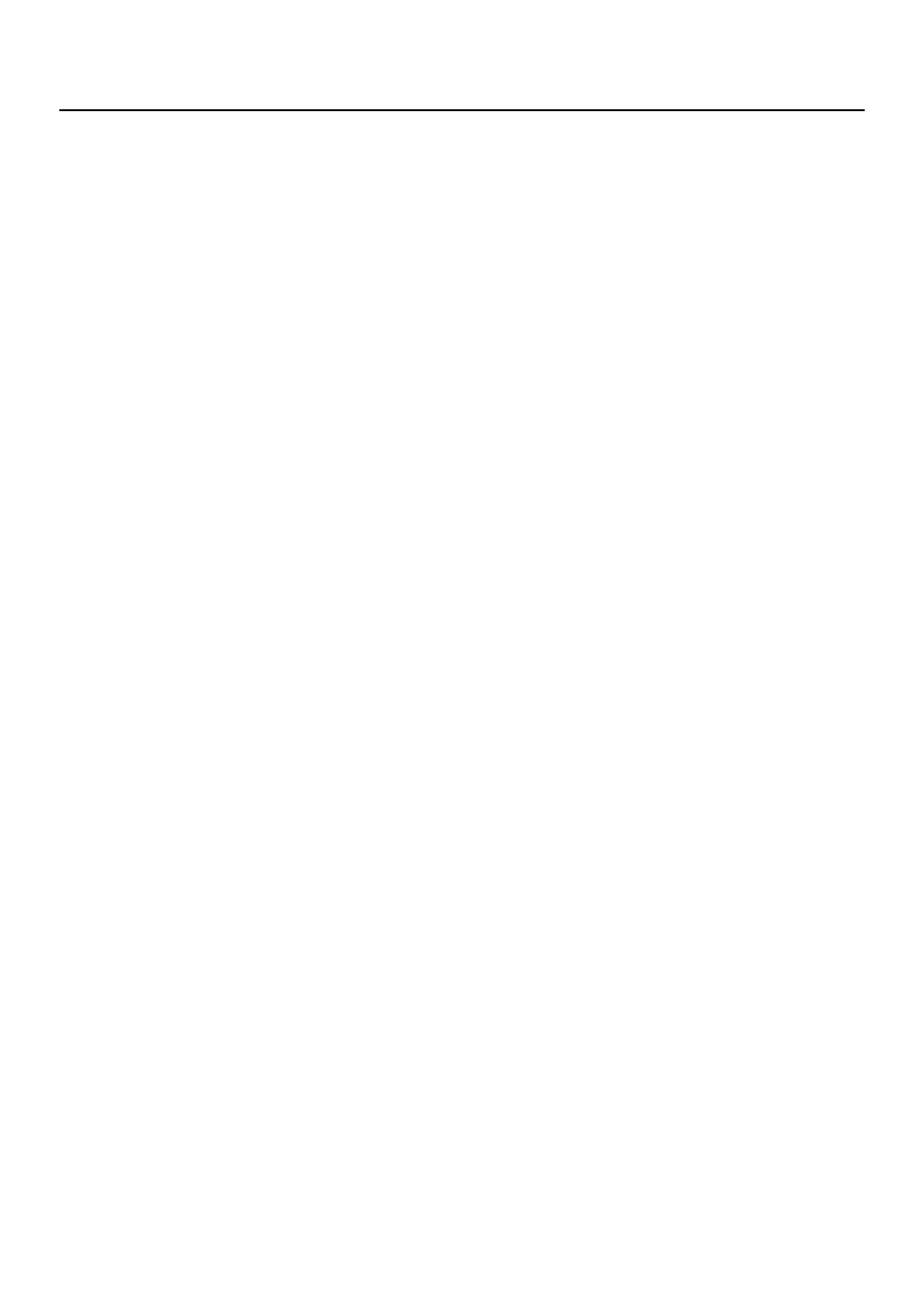
SECTION 5A - BRAKE CONTROL SYSTEM
Service Precaution
General Description
Functional Description
System Components
Electronic Hydraulic Control Unit (EHCU)
ABS Warning Light
Wheel Speed Sensor
G-Sensor
Normal and Anti-lock Braking
Brake Pedal Travel
Acronyms and Abbreviations
General Diagnosis
General Information
ABS Service Precautions
Computer System Service Precautions
General Service Precautions
Note on Intermittents
Test Driving ABS Complaint Vehicles
“ABS" Warning Light
Normal Operation
Tech 2 Scan Tool
Data List
Basic Diagnostic Flow Chart
Basic Inspection Procedure
EHCU Connector Pin-out Checks
Circuit Diagram
Connector List
Part Location
Symptom Diagnosis
Chart A-1 ABS Works Frequently But
Vehicle Does Not Decelerate
Chart TA-1 ABS Works Frequently But
Vehicle Does Not Decelerate
(Use TECH 2)
Chart A-2 Uneven Braking Occurs
While ABS Works
Chart TA-2 Uneven Braking Occurs
While ABS Works (Use TECH 2)
Chart A-3, TA-3 The Wheels Are Locked
Chart A-4 Brake Pedal Feed Is Abnormal
Chart A-5, TA-5 Braking Sound
(From EHCU) Is Heard While Not Braking
Diagnostic Trouble Codes
Diagnosis By “ABS" Warning Light
Illumination Pattern
Diagnostic Trouble Codes (DTCs)
Chart B-1 With the key in the ON position
(Before starting the engine). Warning
light (W/L) is not activated.
Chart B-2 CPU Error (DTC 14 (Flash out) /
C0271, C0272, C0273, C0284 (Serial
communications))
Chart B-3 Low or High Ignition Voltage
(DTC 15 (Flash out) / C0277, 0278 (Serial
communications))
Chart B-4 Excessive Dump Time
(DTC 17 (Flash out) / C0269 (Serial
communications))
Chart B-5 Excessive Isolation Time
(DTC 18 (Flash out) / C0274 (Serial
communications))
Chart B-6 G-Sensor Output Failure
(DTC 21 (Flash out) / C0276 (Serial
communications))
Chart B-7 Brake Switch Failure
(DTC 22 (Flash out) / C0281 (Serial
communications))
Chart B-8 2WD Controller in 4WD Vehicle
Controller (DTC 13 (Flash out) / C0285
(Serial communications)), 4WD State
Input Signal Failure (DTC 24 (Flash out) /
C0282 (Serial communications))
Chart B-9 Pump Motor Failure (DTC 32
(Flash out) / C0267, C0268 (Serial
communications))
Chart B-10 EHCU Valve Relay Failure
(DTC 35 (Flash out) / C0265, C0266 (Serial
communications))
Chart B-11 FL Isolation Solenoid Coil
Failure (DTC 41 (Flash out) / C0245,
C0247 (Serial communications))
Chart B-12 FL Dump Solenoid Coil
Failure (DTC 42 (Flash out) / C0246,
C0248 (Serial communications))
Chart B-13 FR Isolation Solenoid Coil
Failure (DTC 43 (Flash out) /
C0241, C0243 (Serial communications))
Chart B-14 FR Dump Solenoid Coil
Failure (DTC 44(Flash out) /
C0242, C0244 (Serial communications))
Chart B-15 Rear Isolation Solenoid
Coil Failure (DTC 45 (Flash out) / C0251,
C0253 (Serial communications))