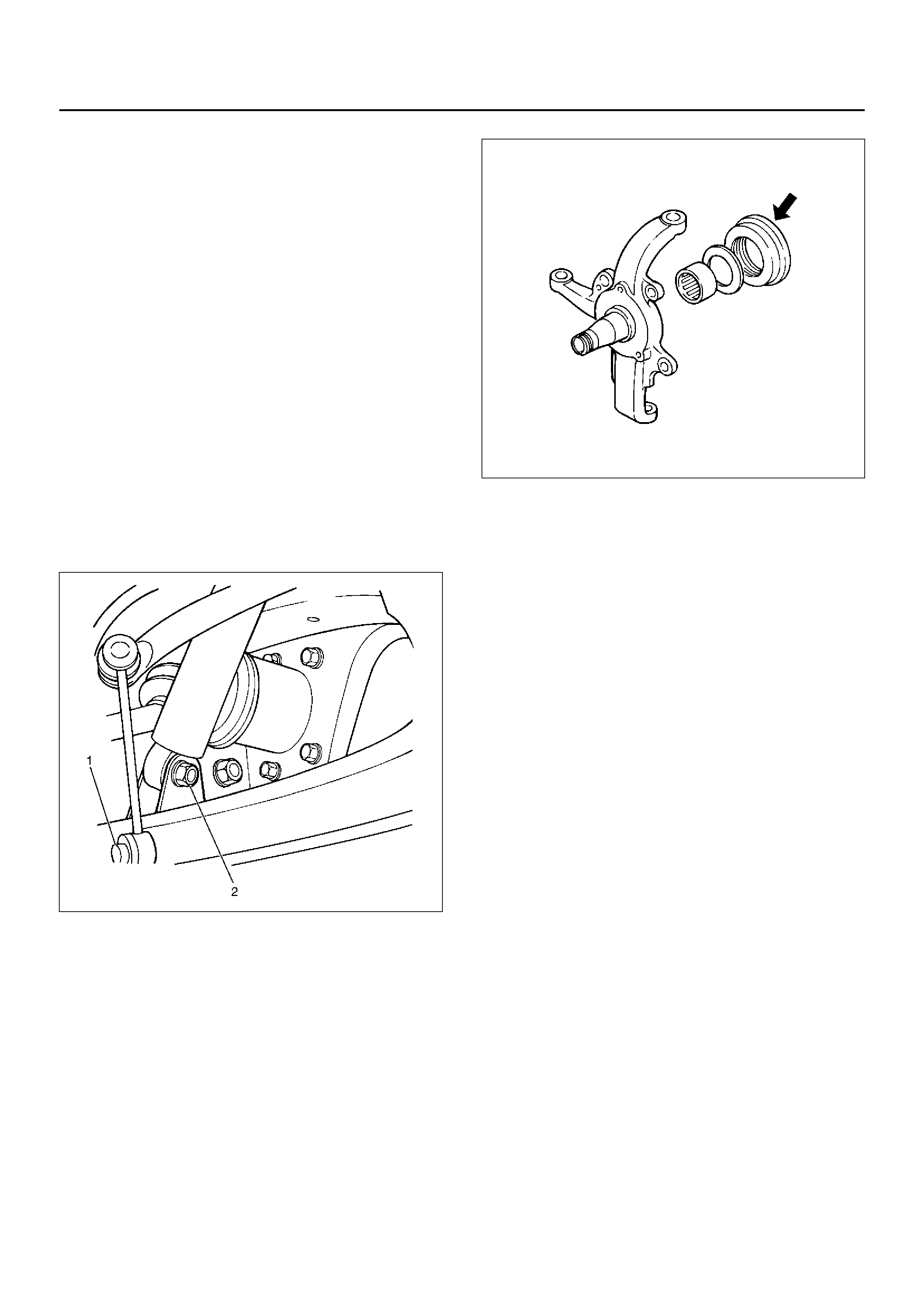
REMOVAL
1. Jack up the vehicle and support it using jack stand.
2. Remove the tire and wheel.
3. Remove the stone guard.
4. Remove the brake caliper fixing bolt and hang the
caliper. Refer to Disc Brakes in Brake section 5C.
5. Remove the antilock brake system speed sensor.
Refer to Front Wheel Speed Sensor in Brake
section 5B.
6. Remove the hub and disc assembly.
Refer to Front Hub and Disc in this section.
7. Remove the propeller shaft, refer to Front Propeller
Shaft in section 4C.
8. Loosen the height control arm of the torsion bar,
then remove the torsion bar from lower control arm.
refer to Torsion Bar in Suspension section 3.
9. Remove the suspension crossmember.
10. Remove the lower nut (1) of the stabilizer link.
11. Remove the lower bolt and nut (2) of the shock
absorber.
412RW057
12. Remove the tie-rod end from the knuckle. Refer to
Power Steering Unit in Steering Section.
13. Disconnect the hose of the shift on the fly, at the
hose clip portion.
14. Disconnect the shift switch connector.
15. Remove the bolts and nuts of the lower control arm
(Frame side), then disconnect the lower control arm
from frame.
16. Disconnect between the right side upper control arm
and the knuckle, then remove the knuckle with lower
control arm.
CAUTION: When removing the knuckle, be careful
not to damage the oil seal inside of the knuckle.
410RW008
17. Support the differential case by the jack.
18. Remove the front axle mounting bolts and nuts,
lower the jack slowly. Remove the left side drive
shaft end from the knuckle, then lower the axle
assembly from the vehicle.
CAUTION:
• Before commencing this procedure, be sure that
the axle assembly is securely supported.
• Be careful not to damage the bellows of the
power steering unit.
INSTALLATION
1. Support the differential case by the jack.
2. Jack up the front drive axle assembly, install the left
side drive shaft to the knuckle, then install the mount
bolts and nuts.
CAUTION:
• Be careful not to damage the bellows of the
power steering unit.
• When installing the drive shaft to the knuckle,
take care to avoid damage to the oil seal inside
of the knuckle.
3. T ighten the mounting bolts and nuts to the specified
torque.
Torque:168N·m