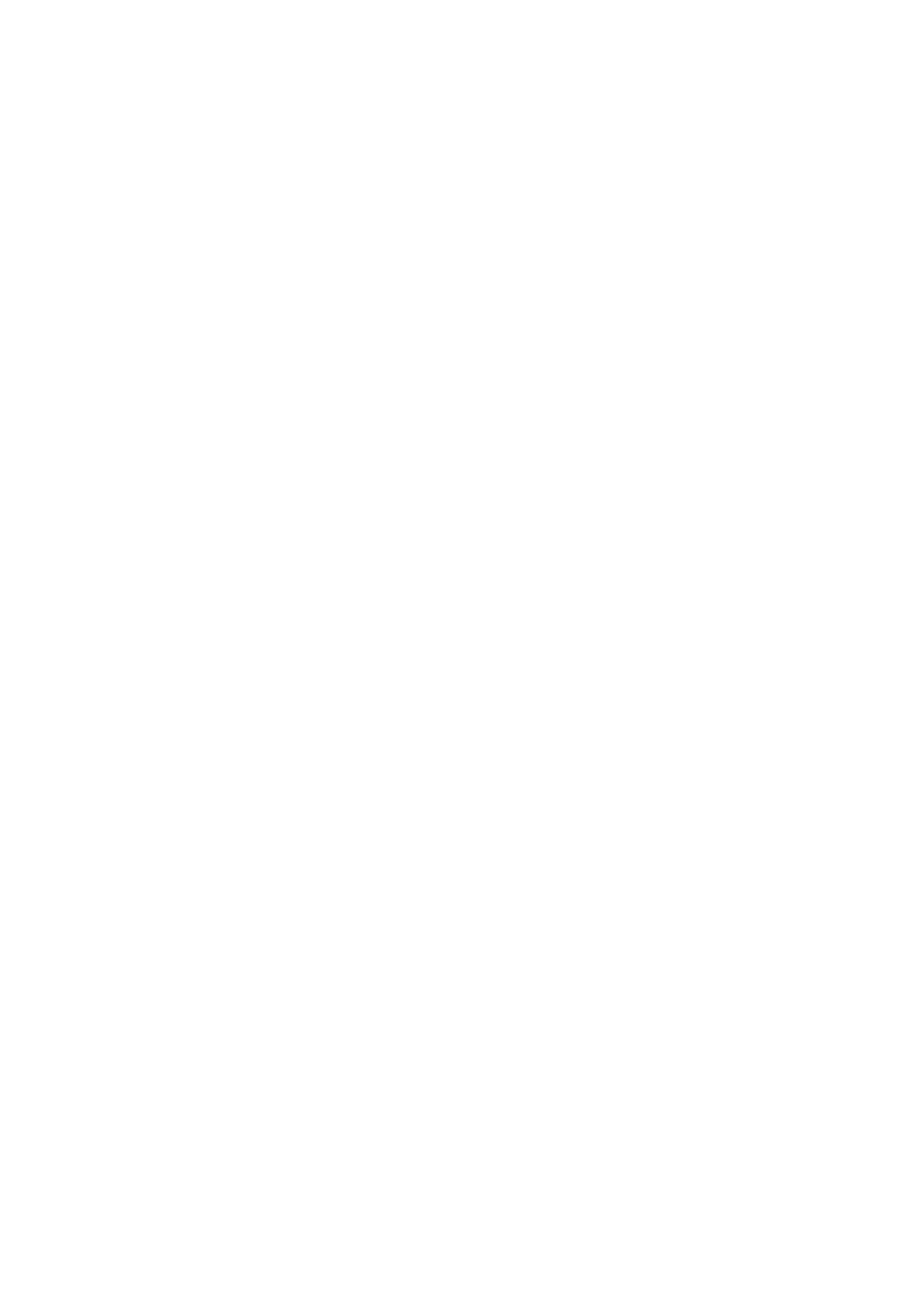
4.4 OPS SAFETY PRECAUTIONS
• Do not use a fast battery charger for starting the vehicle.
• Never disconnect the battery from the vehicle’s electrical system while the engine is running.
• Disconnect the battery from the vehicle’s electrical system before fast battery charging.
• Never disconnect or connect the SDM connector with the ignition turned on.
• After an accident, always replace the individual OPS com ponents. Refer to 4.2 REPAIRS AND INSPECTI ONS
REQUIRED AFTER A COLLISION in this Section.
NOTE: Damaged or defective components must always be replaced with new parts.
• Always reinstall fasteners in the same location from which they were removed, using the correct tightening
torque where given. If the fastener needs replacing, replace it with the correct part number.
• Because the strength of the windshield and its urethane adhesive is critical to the correct deployment
of the airbag, always replace these items with parts complying to the correct specification, refer to
Section 1A6 STATIONARY WINDOWS in the MY2003 VY Series & V2 Series II Service information.
Failure to use the c orrect product m ay res ult in poor retention of the glass. For vehicles with a front pass enger
airbag, the windshield must be replaced correctly to ensure the occupant protection provided by the OPS is
maintained as the windshield supports the passenger airbag during deployment.
• Take c are when handling the side impact sens or. Never strik e or jar the sensor or adjacent body st ructure in a
manner which could cause deployment of the side airbag. Never carry a peripheral acceleration sensor by the
wiring harness leads.
If a peripheral acceleration sensor is dropped from a height greater than one metre, it must be replaced.
• Take c are when handling the SDM. Never strik e or j ar the m odule or body struc ture adjacent to the module in a
manner which could cause deployment of the pretensioners or inflatable restraints.
• When c ar rying a live (undeployed) inf latable res tr aint module, ens ur e that it is always pointed away from you. In
case of an accidental deployment, the likelihood of injury from the airbag is minimised.
• W hen placing a live inflatable res traint module on a bench or other surf ace, always face the assembly up. T his
will provide f ree s pace f or the inflatable rest raint to expand in case of accidental deployment. Also, never place
anything on top of the inflatable restraint module.
• Never carry the pretens ioners, driver ’s inf latable r estraint module, f ront pass enger inf latable restr aint m odule or
side inflatable restraints module by their wiring harness leads.
• Do not apply power to a module except as specified in the MY2003 VY Series & V2 Series II Service
Information.
• Do not attempt to m ake any repairs or modifications to a module or sensor. A dam aged or defective horn bar
and driver airbag inflator module, front passenger airbag inflator module or side airbag inflator module must
only be replaced with new parts.
• Always wear gloves and safety glasses when handling a deployed pretensioner or inflatable restraint module.
The surface of these components may contain chemicals (e.g. sodium hydroxide) as a result of the gas
generated during combustion. This can irritate the skin. Wash hands with mild soap and water after handling.
• Refer to Section 12M, OCCUPANT PROTECTION SYSTEM in the MY2003 VY Series & V2 Series II Service
Information for detailed service procedures and precautions.