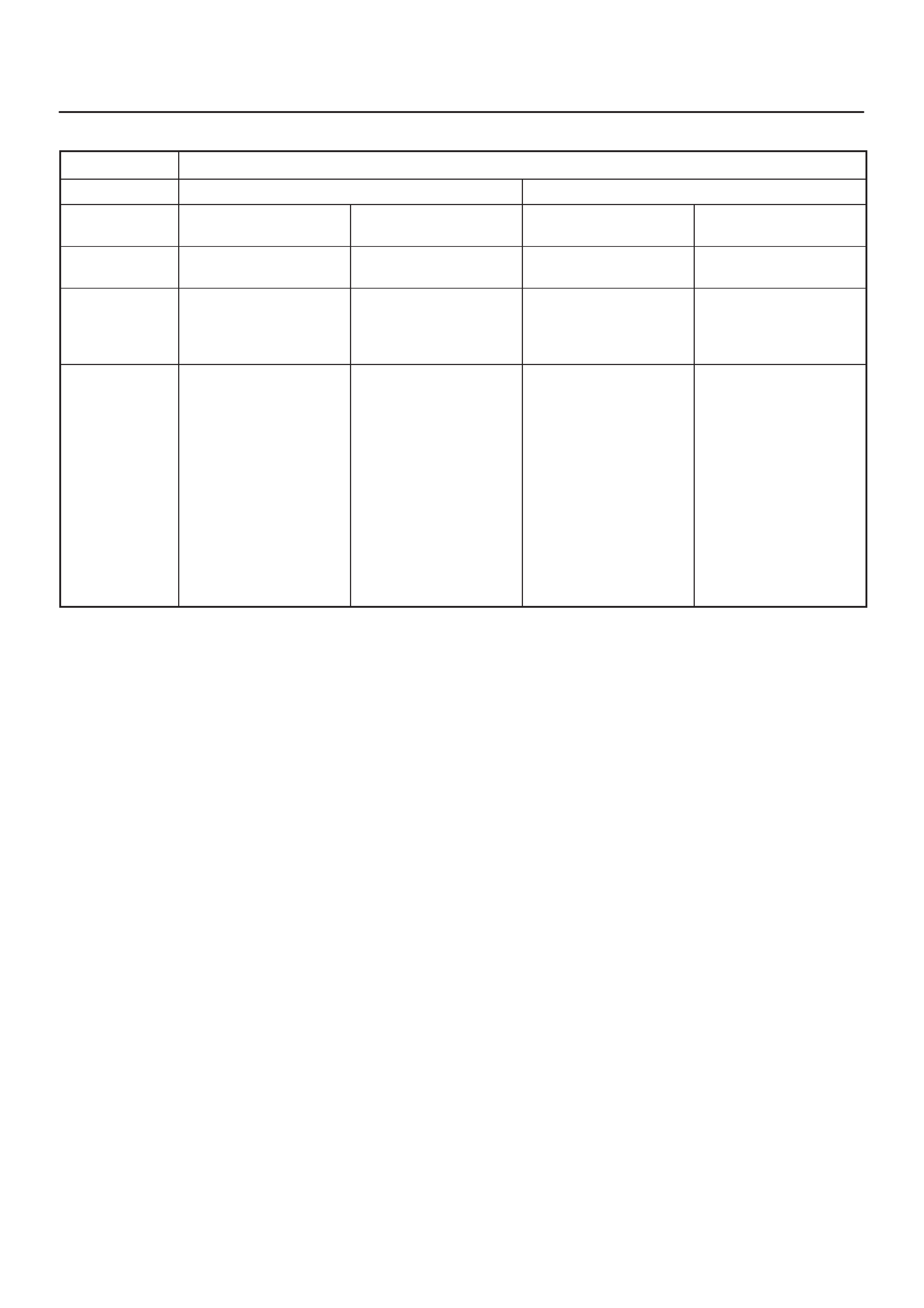
Fluid Condition
FLUID CONDITION
NORMAL* CONTAMINATED
COLOR RED OR LIGHT
BROWN BROWN NON–TRANSPARENT
/ PINK BROWN
DRAIN
REQUIRED? NO YES YES YES
CONTAMI-
NATION NONE Very small amount of
foreign material in
bottom of pan
Contamination by
coolant or other source Large pieces of metal
or other foreign
material in bottom of
pan
CORRECT
LEVEL AND
CONDITION
1.LOW LEVEL:
A.Add fluid to
obtain proper
level & check for
external leaks.
B.Correct cause of
leak.
2.HIGH LEVEL:
–Remove excess
fluid
–Remove both pans
–Change filter
–Flush cooler
–Add new fluid
–Check level
–Repair/replace
radiator cooler
–Transmission
overhaul required
–Check for:
DDamaged plates
and seals
DContaminated
solenoids
–Flush cooler
–Add new fluid
–Check level
–Transmission
overhaul required
–Flush cooler and
cooler lines
–Add new fluid
–Check level
*Fluid should be changed according to maintenance
schedule.
Test Driving
Some 4L30–E automatic transmission complaints will
require a test drive as a part of the diagnostic procedure.
Some codes will not set unless the vehicle is moving. The
purpose of the test drive is to duplicate the customer’s
complaint condition and set a current Powertrain Control
Module (PCM) trouble code. Perform this procedure
before each 4L30–E automatic transmission repair, and
again after repairs are made.
IMPORTANT:
DDuplicate the condition under which the customer’s
complaint was observed.
DDepending on the complaint, the line pressure gauge
and the scan tool may be required during the test
drive.
DDuring the test drive, it is important to record all
necessary data from the areas being monitored, for
use in diagnosis. Also listen for and note any unusual
noises.
The following procedure should be used to test drive
4L30–E automatic transmission complaint vehicles:
1.Turn the ignition ON without starting the engine.
Check that the “CHECK TRANS” lamp comes on for
approximately 2 seconds and then goes out and
remains out.
DIf the lamp is flashing, GOTO Check Trans Indicator
in Transmission Control System (4L30–E) section.
DIf no serial data is present, GOTO OBD System
Check. Refer to Driveability and Emissions in
Engine section.
DIf the lamp stays ON or stays OFF, GOTO “Check
Trans” Check in Transmission Control System
(4L30–E) section.
2.Drive the vehicle. During the test drive, be sure that
the transmission achieves normal operating
temperature (approx. 20 minutes).
Allow the transmission to go through all of its gear
ranges, checking shift timing and firmness. Duplicate
the owner’s complaint condition as closely as
possible during the test drive.
3.If, during the test drive, the “CHECK TRANS” lamp
comes on, use the scan tool to check for trouble
codes.
4.If, during the test drive, a problem is felt, but the
“CHECK TRANS” lamp does not come on and no
trouble codes are present, drive the vehicle with the
PCM disconnected (manually shifting the vehicle).
DIn Manual L, the vehicle operates in first gear.
DIn Manual 2, the vehicle operates in third gear.
DIn Manual 3 or “D”, the vehicle operates in fourth
gear.
If the problem still exists with the PCM disconnected,
refer to Mechanical/Hydraulic Diagnosis in this
section.
5.If no problem has been found at this point, check all
underhood connections that supply power to the PCM
and ignition fuses. Physically and visually inspect all
the PCM harness connectors for loose or corroded
terminals. Inspect the PCM ground points.