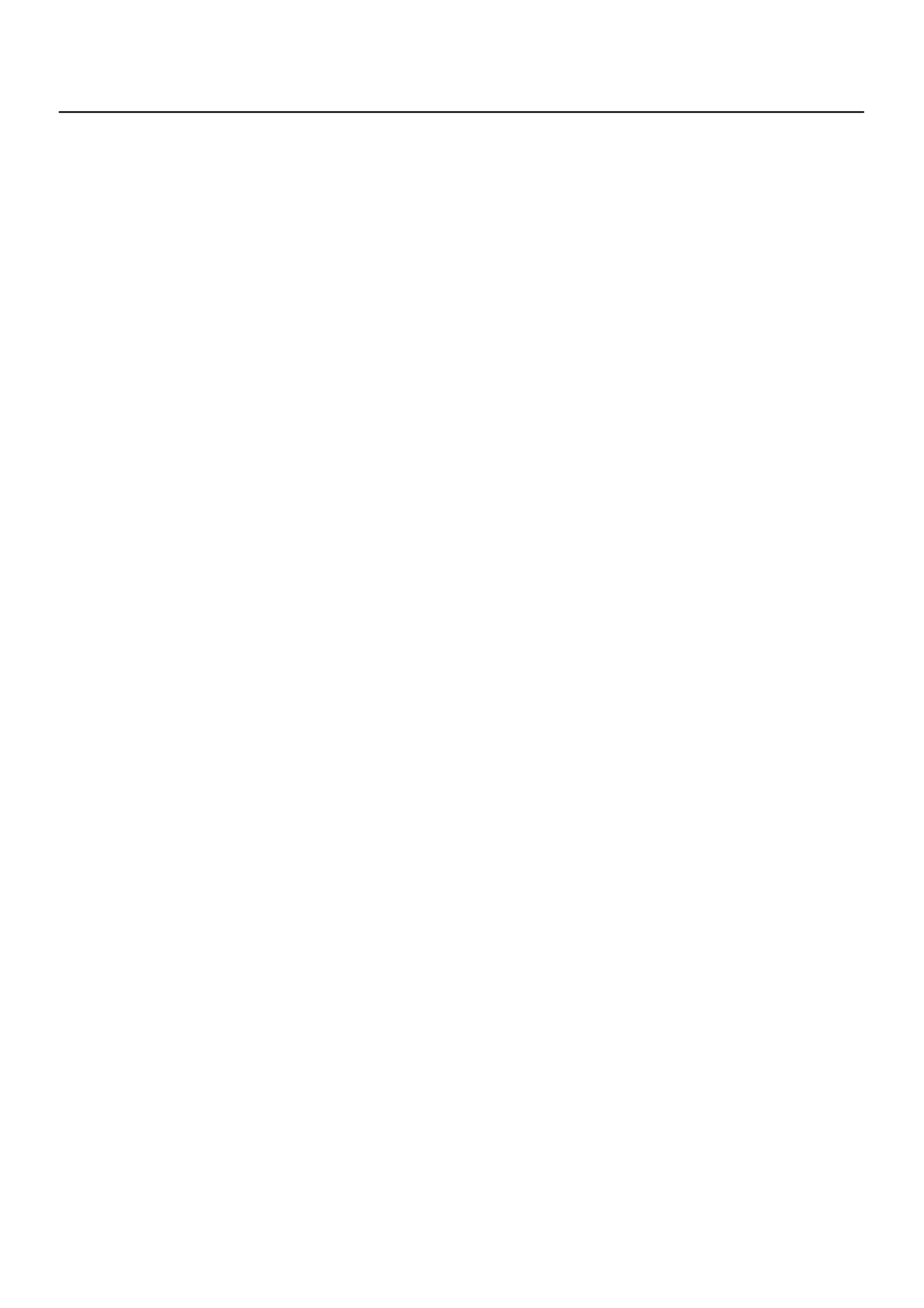
SECTION 7B - MANUAL TRANSMISSION MUA 5C (4X4)
Service Precaution
General Description
Diagnosis (MUA)
Transmission (MUA)
Disassembled View
Removal
Installation
Transmission Case and Transfer Case
Major Component (MUA)
Disassembly
Reassembly
Intermediate Plate with Gear Assembly,
Detent, Shift Arm, and Interlock Pin (MUA)
Disassembled View
Disassembly
Inspection and Repair
Reassembly
Reverse Gear and 5th Gear (MUA)
Disassembled View
Disassembly
Inspection and Repair
Reassembly
Top Gear Shaft, Main Gear Shaft, and
Counter Gear Shaft (MUA)
Disassmebled View
Disassembly
Inspection and Repair
Reassembly
Main Data and Specifications
Special Tools (MUA)
Service Precaution
WARNING: THIS VEHICLE HAS A SUPPLEMENTAL
RESTRAINT SYSTEM (SRS). REFER TO THE SRS
COMPONENT AND WIRING LOCATION VIEW IN
ORDER TO DETERMINE WHETHER YOU ARE
PERFORMING SERVICE ON OR NEAR THE SRS
COMPONENTS OR THE SRS WIRING. WHEN YOU
ARE PERFORMING SER VICE ON OR NEAR THE SRS
COMPONENTS OR THE SRS WIRING, REFER TO
THE SRS SERVICE INFORMATION. FAILURE TO
FOLLOW WARNINGS COULD RESULT IN POSSIBLE
AIR BAG DEPLOYMENT, PERSONAL INJURY, OR
OTHERWISE UNNEEDED SRS SYSTEM REPAIRS.
CAUTION: Always use the correct fastener in the
proper location. When you replace a fastener, use
ONLY the exact part number for that application.
ISUZU will call out those fasteners that require a
replacement after removal. ISUZU will also call out
the fasteners that require thread lockers or thread
sealant. UNLESS OTHERWISE SPECIFIED, do not
use supplemental coatings (Paints, greases, or other
corrosion inhibitors) on threaded fasteners or
fastener joint interfaces. Generally, such coatings
adversely affect the fastener torque and the joint
clamping force, and may damage the fastener . When
you install fasteners, use the correct tightening
sequence and specifications. Following these
instructions can help you avoid damage to parts and
systems.