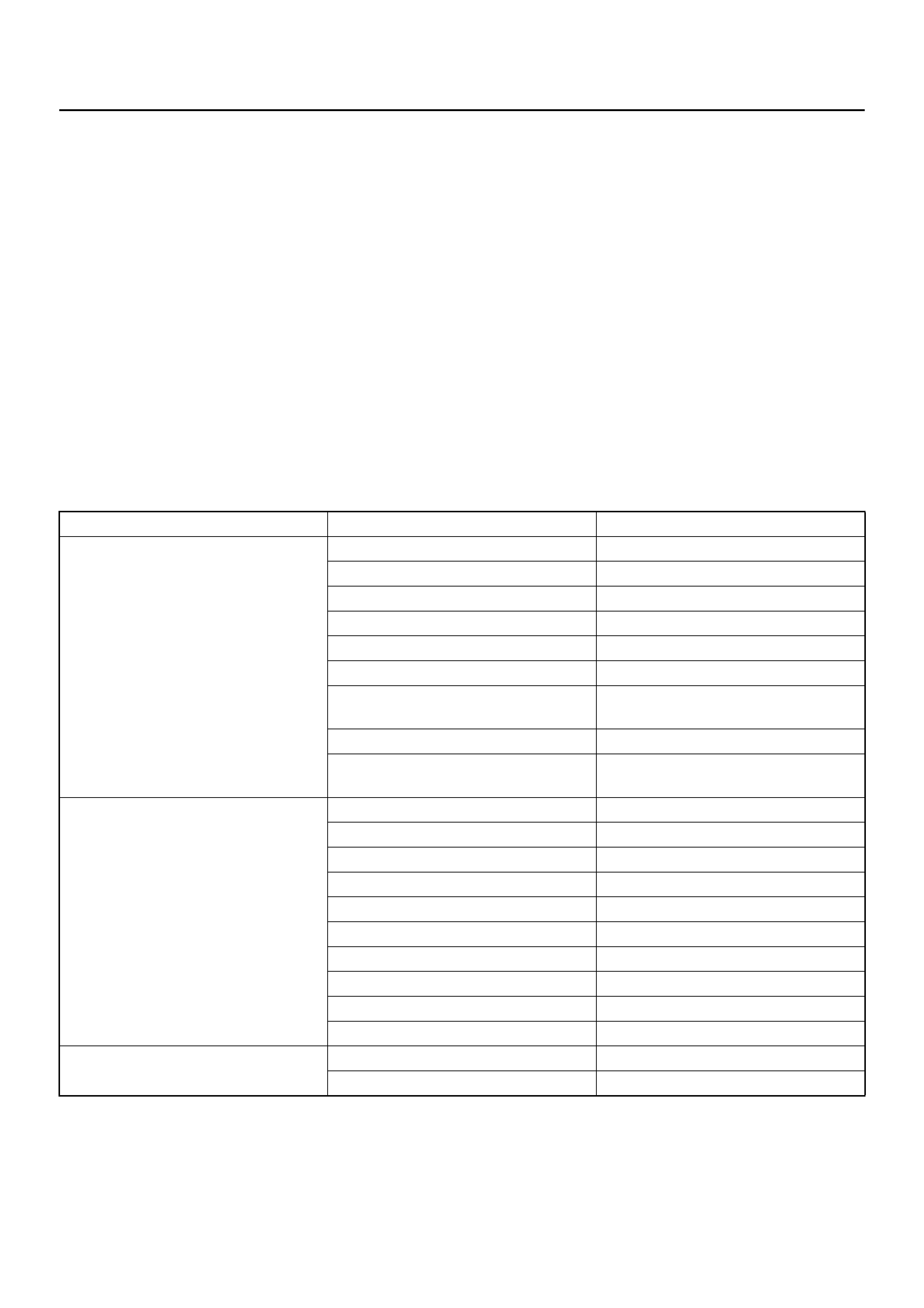
General Description
The front suspension is designed to allow each wheel to
compensate for changes in the road surface level
without greatly affecting the opposite wheel. Each
wheel is independently connected to the frame by a
steering knuckle, ball joint assemblies, and upper and
lower control ar ms. The front whee ls are hel d in pro per
relationship to each other by two tie-rods which are
connected to steering arms on the knuckles, and to a
steering unit.
All models have a front suspension system consisting of
control arms, stabilizer bar, shock absorber and a
torsion bar. The front end of the torsion bar is attached
to the lower control arm. The rear of the torsion bar is
mounted into a height control arm at the crossmember.
Vehicle trim height is controlled by adjusting this arm.
Shock absorbe rs ar e moun ted be tween t he brackets on
the frame and the lower co ntr ol arms. The lower portion
of each shock absorber is attached to the lower control
arm. The up per portio n of each sh ock absorbe r extends
throug h a frame bracket and is secured wi th two rubber
bushings, two retainers and a nut.
Ball joint assemblies are bolted to the outer end of the
upper and lower control arm and are attached to the
steering knuckle.
The inner ends of the upper control arm hav e pressed in
bushings. Bolts, passing through the bushing, attach the
control arm to the frame. The inner ends of the lower
control arm are attached to the frame by bolts passing
through the bushings.
Side roll of the front suspension is controlled by a spring
steel stabilizer bar. It is mounted in rubber bushings,
which are held to the frame by brackets. The ends of
the stabilizer bar are connected to the lower control
arms by links.
Diagnosis
Condition Possible cause Correction
Vehicle Pulls Mismatched or uneven tires. Replace tire.
Tires not adequately inflated. Adjust tire pressure.
Broken or sagging springs. Replace spring.
Radial tire lateral force. Replace tire.
Improper wheel alignment. Adjust wheel alignment.
Brake dragging in one wheel. Repair brake.
Loose, bent or broken front or rear
suspension parts. Tighten or replace the appropriate
suspension part(s).
Faulty shock absorbers. Replace shock absorber.
Parts in power steering valve
defective. Replace power steering unit.
Abnormal or Excessive Tire Wear Sagging or broken spring. Replace spring.
Tire out of balance. Balance or replace tire.
Improper wheel alignment. Check front end alignment.
Faulty shock absorber. Replace shock absorber.
Hard driving. Replace tire.
Overloaded vehicle. Replace tire and reduce load.
Tires not rotated periodically. Replace or rotate tire.
W orn or loose road wheel bearings. Replace wheel bearing.
Wobbly wheel or tires. Replace wheel or tire.
Tires not adequately inflated. Adjust the pressure.
Wheel Hop Blister or bump on tire. Replace tire.
Improper shock absorber operation. Replace shock absorber.