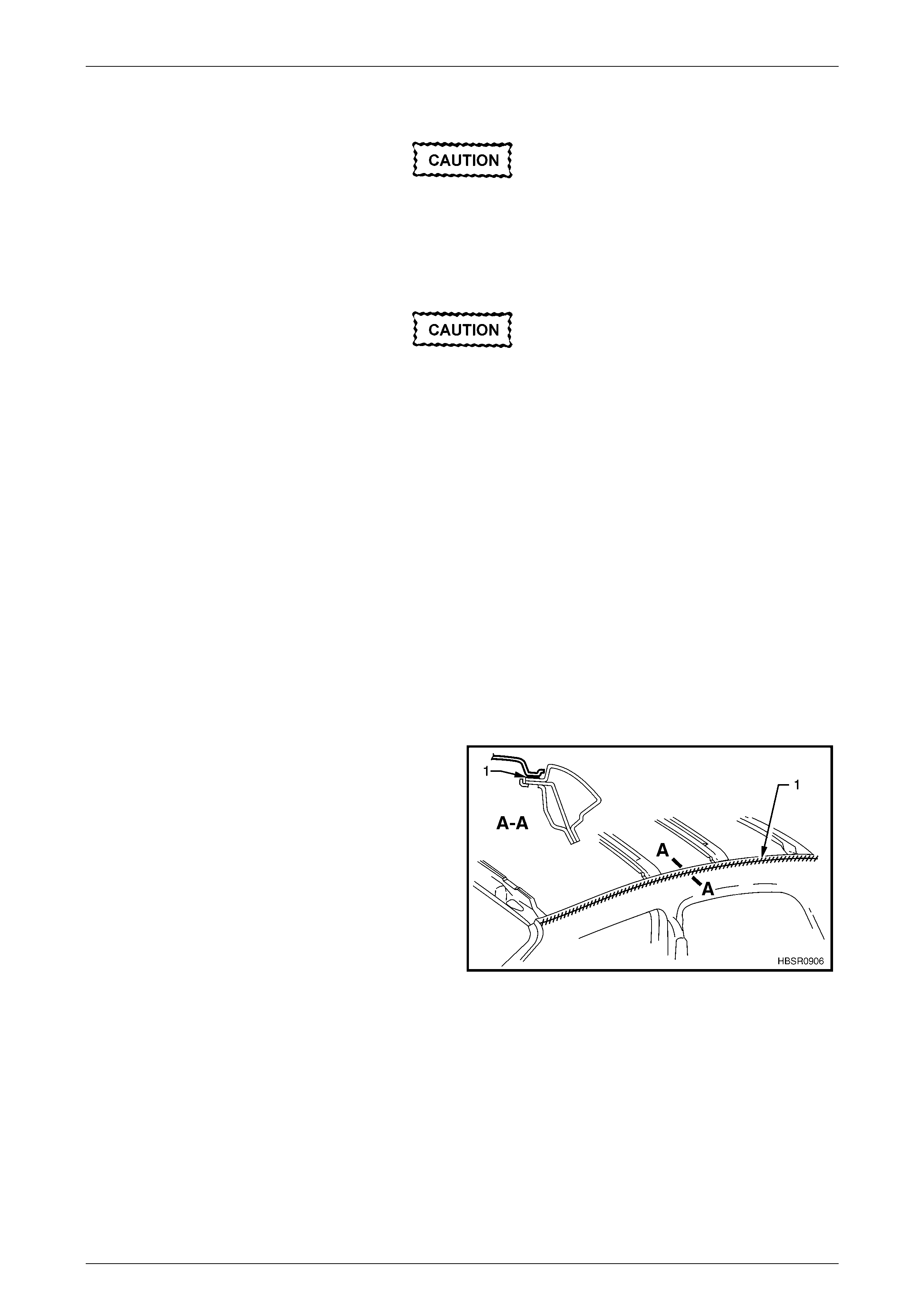
Roof Panel Page 9–6
Page 9–6
Replace
The same number and position of spot welds
(or plug welds) should be used when
replacing the panel, as was used during
manufacture, in order to maintain the original
structural strength of the vehicle.
When welding a relatively flat panel such as
the roof panel, due care must be taken to
minimise the heat absorbed by the panel
which could lead to panel distortion.
NOTE
Spot welding is the preferred method for
attaching of panels and should be used whenever
possible. Where the spot welding equipment
available to the repairer will not access the
required weld position, a plug weld should be
performed.
1 Clean the remaining anti-flutter adhesive from the surfaces of the header rail, roof rear frame and support panel.
2 Prepare the mating surface areas for welding. Dress the channel flange area, the windshield header rail and the
roof rear frame, so they are flat and free from imperfections.
3 Treat the front and rear mating surfaces with Weld Through Primer (Item 1) as required. Refer to Section 3, 5 Body
Sealing, Adhesives & Deadeners.
4 Mark the new roof panel with drilling locations, where plug welding is necessary. Drill holes as required.
5 Apply Structural adhesive (Item 6) (1) to the mating
surfaces of the roof panel and door opening frame.
Refer to Section 3, 5 Body Sealing, Adhesives &
Deadeners.
6 Apply a bead of Anti-flutter adhesive (Item 5) to the full
length of the groove in the windshield header (section
A-A) and the groove in the rear roof frame (section C-
C), refer to Figure 9 – 9. Refer to Section 3, 5 Body
Sealing, Adhesives & Deadeners.
7 Apply two full length beads of Anti-flutter adhesive to
the grooves in the roof supports (section B-B).
Figure 9 – 8