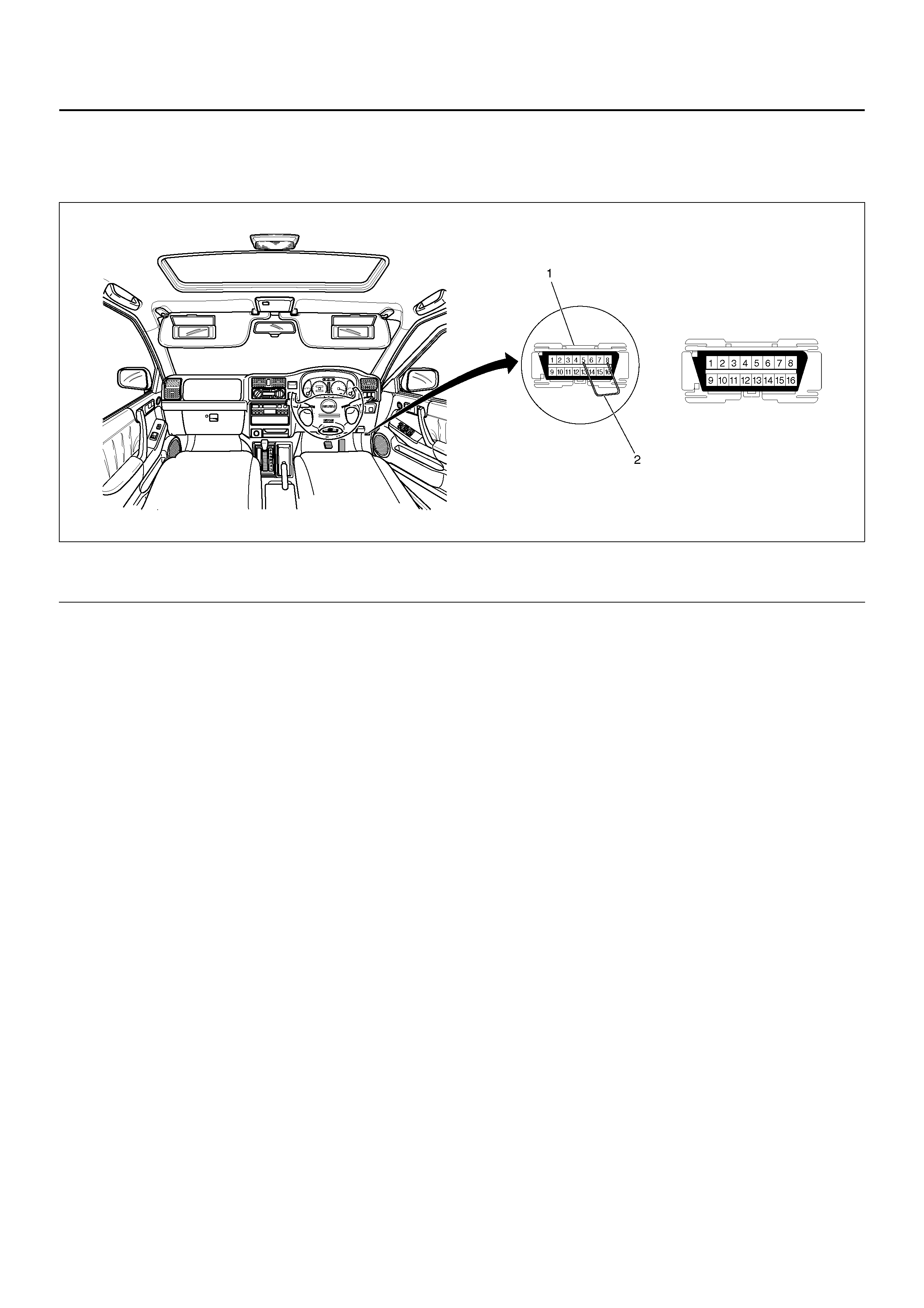
Clearing Diagnostic Trouble Codes
1) Bridge terminals 5 & 8 of the DLC.
2) Turn on the ignition ON and remove DLC bridge.
3) Verify the DTC’s have been cleared
350R100005
EndOFCallout
Diagnostic Precautions
Replacement of Control Unit
The control unit itself rarely fails. In most cases, the
harnesses have failed (i.e. short-circuit), resulting in a
secondary failure. In other cases the exact cause
unknown due to intermittent nature of the fault and the
fault is removed accidentally along with replacement of
control unit.
Therefore, before replacing the control unit, always
check the harness connectors and whether a short
circuit has resulted in excessive current flow damaging
the ECU.
Intermittent Faults
Intermittent faults are mostly attributal to the improper
wiring harness and connector failure.
When intermittent troubles are occur, check the
associated circuit according to the following procedure.
1. Check that the connectors are correctly mated and
that the connector terminals are completely
engaged.
2. Check for deformed or damaged the terminals.
Repair or replace the terminals and reconnect the
terminals securely.
3. Check for broken wires in the harness. Perform a
contin uity check while wriggling the harness, looing
for any indication of an open circuit. Take care not to
use excessive force which may damage the
harness.
Test Run of Failed TOD Vehicle
If the TOD indi cator lamps e xperience d faulty o peration
even once in the past, the failed portion can be
identified by use of the procedure “Diagnosis from
T rouble Codes" or “Trouble Diagnosis Depending on the
Status of TOD Indicator". If the troubles that are only
recognized as abnormal phenomena of the vehicle by
the driver are observed, conduct the test run in the
followi ng procedure to reproduce the faul ty phenomena
and diagno se the fault for each phenome non.
1. Start the engine, and check that the TOD indicator
lamps are tur ned on for about two se conds for initi al
check; the CHECK lamp goes off; and the TOD
indica tor lamps display the specifie d drive mode. (I f
the CHECK lamp starts blinking, read the trouble
codes and identify the failed portion.)
2. While keeping the vehicle standstill, operate the
TOD switch to change the modes: 2H mode→TOD
mode→4L mode→TOD mode→2H mode. Check
that the TOD indicator lamps correctly display the
status whenever the mode is changed. If the
transition status is displayed during the shift
operation, run the vehicle a little to complete
shifting.
3. Slowly start the vehicle in the TOD mode, and add
the power to accelerate to at least 40 km/h (25
mph)an d maintain the speed for about two minutes .
Apply the brake to completely stop the vehicle.
Repeat this test pattern at least three times.
4. Turn the stee ring to the r ight end (or left end) in the
TOD mode, a nd sl owly start th e v ehi cle a nd mak e a
Legend
(1) Data Link Connector (2) Jumper Wire