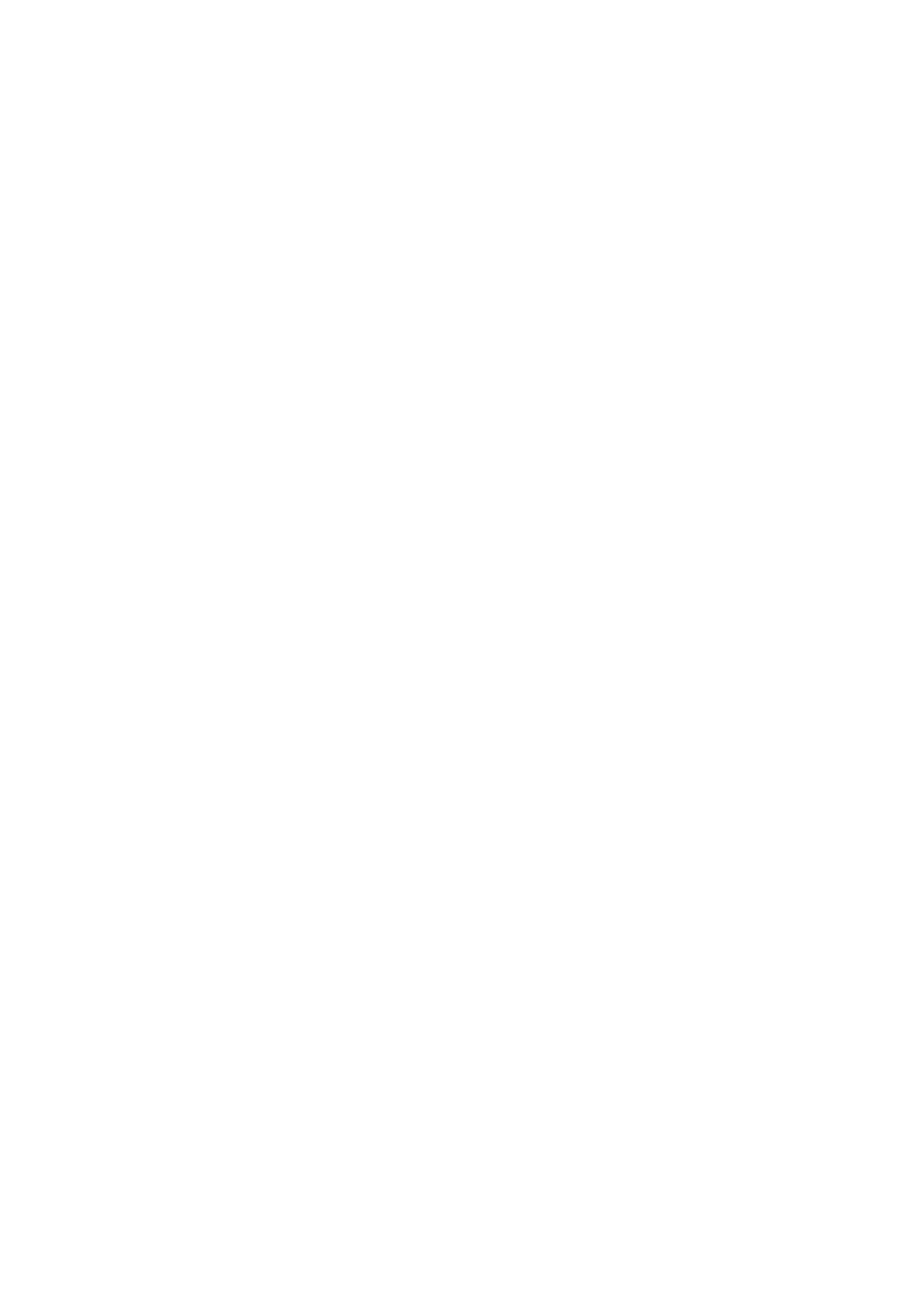
20. Push m ec hanis m into sl ide pos it io n as in s te p 9 ( h ol d adj ustment br acket st able while do ing s o) . If mec hanism
stops after approximately 100 mm (4 in.) preventing a full rearward positioning, you failed to hold the
adjustment bracket stable, repeat step 20.
21. Slide whole mechanism rearwards to allow remounting of locator.
22. Slide the retraction rearwards, remount screw and locator.
23. Repeat steps 10 through 22 to replace other cable.
24. Slide both LH/RH mechanisms to the front position.
25. Push LH/RH mechanisms to closed position. Insert a pin in each 2.5 mm brass hole. (pointed object). Slide
mechanism forward until pin stops the mechanisms movement at the desired location (see Figure J-3).
26. Mount the new gearwheel. Being sure to center it evenly between the walls of the hole in the motor bracket.
Note that the c ore or cent er of the gear has splines (teet h). The spli nes do not exten d completel y to one side
of the gears inner core. This is the down (bottom) side for mounting (see Figure J-5).
27. Mount the new gearwheel housing.
28. Mount the sunroof control unit. Inspect to be sure the two timing spots are aligned in the view finders (top to
bottom) (see Figure J-4). Dropping the front of the S.C.U. low enough for cable clearance slide forward,
engage lip of cable plate in S.C.U. slot. Straighten S.C.U. horizontally and tighten screw.
NOTE: If the timing spots are not aligned, turn the top mount cable gear until each appears aligned over one
another in the view finders (see Figure J-4).
29. Connect the motor to the sunroof control unit (wire one way connector).
30. Remount motor and cover, replace screws.
31. Inspect the sunroof for proper electrical and mechanical functioning.
32. Remount headliner.
33. Remount adjustment bracket, sunshade or ventilation tray and trim tray, drain channel, panel, wind deflector
and mechanism covers.
34. Final inspection of unit.
Timing Of The Drive Cables
1. Fully tilt panel
2. Remove LH/RH mechanism covers.
3. Fully close panel.
4. Drop rear of headliner to access motor cover plate.
5. Remove motor cover, motor now drops down.
6. Disconnect sunroof control unit wires and remove the motor.
7. Dismount sunroof control unit with screw, drop the front and slide back.
8. Remove the ge arwhe el hous ing b y rem oving the two screws.
9. Remove gearwheel by inserting screwdriver, push forward, it drops down
(see Figure J-5).
10. Push m ec hanisms LH/RH to c losed p os ition. Ac c ess eac h 2.5 m m bras s hole with a p in ( p oin ted objec t). Slide
mechanism forward until pin stops the mechanisms movement at the desired location (Figure J-3).
11. Mount the new gearwheel. Being sure to center it evenly between the walls of the hole in the motor bracket.
Note that the c ore or cent er of the gear has splines (teet h). The spli nes do not exten d completel y to one side
of the gears inner core. This is the down (bottom) side for mounting (see Figure J-5).
12. Mount the new gearwheel housing.
13. Mount the sunro of control unit. Insp ect to be sure the two white t im ing spots ar e alig ned in the view fin der (to p
to bottom) (see Figure J-4). Dropping the front of the S.C.U. low enough for cable clearance slide forward,
engage lip of cable plate in S.C.U. slot. Straighten S.C.U. horizontally and tighten screw.
NOTE: If the white timing spots are not aligned, turn the top mount cable gear until each appears aligned over
one another in the vi e w finders (s ee Figure J-4).
14. Connect the motor to the sunroof control unit. (wire one way connector).
15. Remount motor and cover, replace screws.
16. Inspect the sunroof for proper electrical and mechanical functioning.
17. Remount headliner.
18 Remount the LH mechanism cover.
19. Final inspection of unit.