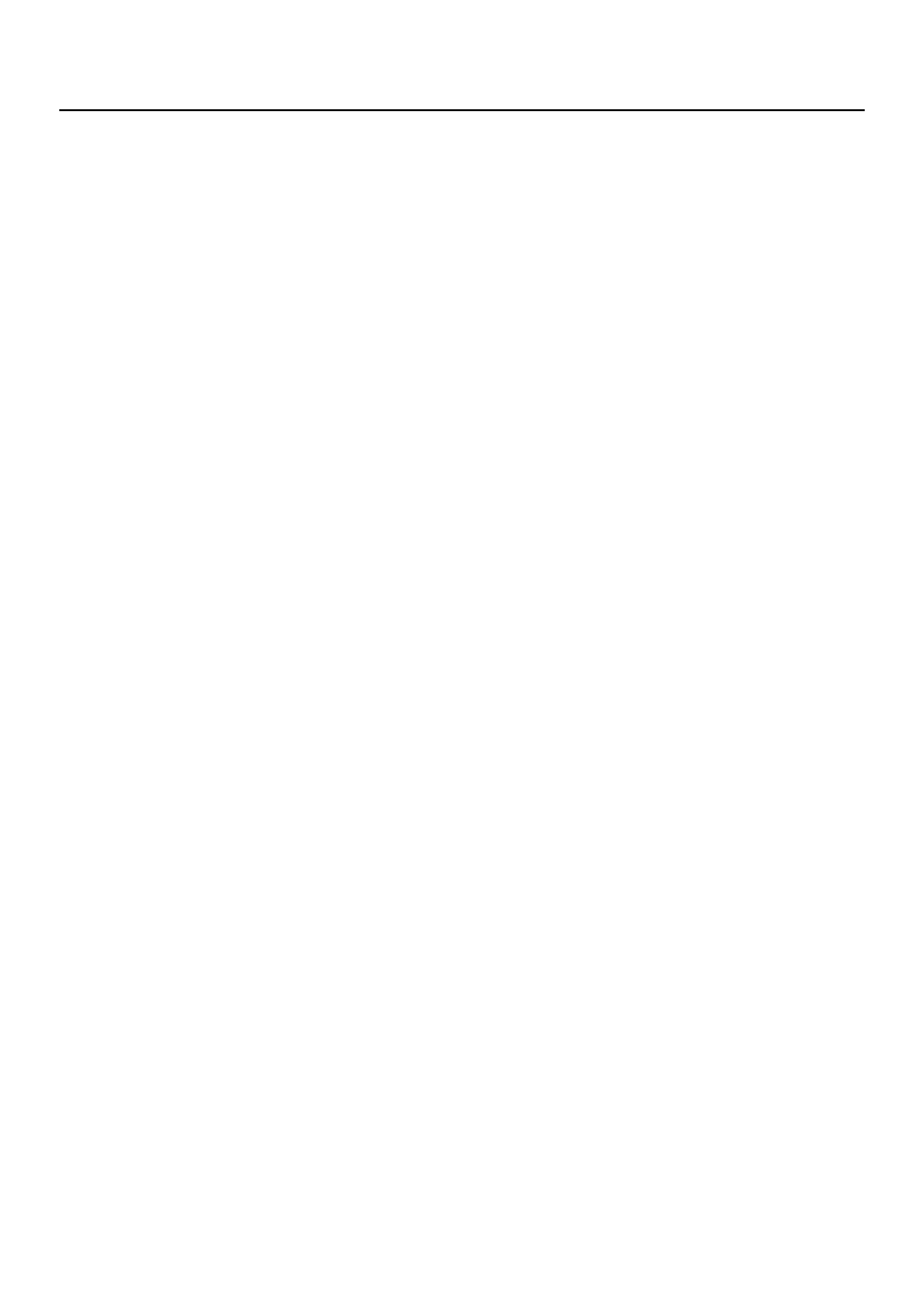
When working on the fuel system, there are several
things to k eep in mind:
• Any time the fuel system is being worked on,
disconnect the negative battery cable except for
those tests where battery voltage is required.
• Always keep a dry chemical (Class B) fire
extinguisher near the work area.
• Replace all pipes with the same pipe and fittings that
were removed.
• Clean and inspect “O" rings. Replace if required.
• Always relieve the line pressure before servicing any
fuel sys tem com pon ent s.
• Do not attempt repairs on the fuel system until you
have read the instructions and checked the pictures
relating to that repair.
• Adhere to all Notices and Cautions.
All gasoline engines are designed to use only unleaded
gasoline. Unleaded gasoline must be used for proper
emission control system operation.
Its use will also minimize spark plug fouling and extend
engine oil life. Using leaded gasoline can damage the
emissi on con t ro l system and cou ld resu lt in los s of
emission warranty coverage.
All cars are equipped with an Evaporative Emission
Control System. The purpose of the system is to
minimize the escape of fuel v apors to the atmosphere.
Fuel Metering
The Powertrain Control Module (PCM) is in complete
control of this fuel delivery system during normal driving
conditions.
The intake manifold function, like that of a diesel, is
used only to let air into the engine. The fuel is injected
by separate injectors that are mounted over the intake
manifold.
The Manifold Absolute Pressure (MAP) sensor
measures the changes in the intake manifold pressure
which result from engine load and speed changes,
which the MAP sensor converts to a voltage output.
This sensor generates the voltage to change
corresponding to the flow of the air drawn into the
engine.
The changing voltage is transformed into an electric
signal and provided to the PCM.
With receipt of the signals sent from the MAP sensor,
Intake Air Temperature sensor and others, the PCM
determines an appropriate fuel injection pulse width
feeding such information to the fuel injector valves to
effe ct an appropriate air/fuel ratio.
The Multiport Fuel Injection system utilizes an injection
system where the injectors turn on at every crankshaft
revolution. The PCM controls the injector on time so
that the correct amount of fuel is metered depending on
driving conditions.
Two interchangeable “O" rings are used on the injector
that must be replaced when the injectors are remov ed.
The fuel rail is attached to the top of the intake manifold
and supplies fuel to all the injectors.
Fuel is recirculated through the rail continually while the
engine is running. This removes air and v apors from the
fuel as well as keeping the fuel cool during hot weather
operation.
The fuel pressure control valve that is mounted on the
fuel rail maintains a pressure differential across the
injectors under all operating conditions. It is
accomplished by controlling the amount of fuel that is
recirculated back to the fuel tank based on engine
demand.
See Section “Driveability and Emission" for more
information and diagnosis.