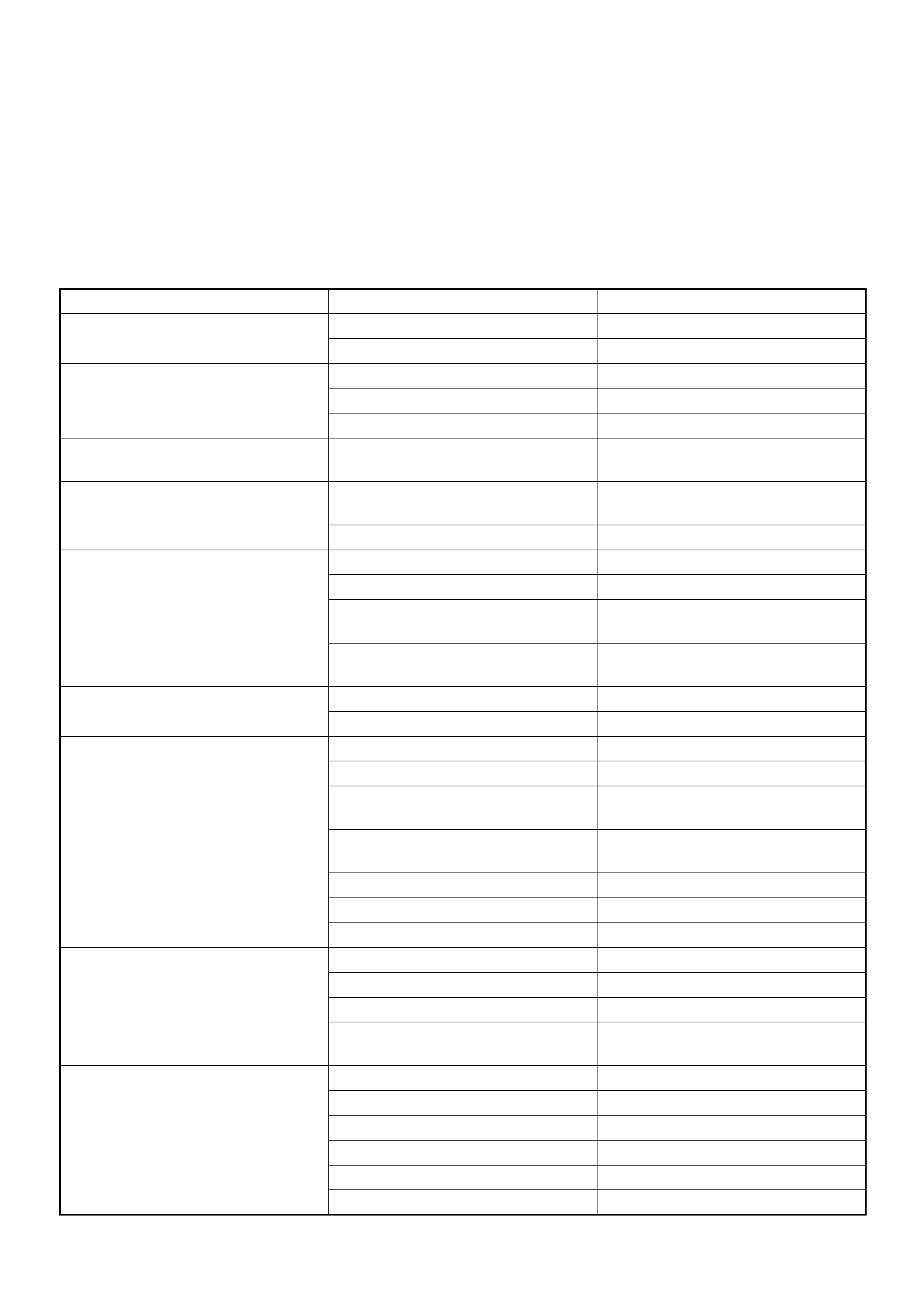
General Description
This publication contains essential removal, installation,
adjustment and maintenance procedures.
The front axle utilizes a central disconnect type front
axle/transfer case system.
The drive axles are completely flexible assemblies,
consisting of inner and outer constant velocity (CV)
drive shaft joints connected by an axle shaft.
For description of front propeller shaft and universal
joint, refer to Front Propeller Shaft in this section.
Diagnosis
Condition Possible cause Correction
Oil Leak At Front Axle Worn or defective oil seal. Replace the oil seal.
Front axle housing cracked. Repair or replace.
Oil Leak At Pinion Shaft Too much gear oil. Correct the oil level.
Oil seal worn or defective. Replace the oil seal.
Pinion flange loose or damaged. Tighten or replace.
Noises In Front Axle Drive Shaft
Joint
Broken or worn drive shaft joints and
bellows (BJ and DOJ).
Replace the drive shaft joints and
bellows.
“Clank" When Accelerating From
“Coast"
Loose drive shaft joint to output
shaft bolts.
Tighten.
Damaged inner drive shaft joint. Replace.
Shudder or Vibration During
Acceleration
Excessive drive shaft joint angle. Repair.
Worn or damaged drive shaft joints. Replace.
Sticking spider assembly (inner
drive shaft joint).
Lubricate or replace.
Sticking joint assembly (outer drive
shaft joint).
Lubricate or replace.
Vibration At Highway Speeds Out of balance or out of round tires. Balance or replace.
Front end out of alignment. Align.
Noises in Front Axle Insufficient gear oil. Replenish the gear oil.
Wrong or poor grade gear oil. Replace the gear oil.
Drive pinion to ring gear backlash
incorrect.
Adjust the backlash.
Worn or chipped ring gear, pinion
gear or side gear.
Replace the ring gear, pinion gear or
side gear.
Pinion shaft bearing worn. Replace the pinion shaft bearing.
Hub unit bearing worn. Replace the hub unit bearing.
Differential bearing loose or worn. Tighten or replace.
Wanders and Pulls Incorrect front alignment. Adjust the front alignment.
Steering unit loose or worn. Tighten or replace.
Tire worn or improperly inflated. Adjust the inflation or replace.
Front or rear suspension parts loose
or broken.
Tighten or replace.
Front Wheel Shimmy Hub unit bearing worn. Replace.
Incorrect front alignment. Adjust the front alignment.
Worn ball joint or bush. Replace the ball joint or bush.
Steering unit loose or worn. Tighten or replace.
Tire worn or improperly inflated. Replace or adjust the inflation.
Shock absorber worn. Replace the shock absorber.