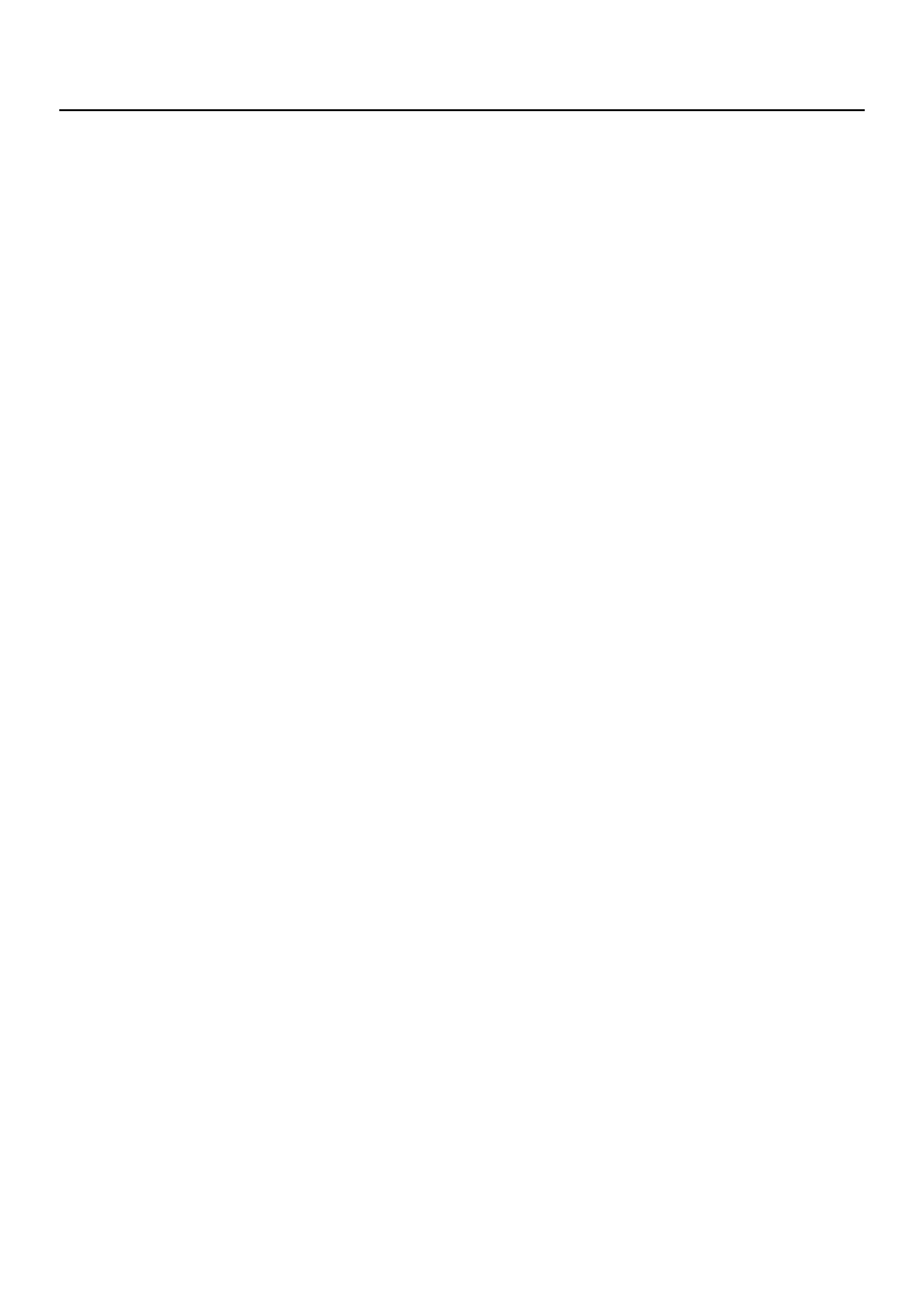
SECTION 7B2 - TRANSFER CASE
Service Precaution
General Description
Transfer Rear Oil Seal
Transfer Rear Oil Seal and Associated
Parts
Removal
Installation
Transfer Case Assembly (A/T)
Transfer Case Assembly (A/T) and
Associated Parts
Removal
Installation
Transfer Rear Case Assembly (A/T)
Transfer Rear Case Assembly (A/T) and
Associated Parts
Removal
Installation
Transfer Rear Cover Assembly
Disassembly
Inspection and Repair
Reassembly
Detent, Shift Arm, and Interlock Pin
(Transfer Case Assembly)
Disassembled View
Disassembly
Inspection and Repair
Reassembly
Transfer Case Assembly
Disassembled View
Disassembly
Inspection and Repair
Reassembly
Main Data and Specifications
Special Tools
SERVICE PRECAUTION
WARNING: THIS VEHICLE HAS A SUPPLEMENTAL
RESTRAINT SYSTEM (SRS). REFER TO THE SRS
COMPONENT AND WIRING LOCATION VIEW IN
ORDER TO DETERMINE WHETHER YOU ARE
PERFORMING SERVICE ON OR NEAR THE SRS
COMPONENTS OR THE SRS WIRING. WHEN YOU
ARE PERFORMING SERVICE ON OR NEAR THE
SRS COMPONENTS OR THE SRS WIRING, REFER
TO THE SRS SERVICE INFORMATION. FAILURE
TO FOLLOW WARNINGS COULD RESULT IN
POSSIBLE AIR BAG DEPLOYMENT, PERSONAL
INJURY, OR OTHERWISE UNNEEDED SRS
SYSTEM REPAIRS.
CAUTION: Always use the correct fastener in the
proper location. When you replace a fastener, use
ONLY the exact part number for that application.
HOLDEN will call out those fasteners that require a
replacement after removal. HOLDEN will also call
out the fasteners that require thread lockers or
thread sealant. UNLESS OTHERWISE SPECIFIED,
do not use supplemental coatings (Paints, greases,
or other corrosion inhibitors) on threaded fasteners
or fastener joint interfaces. Generally, such
coatings adversely affect the fastener torque and
the joint clamping force, and may damage the
fastener. When you install fasteners, use the correct
tightening sequence and specifications. Following
these instructions can help you avoid damage to
parts and systems.