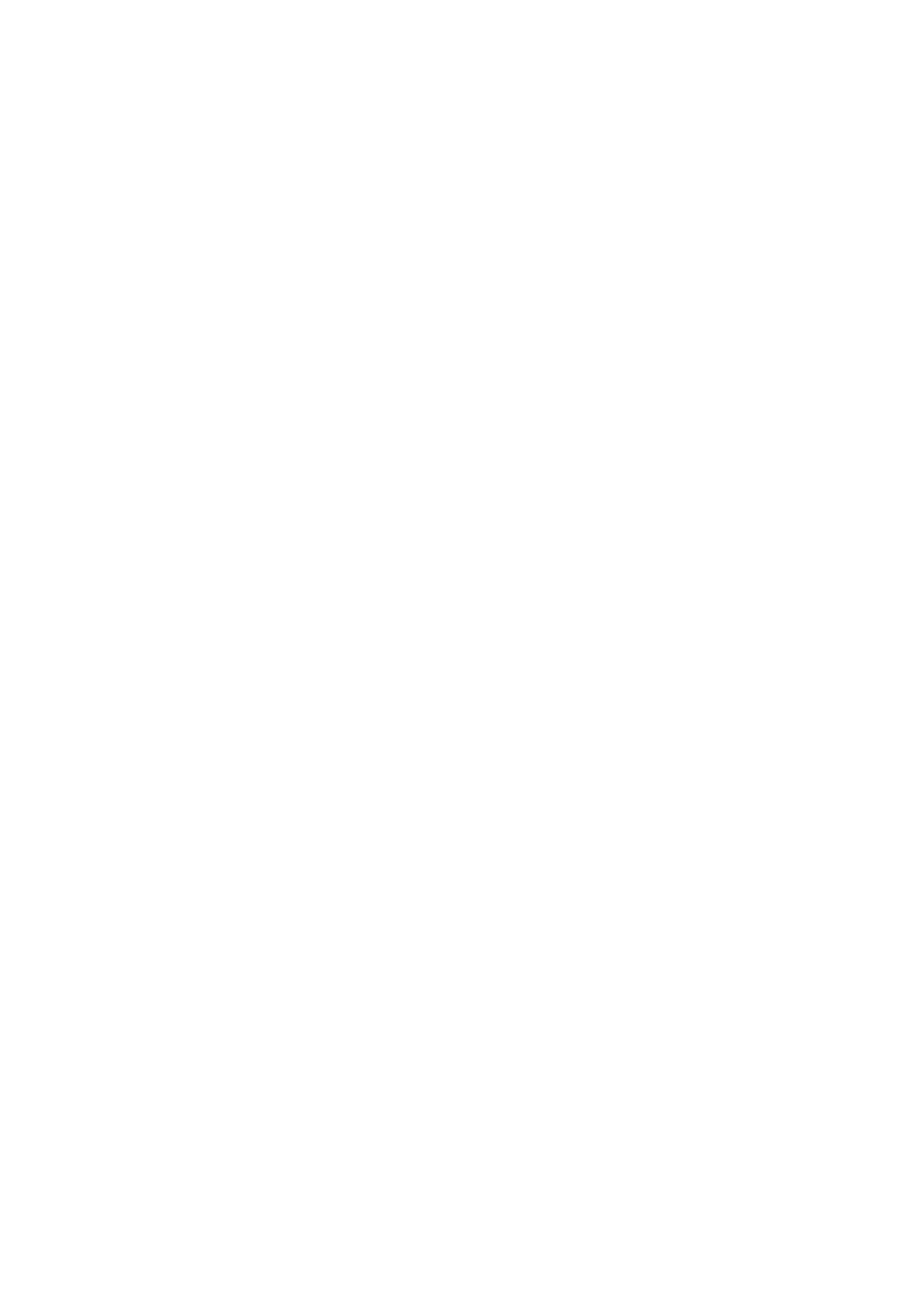
Diagnosis
Many noises that seem to come from the rear axle
actually originate from other sources such as tyres, road
surface, wheel bearings, engine, transmission, muffler,
or body drumming. Investigate to find the source of the
noise before disassembling the rear axle. Rear axles,
like any other mechanical device, are not absolutely
quiet but should be considered quiet unless some
abnormal noise is present.
