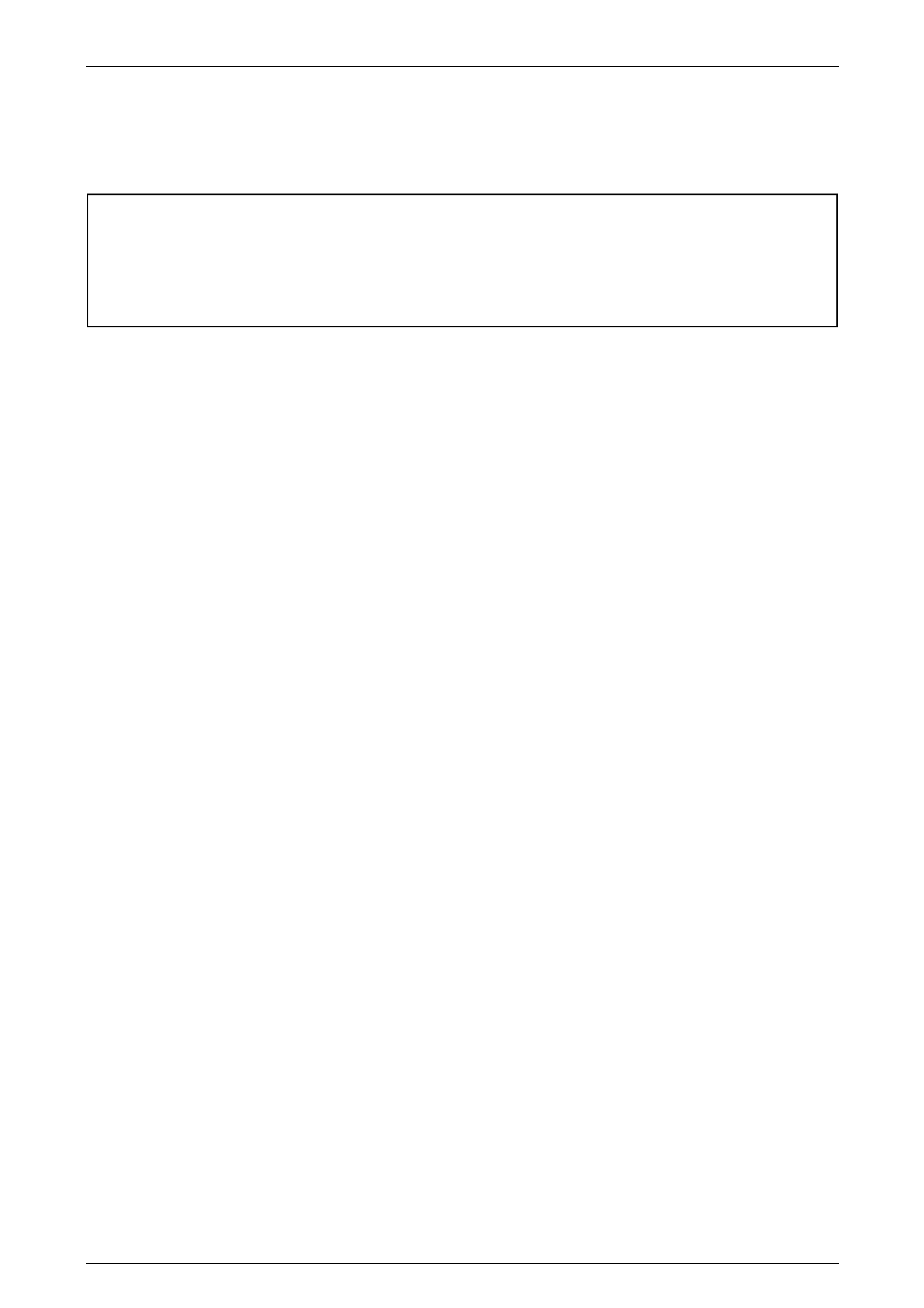
Suspension Page C-1
Page C-1
Section C
Suspension
ATTENTION:
HSV vehicles are equipped with a Supplemental Restraint System (SRS). An SRS consists of seat belt pre-
tensioners (fitted to all front seats), a driver’s-side air bag , a passenger’s-side air bag and left and right hand
side air bags. Refer to CAUTIONS, Section 12M, in Volume 12M of the Holden V2 Coupe Service Manual
before performing any service operation on or around SRS components, the steering mechanism or wiring.
Failure to follow the CAUTIONS could result in personal injury or unnecessary SRS system repairs.
1 Purpose...................................................................................................................................................4
1.1 General Description............................................................................................................................................... 4
2 Wheel Alignment ....................................................................................................................................6
2.1 Steering Geometry................................................................................................................................................. 6
Caster...................................................................................................................................................................... 6
Camber ................................................................................................................................................................... 7
Wheel Toe............................................................................................................................................................... 7
Steering Axis Inclination....................................................................................................................................... 8
Scrub Radius.......................................................................................................................................................... 8
Included Angle....................................................................................................................................................... 9
Toe-Out On Turns.................................................................................................................................................. 9
2.2 Wheel Alignment Checking and Adjustment..................................................................................................... 10
Preliminary Inspection ........................................................................................................................................ 10
Caster Adjustment............................................................................................................................................... 10
Camber Adjustment............................................................................................................................................. 10
Toe Adjustment.................................................................................................................................................... 12
2.3 Jacking Precautions............................................................................................................................................ 13
2.4 Front Wheel Hub Assembly – End Float Checking Procedure ........................................................................ 14
3 Front Suspension.................................................................................................................................15
3.1 Service Notes And Cautions............................................................................................................................... 15
3.2 Front Wheel Hub Assembly and Brake Rotor.................................................................................................... 17
Remove................................................................................................................................................................. 17
Inspect .................................................................................................................................................................. 18
Reinstall................................................................................................................................................................ 19
3.3 Front Wheel Hub Studs....................................................................................................................................... 20
Replace................................................................................................................................................................. 20
3.4 Front Strut Assembly........................................................................................................................................... 22
Remove................................................................................................................................................................. 22
Reinstall................................................................................................................................................................ 24
3.5 Upper Strut Support Bearing and Mount........................................................................................................... 26
Remove................................................................................................................................................................. 26
Reinstall................................................................................................................................................................ 27
3.6 Front Spring ......................................................................................................................................................... 28
Remove................................................................................................................................................................. 28
Reinstall................................................................................................................................................................ 28
3.7 Front Strut Unit .................................................................................................................................................... 29
Replace................................................................................................................................................................. 29
3.8 Steering Knuckle.................................................................................................................................................. 30
Remove................................................................................................................................................................. 30
Reinstall................................................................................................................................................................ 33