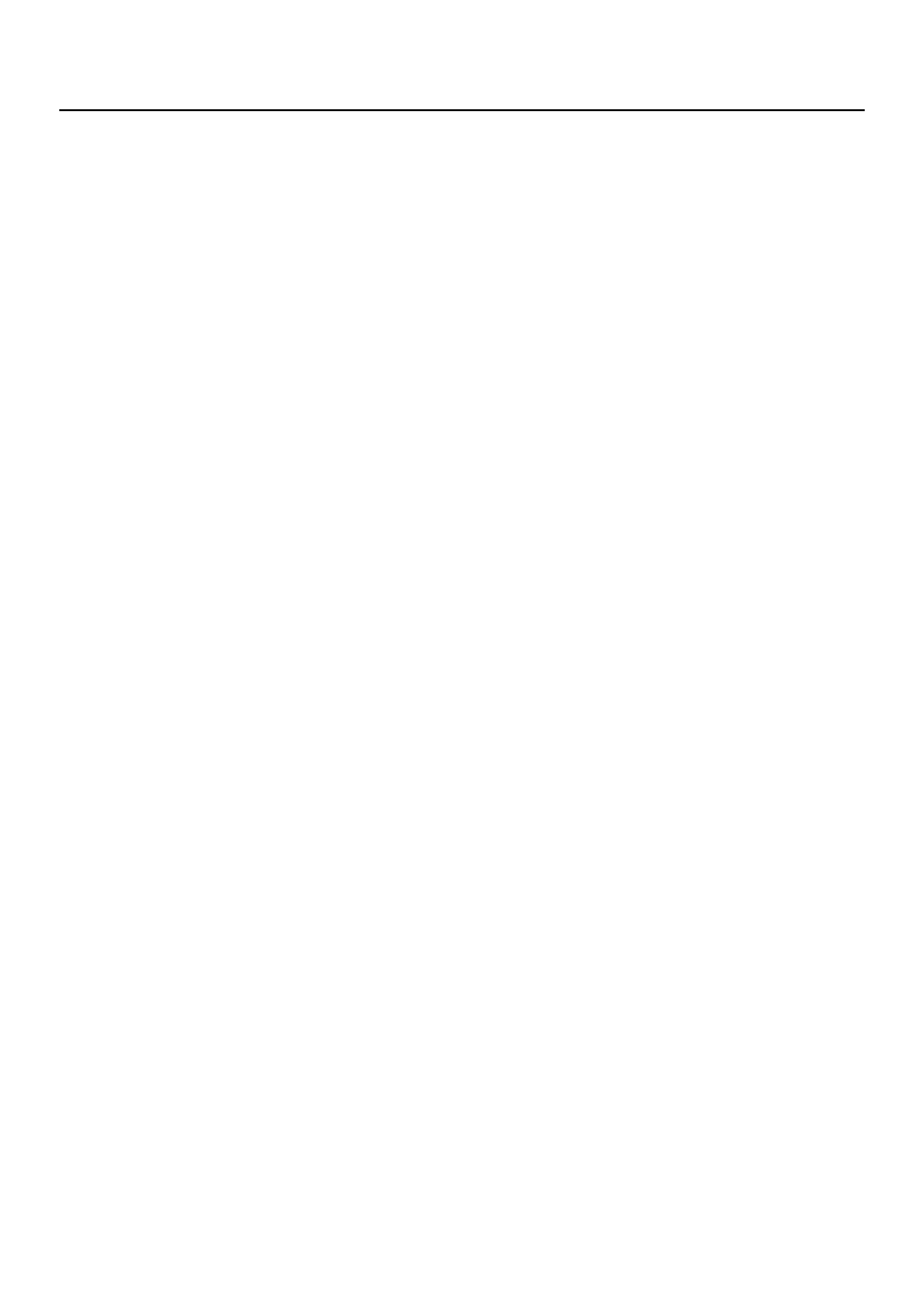
4.Bleed the system. Refer to Bleeding the Power
Steering System in this section.