To make a systematic check for axle noise, observe the
following:
1. Select a level asphalt road to reduce tyre noise and
body drumming.
2. Check rear axle lubricant level to assure correct
level, and then drive the vehicle far enough to
thoroughly warm up the rear axle lubricant.
3. Note the speed at which noise occurs. Stop the
vehicle and put the transmission in neutral. Run the
engine speed slowly up and down to determine if
the noise is caused by exhaust, muffler noise, or
other engine conditions.
4. Tyre noise changes with different road surfaces;
axle noises do not. Temporarily inflate all tyres to
344 kPa (50 psi) (for test purposes only). This will
change noise caused by tyres but will not affect
noise caused by the rear axle.
Rear axle nose usually stops when coasting at
speeds under 48 km/h (30 mph); however, tyre
noise continues with a lower tone. Rear axle noise
usually changes when comparing pull and coast, but
tyre noise stays about the same.
Distinguish between tyre noise and rear axle noise
by noting if the noise changes with various speeds
or sudden acceleration and deceleration. Exhaust
and axle noise vary under these conditions, while
tyre noise remains constant and is more
pronounced at speeds of 32 to 48 km/h (20 to 30
mph). Further check for tyre noise by driving the
vehicle over smooth pavements or dirt roads (not
gravel) with the tyres at normal pressure. If the
noise is caused by tyres, it will change noticeably
with changes in road surface.
5. Loose or rough front wheel bearings will cause
noise which may be confused with rear axle noise;
however, front wheel bearing noise does not change
when comparing drive and coast. Light application
of the brake while holding vehicle speed steady will
often cause wheel bearing noise to diminish. Front
wheel bearings may be checked for noise by jacking
up the wheels and spinning them or by shaking the
wheels to determine if bearings are loose.
6. Rear suspension rubber bushings and spring
insulators dampen out rear axle noise when
correctly installed. Check to see that there is no link
or rod loosened or metal–to–metal contact.
7. Make sure that there is no metal–to–metal contact
between the floor and the frame.
After the noise has been determined to be in the axle,
the type of axle noise should be determined, in order to
make any necessary repairs.
Gear Noise
Gear noise (whine) is audible from 32 to 89 km/h (20 to
55 mph) under four driving conditions.
1. In drive under acceleration or heavy pull.
2. Driving under load or under constant speed.
3. When using enough throttle to keep the vehicle from
driving the engine while the vehicle slows down
gradually (engine still pulls slightly).
4. When coasting with the vehicle in gear and the
throttle closed. The gear noise is usually more
noticeable between 48 and 64 km/h (30 and 40
mph) and 80 and 89 km/h (50 and 55 mph).
Bearing Noise
Bad bearings generally produce a rough growl or
grating sound, rather than the whine typical of gear
noise. Bearing noise frequently “wow–wows" at bearing
rpm, indicating a bad pinion or rear axle side bearing.
This noise can be confused with rear wheel bearing
noise.
Rear Wheel Bearing Noise
Rear wheel bearing noise continues to be heard while
coasting at low speed with transmission in the neutral.
Noise may diminish by gentle braking. Jack up the rear
wheels, spin them by hand and listen for noise at the
hubs. Replace any faulty wheel bearings.
Knock At Low Speeds
Low speed knock can be caused by worn universal
joints or a side gear hub counter bore in the cage that is
worn oversize. Inspect and replace universal joints or
cage and side gears as required.
Backlash Clunk
Excessive clunk on acceleration and deceleration can
be caused by a worn rear axle pinion shaft, a worn
cage, excessive clearance between the axle and the
side gear splines, excessive clearance between the
side gear hub and the counterbore in the cage, worn
pinion and side gear teeth, worn thrust washers, or
excessive drive pinion and ring gear backlash. Remove
worn parts and replace as required. Select close–fitting
parts when possible. Adjust pinion and ring gear
backlash.