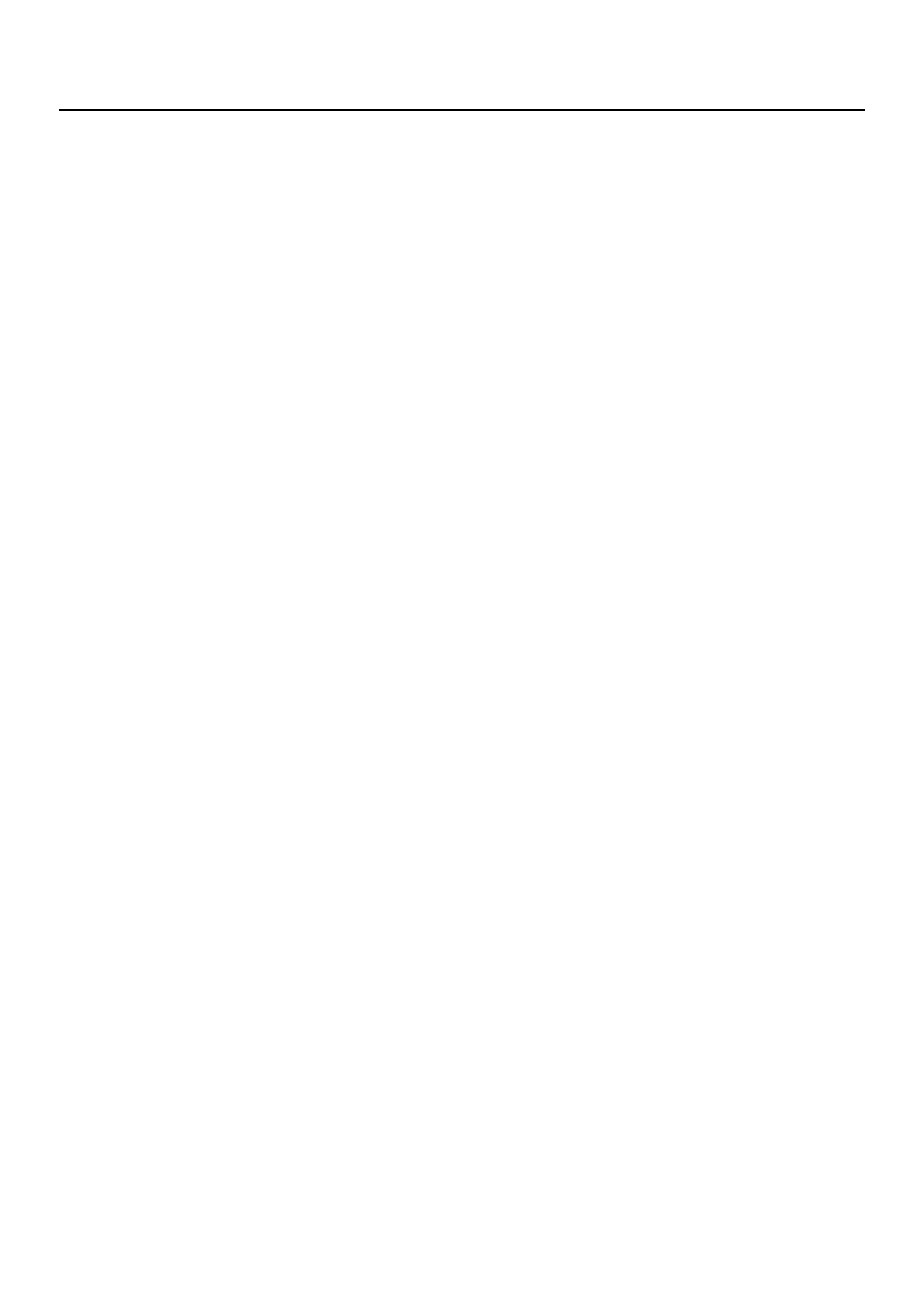
DIAGNOSTIC INFORMATION
Diagnostic Procedures
WARNING: WHEN FASTENERS ARE REMOVED,
ALWAYS REINSTALL THEM IN THE SAME
LOCATION FROM WHICH THEY WERE REMOVED.