5.Start the engine and check the fluid level. Add
power steering fluid if required. When the engine is
at normal operating temperature, increase engine
speed to 1500 rpm.
CAUTION: Do not leave shutoff valve fully closed
for more than 5 seconds, as the pump could
become damaged internally.
6.Fully close the shutoff valve. Record the highest
pressures.
•If the pressure recorded is within 9300–9800 kPa
(95–100 kg/cm2/1350–1420 psi), the pump is
functioning within its specifications.
•If the pressure recorded is higher than 9800 kPa
(100 kg/cm2/1420 psi), the valve in the pump is
defective.
•If the pressure recorded is lower than 9300 kPa
(95 kg/cm2/1350 psi), the valve or the rotating
group in the pump is defective.
7.If the pump pressures are within specifications,
leave the valve open and turn (or have someone
else turn) the steering wheel fully in both directions.
Record the highest pressures and compare with the
maximum pump pressure recorded in step 6. If this
pressure cannot be built in either side of the power
steering unit, the power steering unit is leaking
internally and must be replaced.
8.Shut the engine off, remove the testing gauge.
9.Reconnect the pressure hose, check the fluid level
and make the needed repairs.
10.If the problem still exists, the steering and front
suspension must be thoroughly examined.
Maintenance
The hydraulic system should be kept clean and fluid
level in the reservoir should be checked at regular
intervals and fluid added when required. Refer to
Recommended Fluids and Lubricants in General
Information section for the type of fluid to be used and
the intervals for filling.
If the system contains some dirt, flush it as described in
this section. If it is exceptionally dirty, the pump must
be completely disassembled before further usage. (The
steering unit cannot be disassembled.)
All tubes, hoses, and fittings should be inspected for
leakage at regular intervals. Fittings must be tight.
Make sure the clips, clamps and supporting tubes and
hoses are in place and properly secured.
Power steering hoses and lines must not be twisted,
kinked or tightly bent. Air in the system will cause
spongy action and noisy operation. When a hose is
disconnected or when fluid is lost, for any reason, the
system must be bled after refilling. Refer to Bleeding
the Power Steering System in this section.
•Inspect belt for tightness.
•Inspect pulley for looseness or damage. The pulley
should not wobble with the engine running.
•Inspect hoses so they are not touching any other
parts of the vehicle.
•Inspect fluid level and fill to the proper level.
Fluid Level
1.Run the engine until the power steering fluid
reaches normal operating temperature, about 55°C
(130°F), then shut the engine off.
2.Check the level of fluid in the reservoir.
3.If the fluid level is low, add power steering fluid as
specified in General Information to the proper level
and install the receiver cap.
4.When checking the fluid level after the steering
system has been serviced, air must be bled from the
system. Refer to Bleeding the Power Steering
System in this section.
Bleeding The Power Steering System
When a power steering pump or unit has been installed,
or an oil line has been disconnected, the air that has
entered the system must be bled out before the vehicle
is operated. If air is allowed to remain in the power
steering fluid system, noisy and unsatisfactory
operation of the system may result.
Bleeding Procedure
When bleeding the system, and any time fluid is added
to the power steering system, be sure to use only
power steering fluid as specified in General Information.
1. Fill the pump fluid reservoir to the proper level and
let the fluid settle for at least two minutes.
2. Start the engine and let it run for a f e w seconds. Do
not turn the steering wheel. Then turn the engine
off.
3. Add fluid if necessary.
4. Repeat the above procedure until the fluid level
remain s constant after running the engine.
5. Raise and support the front end of the vehicle so
that the wheels are off the ground.
6. Start the engine. Slowly turn the steering wheel
right and left, lightly contacting the wheel stops.
7. Add power steering fluid if necessary.
8. Lower the vehicle, set the steering wh eel at the
straight forward position after turning it to its full
steer positions 2 or 3 times, and stop the engine.
9. Check the fluid level and refill as required.
10. If the fluid is extremely foamy, allow the vehicle to
set a f e w minutes, then repeat the abov e procedure.