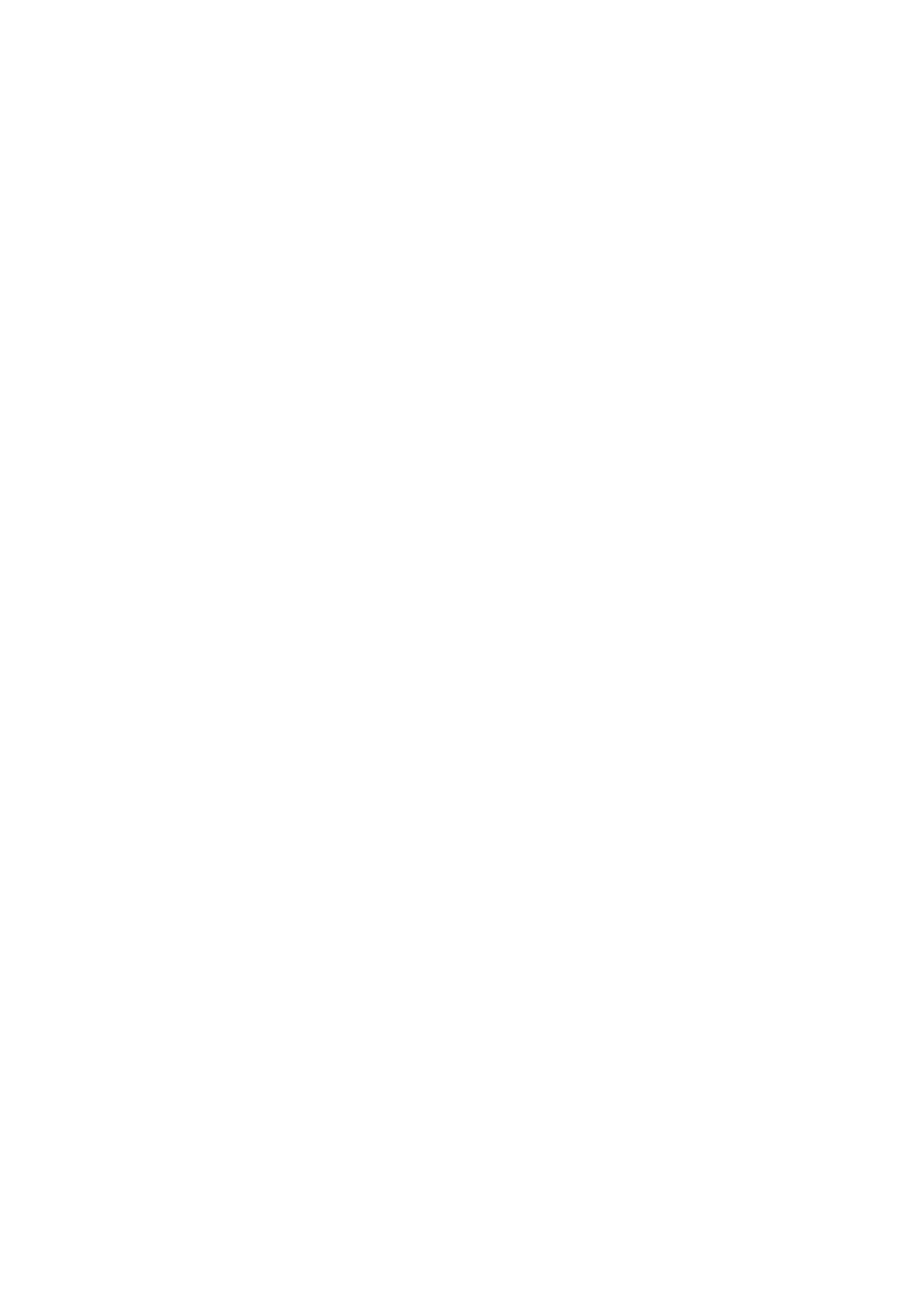
1.2 ANTI-CORROSIVE TREATMENT
Precoated and galvanised steel is used extensively for various body structure components for increased corrosion
protection. Body panels such as the engine hood, door and deck lid outer panels ar e precoated on the inner surf ace
of the metal to improve corrosion protection. Other body structure members have complete double-sided galvanised
protection.
In addition, a rust preventative material (cavity wax) is sprayed after paint application to areas such as the interior
surfaces of doors, etc. Refer to 6. CAVITY WAX in Section, 3A – Sedan, 3B – Wagon, 3C – Utility or 3D – Coupe.
Any repair or replacement of panels, assemblies, etc. that disturb this anti-corrosive treatment must be resealed
and should be included as part of the repair or replacement operation.
Anti-corrosive compounds used for repairs should be light bodied materials designed to penetrate between metal-
to-metal surfaces such as pinch weld flanges and integral panel attaching points.
All bare metal sur f ac es must be tr eated with metal conditioner and pr imed. T hes e operations need to be c arr ied out
prior to the application of sealer s, waxes and s ound deadeners. Attac hing points of new replacem ent panels s hould
be resealed. T he hemm ing flanges of replacem ent doors, lif tgates, endgates and r ear compartm ent lids will require
resealing.
Open joins that require bridging of the sealer to close a gap should be sealed with a heavy-bodied caulking material.
When colour application is required to restore repaired areas to original appearance, conventional refinishing
preparation, undercoat build-up and colour application techniques should be employed.
When deadeners are disturbed during damage repair, or a panel has been replaced, the deadener material must be
replaced with an equivalent material. The location and pattern for replacement material can be determined by
observing the original deadener application outlines. Refer to 5. BODY SEALING, ADHESIVES & DEADENERS, in
Section, 3A – Sedan, 3B – Wagon, 3C – Utility or 3D – Coupe.