IF A FASTENER NEEDS TO BE REPLACED, USE
THE CORRECT PART NUMBER FASTENER FOR
THAT APPLICATION. IF THE CORRECT PART
NUMBER FASTENER IS NOT AVAILABLE, A
FASTENER OF EQUAL SIZE AND STRENGTH (OR
STRONGER) MAY BE USED. FASTENERS THAT
ARE NOT REUSED, AND THOSE REQUIRING
THREAD LOCKING COMPOUND WILL BE CALLED
OUT. THE CORRECT TORQUE VALUE MUST BE
USED WHEN INSTALLING FASTENERS THAT
REQUIRE IT. IF THE ABOVE CONDITIONS ARE NOT
FOLLOWED, PARTS OR SYSTEM DAMAGE COULD
RESULT.
WARNING: TO AVOID DEPLOYMENT WHEN
TROUBLESHOOTING THE SRS, DO NOT USE
ELECTRICAL TEST EQUIPMENT SUCH AS A
BATTERY–POWERED OR AC–POWERED
VOLTMETER, OHMMETER, ETC., OR ANY TYPE OF
ELECTRICAL EQUIPMENT OTHER THAN THAT
SPECIFIED IN THIS MANUAL. DO NOT USE A
NONPOWERED, PROBE–TYPE TESTER.
INSTRUCTIONS IN THIS MANUAL MUST BE
FOLLOWED CAREFULLY, OTHERWISE PERSONAL
INJURY MAY RESULT.
The diagnostic procedures used in this section are
designed to aid in finding and repairing SRS problems.
Outlined below are the steps to find and repair SRS
problems quickly and effectively. Failure to carefully
follow these procedures may result in extended
diagnostic time, incorrect diagnosis and incorrect parts
Replacement.
1. Perform The “SRS Diagnostic System Check."
The “Supplemental Restraint System (SRS)
Diagnostic System Check" should always be the
starting point of any SRS diagnostics. The “SRS
Diagnostic System Check" checks for proper “AIR
BAG" warning lamp operation and checks for SRS
trouble codes using both “Flash Code" and “Scan
Tool" Methods.
2. Refer To The Proper Diagnostic Chart As
Directed By The “SRS Diagnostic System
Check."
The “SRS Diagnostic System Check" will lead you
to the correct chart to diagnose any SRS problems.
Bypassing these procedures may result in
extended diagnostic time, incorrect diagnosis and
incorrect parts Replacement.
3. Repeat the “SRS Diagnostic System Check"
After Any Repair Or Diagnostic Procedures
Have Been Perfor med .
Performing the “SRS Diagnostic System Check"
after all repair or diagnostic procedures will assure
that the repair has been made correctly and that no
other conditions exist.
Diagnostic Codes
The Sensing and Diagnostic Module (SDM) maintains a
history record of all diagnostic codes that have been
detected since the SRS codes were last cleared during
service.
1. Active Codes—Faults that are presently detected
this ignition cycle. Active codes are stored in
Random Access Memory (RAM).
2. History Codes—All faults detected since the last
time the history fault memory was cleared. History
codes are stored in Electronically Erasable
Program m ab le Read only Mem ory (EEP RO M).
How To Read Trouble Codes
All codes (Active and history) can be read (or cleared)
by using a scan tool or equivalent.
How To Clear Trouble Codes
T rouble codes can only be cleared by using a scan tool.
If a scan tool is not available then inform the owner of
the stored codes and suggest that the codes are
cleared upon the next visit to a dealership.
Scan Tool Diagnostics
A scan tool can be used to read current and history
codes and to clear all history codes after a repair is
complete. The scan tool must be updated to
communicate with the SRS through a replaceable
cartridge for SRS diagnostics. To use the scan tool,
connect it to the Data Link Connector (DLC) and turn
the ignition switch “ON". Then follow the manufacturer's
directions for communication with the SRS. The scan
tool reads serial data from the Sensing and Diagnostic
Module (SDM) “Serial Data" output (terminal 24) to the
DLC.
Basic Knowledge Required
Before using this section of the Service Manual, there is
some basic knowledge which will be required. Without
this knowledge, you will have trouble using the
diagnostic procedures in this section. Use care to
prevent harm or unwanted deployment. Read all
cautions in the service manual and on warning labels
attached to SRS components.
Basic Electrical Circuits
You should understand the basic theory of electricity
including series and parallel circuits, and understand the
volt age dr ops ac ross se ri es re sist o rs. You s hou ld k now
the meaning of voltage (volts), current (amps), and
resistance (ohms). You should understand what
happens in a circuit with an open or a shorted wire. You
should be able to read and understand a wiring
diagram.