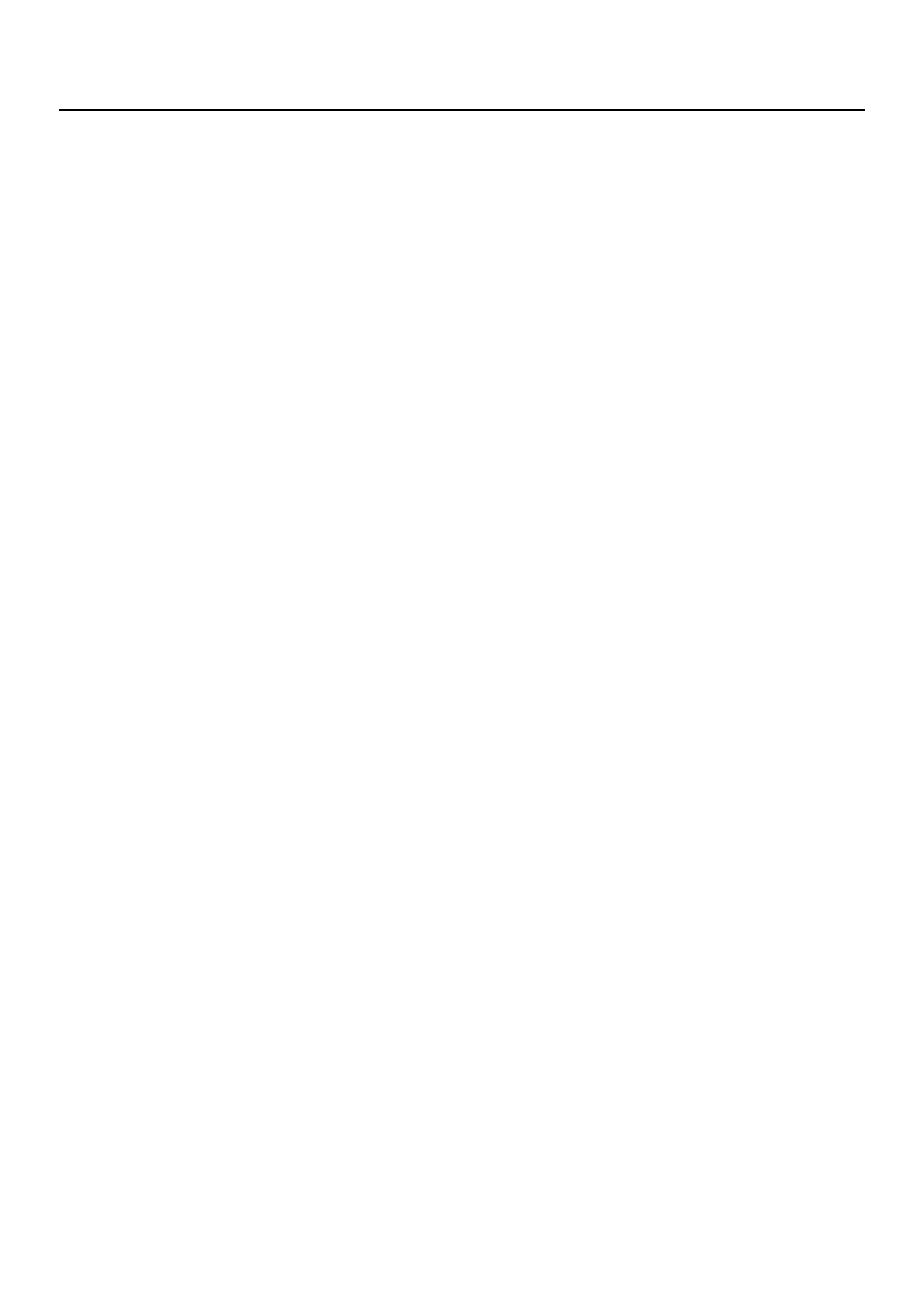
SECTION 7B3 - TRANSFER CASE (TOD)
Service Precaution
General Description
Removal and Installation of Transfer Case
Assembly
Removal
Installation
Transfer Rear Oil Seal
Removal
Installation
TOD Control Unit
Removal
Installation
Unit Repair
Disassembly and Reassembly of Major
Components
Disassembly
Reassembly
Transfer Cover Assembly
Disassembly
Inspection and Repair
Reassembly
Clutch Pack and Clutch Cam (Transfer
Case Assembly)
Disassembly
Reassembly
Chain, Sprocket and Mechanical Lock
(Transfer Case Assembly)
Disassembly
Reassembly
Transfer Case Assembly
Disassembly
Reassembly
Inspection and Repair (Transfer Case
Assembly)
Main Data and Specification
General Specification
Torque Specifications
Special Tools
SERVICE PRECAUTION
WARNING: THIS VEHICLE HAS A SUPPLEMENTAL
RESTRAINT SYSTEM (SRS). REFER TO THE SRS
COMPONENT AND WIRING LOCATION VIEW IN
ORDER TO DETERMINE WHETHER YOU ARE
PERFORMING SERVICE ON OR NEAR THE SRS
COMPONENTS OR THE SRS WIRING. WHEN YOU
ARE PERFORMING SERVICE ON OR NEAR THE
SRS COMPONENTS OR THE SRS WIRING, REFER
TO THE SRS SERVICE INFORMATION. FAILURE TO
FOLLOW WARNINGS COULD RESULT IN POSSIBLE
AIR BAG DEPLOYMENT, PERSONAL INJURY, OR
OTHERWISE UNNEEDED SRS SYSTEM REPAIRS.
CAUTION: Always use the correct fastener in the
proper location. When you replace a fastener, use
ONLY the exact part number for that application.
HOLDEN will call out those fasteners that require a
replacement after removal. HOLDEN will also call
out the fasteners that require thread lockers or
thread sealant. UNLESS OTHERWISE SPECIFIED,
do not use supplemental coatings (Paints, greases,
or other corrosion inhibitors) on threaded fasteners
or fastener joint interfaces. Generally, such
coatings adversely affect the fastener torque and
the joint clamping force, and may damage the
fastener. When you install fasteners, use the correct
tightening sequence and specifications. Following
these instructions can help you avoid damage to
parts and systems.