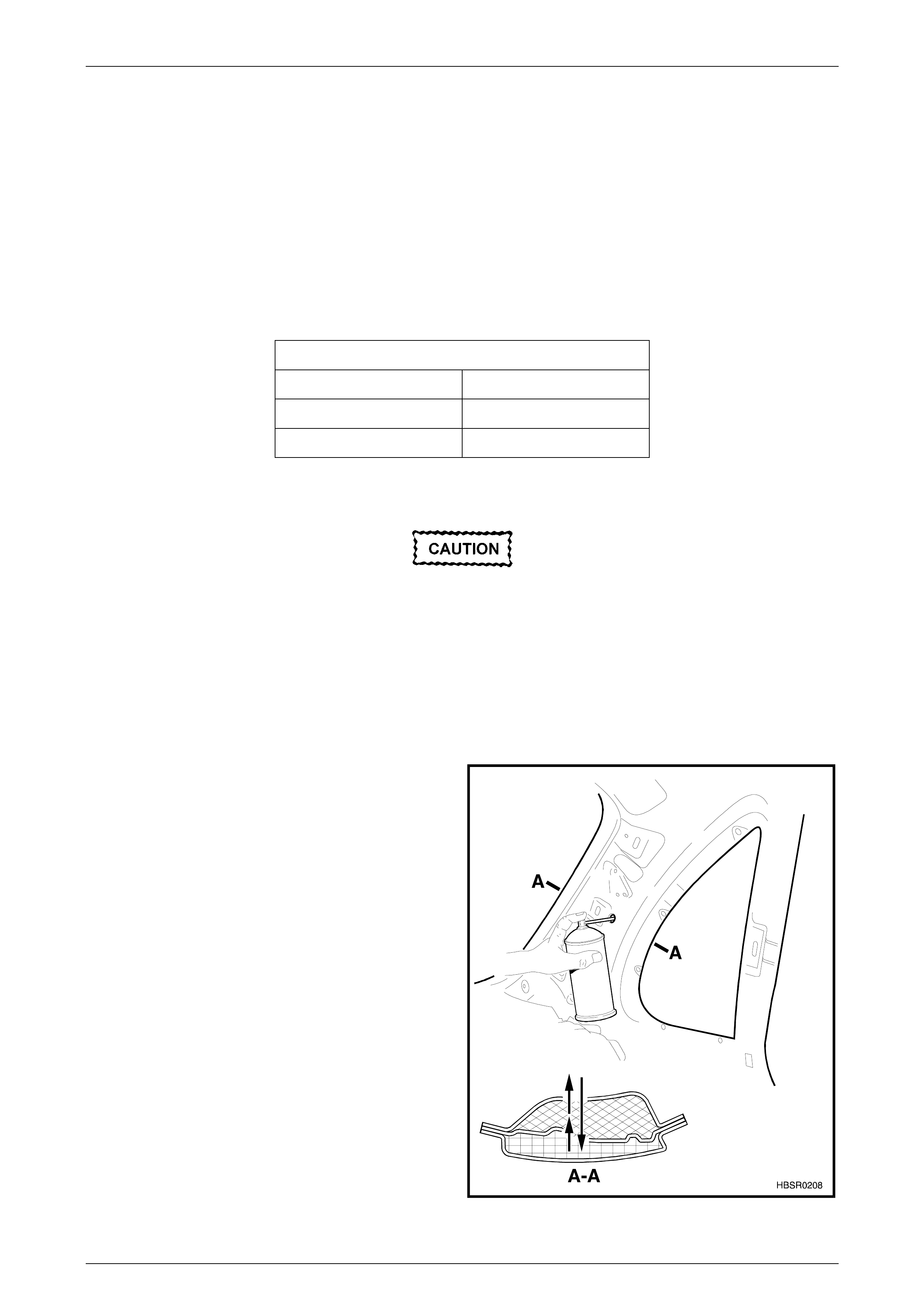
Precautions Page 2–11
Page 2–11
3 Cavity Foam
To reduce noise transmittence, cavity foam blocks are placed in the hinge, centre, lock and back lock pillars during
production. This material, when subjected to a temperature of approximately 160°C, expands up to 10 times its original
size to seal the cavity.
The use of this material posses no health and safety risk to a repairer, unless it is heated to temperatures associated
with heating using oxy / acetylene equipment or welding, as toxic fumes will be emitted which must not be inhaled.
Prior to welding or heating in the areas filled with cavity foam, the foam must first be removed - usually by cutting it out
with a knife, refer to Figure 2 – 7.
If a panel or section is replaced or repair work is carried out where the foam is removed, it must be replaced with a
commercially available equivalent, such as those listed, using the following procedure.
Cavity Foam Equivalents
Brand Product
Sista Multi Purpose Foam
Selleys Space Invader
Replace
Take care not to drill into the outer panel.
1 For the hinge, centre and lock pillar, drill a hole in the quarter panel inner assembly at the section areas, refer to
Figure 2 – 7, as required. The hole size should be similar to the diameter of the nozzle supplied with the
replacement foa m.
2 Insert the nozzle into the drilled hole and spray foam into the cavity for several seconds to fill the area to a height of
approximately 50 mm.
3 For the back lock pillar, two cavity blocks are installed, refer to D, Figure 2 – 7. Drill a hole in the quarter panel inner
assembly at Section D-D and carefully continue drilling a further hole through the back lock pillar reinforcement.
4 Insert the nozzle into the drilled hole through the
quarter panel inner assembly and back lock pillar
reinforcement and spray foam into the cavity between
the outer panel and back lock pillar reinforcement for
several seconds to a height of approximately 50 mm.
5 Retract the nozzle into the cavity between the back
lock pillar reinforcement and quarter panel inner
assembly and spray foam to fill this cavity for several
seconds to a height of approximately 50 mm.
Figure 2 – 6