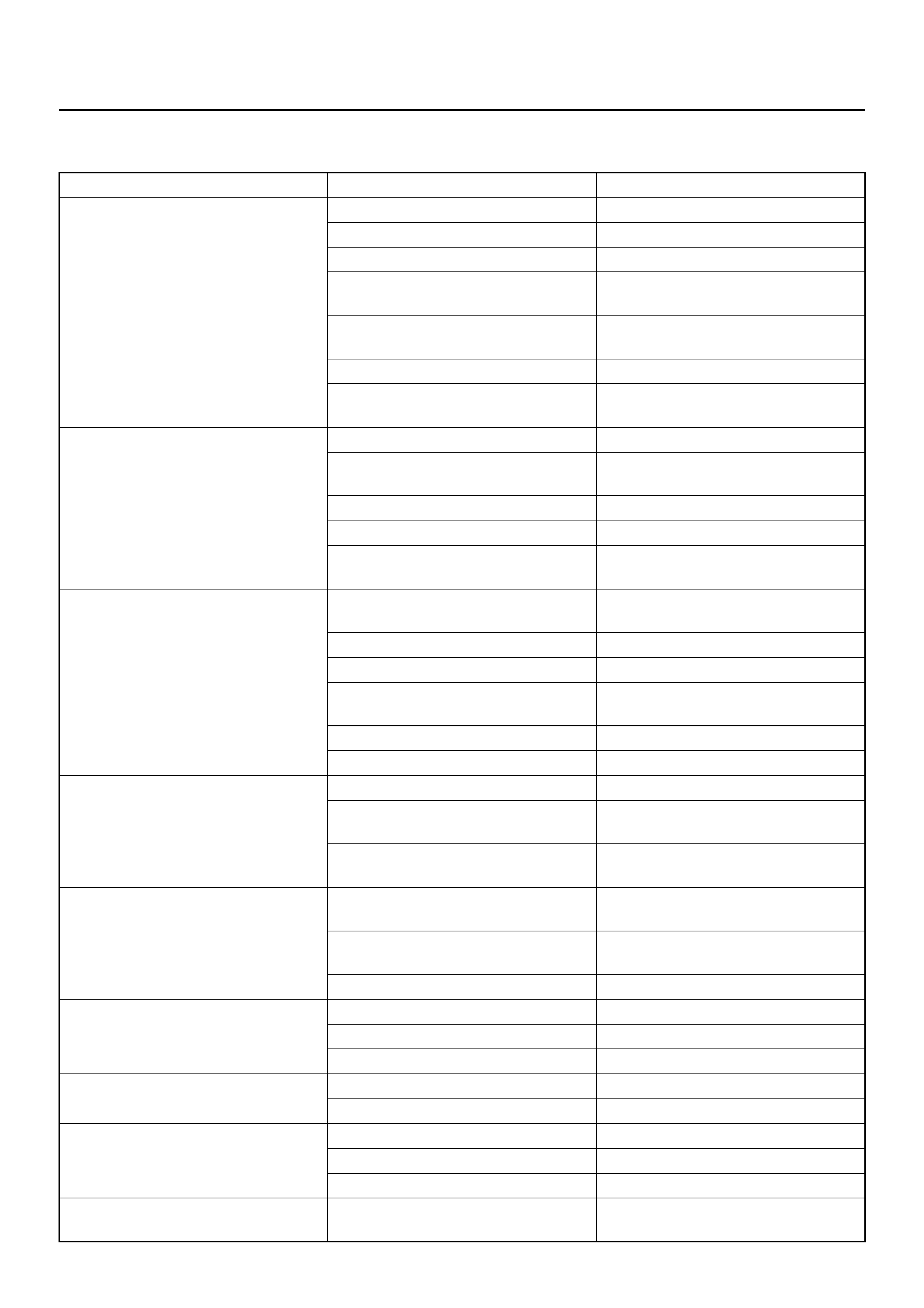
DIAGNOSIS
Condition Possible cause Correcti on
Dragging Air in circuit. Bleed and check for damage.
Driven plate worn or warped. Replace.
Clutch fork off the ball stud. Install correctly and lubricate.
Diaphragm spring weak or tip of
fingers worn. Replace.
Driven plate sticking on splines. Clean and free splines and lubricate
with grease.
Pilot bearing worn or damaged. Replace.
Master cylinder and slave cylinder
seals worn. Replace.
Slipping Clutch facing worn. Replac e.
Driven plate friction pads worn or
oilsoaked. Replace and check for leaks as
needed.
Diaphragm spring weak. Replace pressure plate.
Pressure plate or flywheel warped. Replace.
Master cylinder and slave cylinder
seals worn. Replace as needed.
Chattering Clutch facing in poor contact or
facing warped. Replace.
Surface of faci ng har den ed. Replac e.
Driven plate friction pads oil soaked. Replace and check for leaks.
Damper springs weakened or
broken. Replace.
Rivets on clutch plate loosened. Replace.
Pressure plate or flywheel warped. Replace as needed.
Rattling Diaphragm spring weak. Replace the pressure plate.
Clutch fork loose or off the ball stud. Replace the retaining spring or
install the fork correctly.
Driven plate springs weak or oil in
the damper. Replace and check for leaks as
needed.
Release bearing noisy with the
clutch engaged Release bearing binding. Clean, or replace if damaged, and
lubricate.
Clutch fork off the ball stud or loose
spring tension. Install correctly, and lubricate.
Linkage return springs weak. Replace.
Noisy Release bearing worn or damaged. Replace.
Clutch fork off the ball stud. Install correctly and lubricate.
Pilot bearing loose. Replace.
Pedal stays on the floor when
disengaged Replace bearing binding. Free up, or replace, and lubricate.
Diaphragm spring weak. Replace the pressure plate.
Pedal is hard to push down Hydraulic line blocked or crimped. Clean out or replace.
Master or slave cylinders bindinig. Repair or replace as needed.
Driven plate worn. Replace.
Squeaking Ball stud not lubricated or incorrectly
lubricated. Lubricate with high temperature
grease.