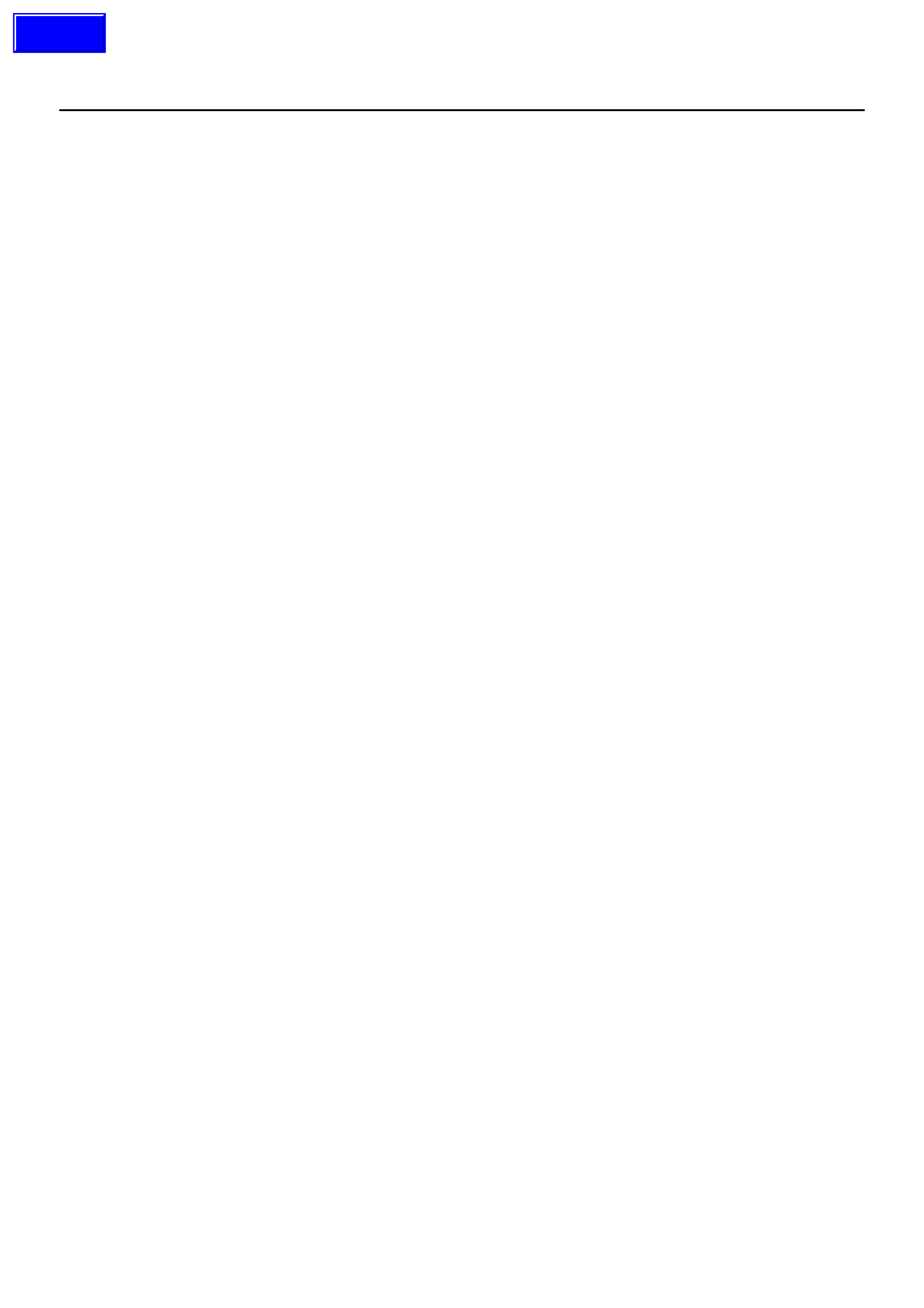
SECTION 6F - ENGINE LUBRICATION
Service Precaution
General Description
Oil Pump
Oil Pump and Associated Parts
Oil Pump and Associated Parts
Inspection and Repair
Reassembly
Oil Pan and Crankcase
Removal
Installation
Oil Pump
Removal
Installation
Oil Pump Oil Seal
Removal
Installation
Oil Filter
Removal
Installation
Main Data and Specification
Special Tool
SERVICE PRECAUTION
WARNING: THIS VEHICLE HAS A SUPPLEMENTAL
RESTRAINT SYSTEM (SRS), REFER TO THE SRS
COMPONENT AND WIRING LOCATION VIEW IN
ORDER TO DETERMINE WHETHER YOU ARE
PERFORMING SERVICE ON OR NEAR THE SRS
COMPONENTS OR THE SRS WIRING. WHEN YOU
ARE PERFORMING SERVICE ON OR NEAR THE
SRS COMPONENTS OR THE SRS WIRING, REFER
TO THE SRS SERVICE INFORMATION. FAILURE TO
FOLLOW WARNINGS COULD RESULT IN
POSSIBLE AIR BAG DEPLOYMENT, PERSONAL
INJURY, OR OTHERWISE UNNEEDED SRS SYSTEM
REPAIRS.
CAUTION: Always use the correct fastener in the
proper location. When you replace a fastener, use
ONLY the exact part number for that application.
HOLDEN will call out those fasteners that require a
replacement after removal. HOLDEN will also call
out the fasteners that require thread lockers or
thread sealant. UNLESS OTHERWISE SPECIFIED,
do not use supplement a l coatings (Paints, greases,
or other corrosion inhibitors) on threaded
fasteners or fastener joint interfaces. Generally,
such c oatin gs ad versely affect the f astene r tor que
and the joint clamping force, and may damage the
fastener. When you install fasteners, use the
correct tightening sequence and specifications.
Following these instructions can help you avoid
damage to parts and systems.