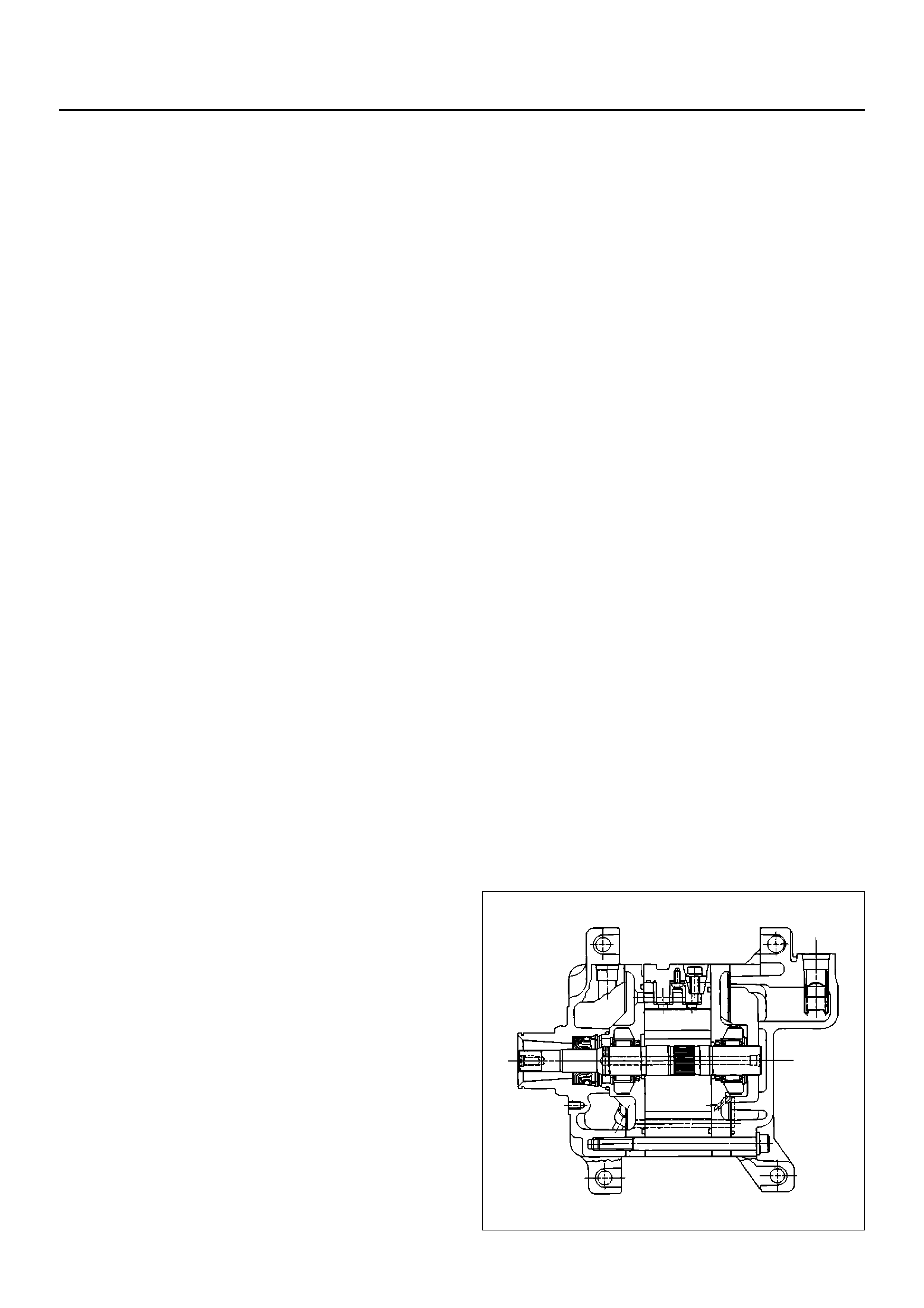
Compressor
Service Precaution
WARNING: This vehicle has a Supplemental
Restraint System (SRS). Refer to the SRSComponent Location View in order to determinewhether you are performing service on or near theSRS components or the SRS wiring. When you areperforming service on or near the SRS componentsor the SRS wiring, refer to the SRS On-Vehicle
Service Information. Failure to follow CAUTIONScould result in possible air bag deployment,personal injury, or otherwise unneeded SRS systemrepairs.
CAUTION: Always use the correct fastener in the
proper location. When you replace a fastener, use
ONLY the exact part number for that application.
ISUZU will call out those fasteners that require a
replacement after removal. ISUZU will also call out
the fasteners that require thread lockers or thread
sealant. UNLESS OTHERWISE SPECIFIED, do not
use supplemental coatings (paints, greases, or
other corrosion inhibitors) on threaded fas teners or
fastener joint interfaces. Generally, such coatings
adversely affect the fastener torque and the joint
c lamping for ce, and may damage the fastener . When
you install fasteners, use the correct tightening
sequence and specifications. Following these
instructions can help you avoid damage to parts
and systems.
General Description
When servicing the compressor, keep dirt or foreign
material from getting on or into the compressor parts
and system. Clean tools and a clean work area are
important for proper service. The compressor
connections and the outside of the compressor should
be cleaned before any "On-Vehicle" repair, or before
removal of the compressor. The parts must be kept
clean at all times and any parts to be reassembled
should be cleaned with Trichloroethane, naphtha,
kerosene, or equivalent solvent, and dried with dry air.
Use only lint free cloths to wipe parts.
The operations described below are based on bench
overhaul with compressor removed from the vehicle,
except as noted. They have been prepared in order of
access ibility of the comp onents. When th e compre ssor
is removed from the vehicle for servicing, the oil
remaining in the compressor should be discarded and
new compressor oil added to the compressor.
Compressor malfunction will appear in one of four ways:
noise, seizure, leakage or low discharge pressure.
Resonant compressor noises are not cause for alarm;
however, irregular noise or rattles may indicate broken
parts or excessive clearances due to wear. To check
seizure, de-energize the magnetic clutch and check to
see if the drive plate can be rotated. If rotation is
impossible, the compressor is seized. Low discharge
pressure may be due to a faulty internal seal of the
compressor, or a restriction in the compressor. Low
discharge pressure may also be due to an insufficient
refrigerant charge or a restriction elsewhere in the
system. These possibilities should be checked prior to
servicing the compressor. If the compressor is
inoperative, but is not seized, check to see if current is
being supplied to the magnetic clutch coil terminals.
The compressor oil used in the HFC-134a system
compressor differs from that used in R-12 systems.
Also, compressor oil to be used varies acco rding to the
compressor model. Be sure to av oid mixing two or more
different types of oil.
If the wrong oil is used, lubrication will be p oor and the
compressor will seize or malfunction.
DKV -1 4G Type Co m pressor
DKV-14G is equipped with five-vane rotary compressor.
These vanes are built into a rotor which is mounted on a
shaft.
When the shaft rotates, the vanes bui lt into the cylinder
block assembly are operated by centrifugal force.
This changes the volume of the spare formed by the
rotor and cylinder, resulting in the intake and
compression of the refrigerant gas. The discharge v alve
and the valve stopper, which protects the discharge
valve, are built into the cylinder block assembly. There
is no suction valve but a shaft seal is insta lled between
the shaft and head; a trigger valve, which applies back
pressure to the vanes, is installed in the cylinder block
and a refrig erant gas temperature sensor is installed in
the front head.
The spec ified quantity of compress or oil is con tained in
the compressor to lubricate the various par ts using the
refrigerant gas discharge pressure.
A01RS003