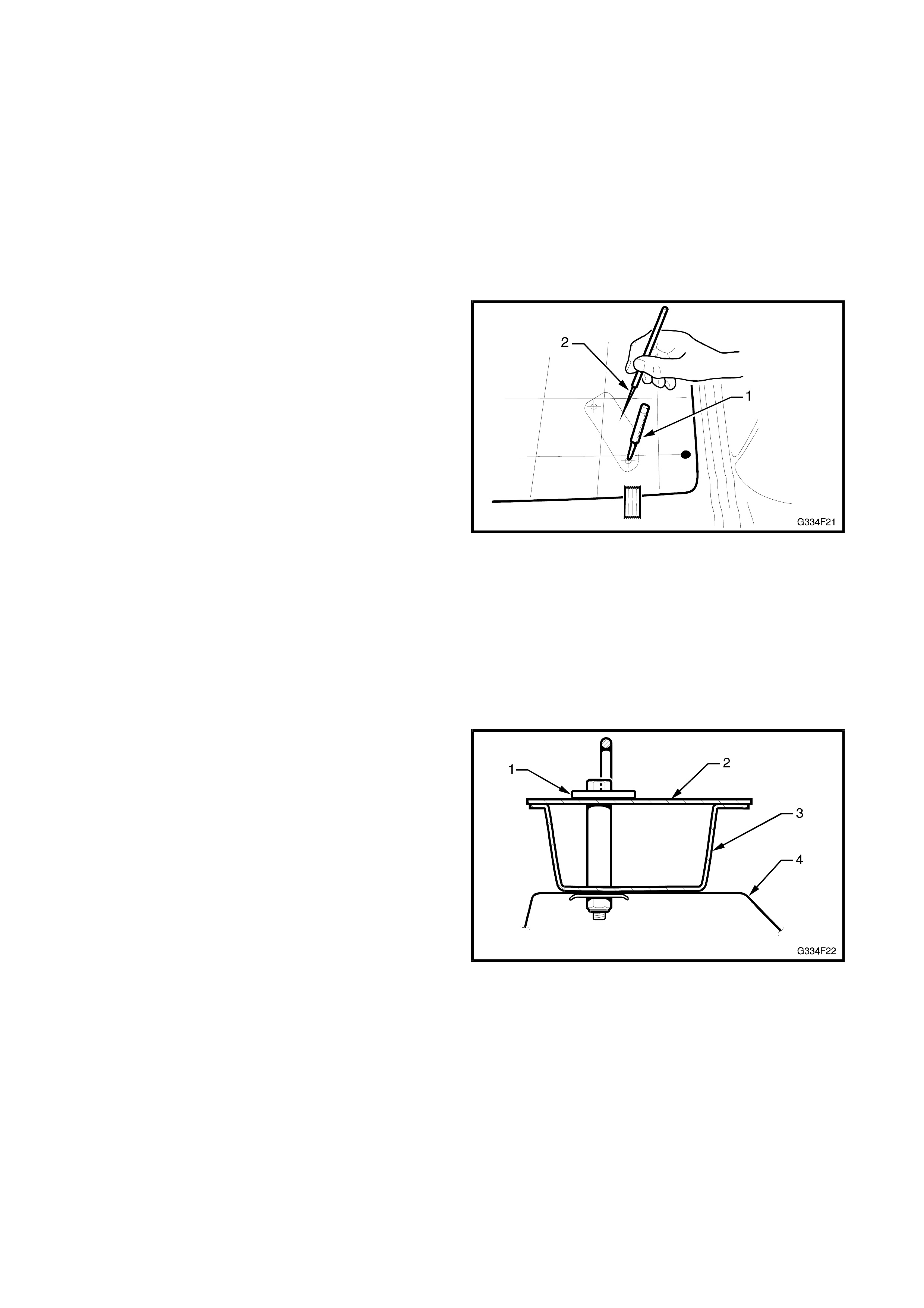
INSTALL
NOTE: If the original mounting holes were
undisturbed, proceed to Step 12.
1. Place the previously constructed template on the
floor ensuring its correct orientation and
alignment with the four alignm ent holes as shown
in Fig. 4F-14, or if no template has been
constructed, refer to 4.6 SEAT MOUNT
MARKING - FLOOR in this Section.
2. Tape the template in position.
3. Centre punch (1) the desired num ber of m ounting
hole locations through the template onto the floor.
4. If required, scribe a dotted guideline (2) through
the template onto the floor at each pivot mount
and striker location, to outline the deadener
removal areas.
Figure 4F-21
5. Remove the template and drill 3 mm pilot holes
for the eight mounting bolts
IMPORTANT: The RH striker plate is mounted
directly over the fuel tank. To prevent puncturing the
tank, when drilling the RH strik er holes a spacer must
be used over the drill bit to ens ure a m ax imum dr ill tip
length of 25 mm will protrude through the drilled
surf ace. A piece of snug f itting hose will suf fic e as the
spacer. Refer Fig. 4F-18.
6. Drill a 10.5 mm hole at the LH striker (1) front
hole location. Drill through the floor (2),
longitudinal (3) and rear muffler heat shield (4).
Refer to Figs. 4F-20 and 4F-22.
NOTE: It is advisable to use a spacer to achieve a
100-110 mm drill tip depth similar to previously
mentioned, to avoid dr illing into the r ear muf fler. Ref er
to Fig. 4F-17.
Figure 4F-22
7. Enlarge the hole to 19 mm through the FLOOR
ONLY.
8. Drill 8.5 mm holes at all other locations, noting the
fuel tank clearance at the RH striker plate as
previously mentioned.