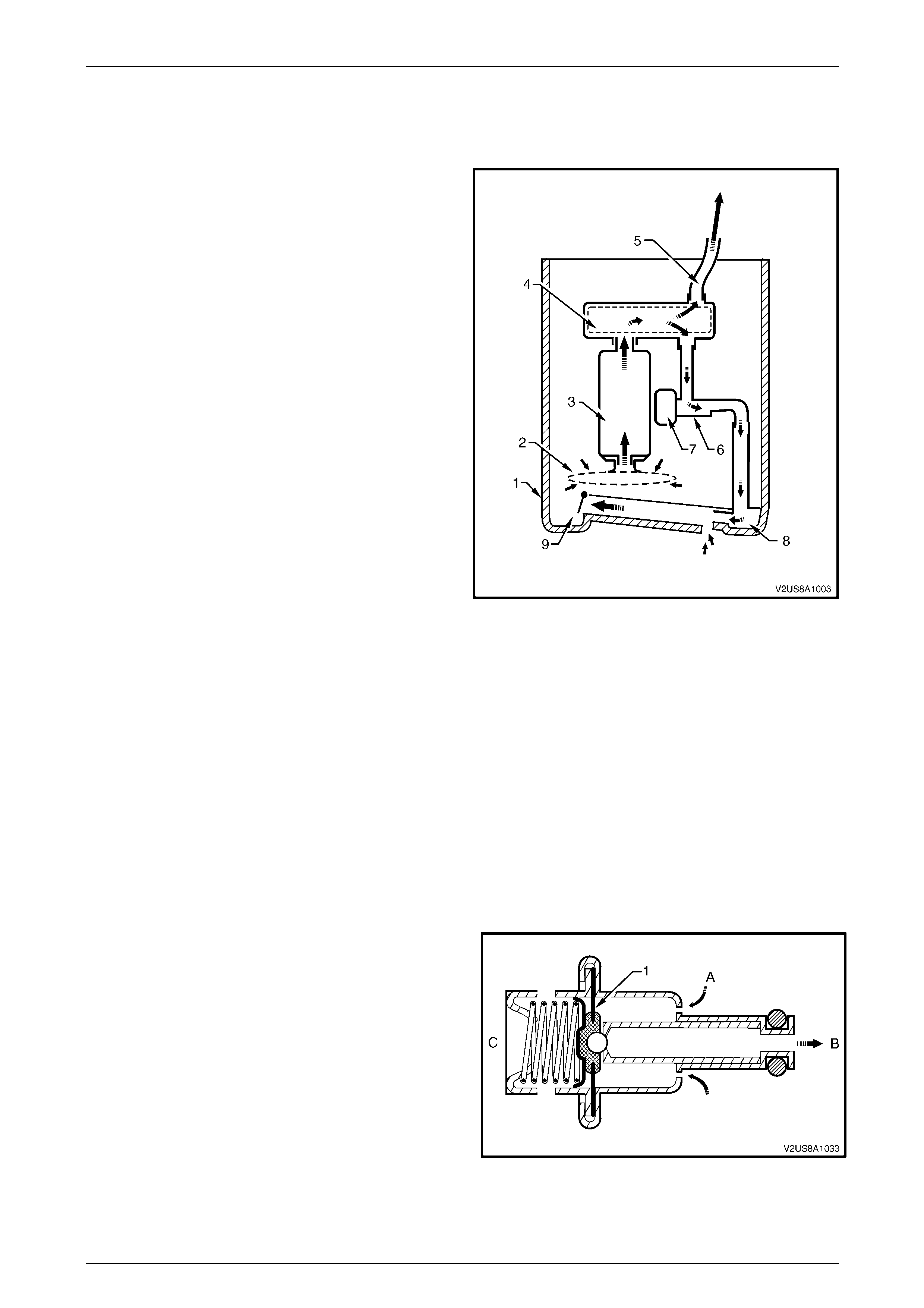
Fuel and Exhaust Systems Page G-10
Page G-10
Fuel Flow Through The Modular Fuel Pump And Sender Assembly
This section provides a general description of fuel flow through the modular fuel pump and sender assembly.
Fuel is pumped from the fuel tank to the engine via the
modular fuel pump and sender assembly.
Fuel in the reservoir (1) is drawn through the fuel strainer (2)
and into the single turbine fuel pump (3) which is driven by a
constant-speed motor. Fuel is then forced through the motor
and out, under pressure, into the fuel filter canister and
through the fuel filter (4). There are two fuel filter exit ports,
one runs into a flexible pipe which connects to the engine fuel
feed line (5) within the fuel tank, and the other provides the
connection port to which the fuel pressure regulator holder
and port assembly (6) is connected.
When the engine is operating, fuel is continuously forced to
flow through the ported pressure regulator holder assembly
which has an extended moulding to enable mounting and
provide the fuel exit port. The fuel pressure regulator (7) is
attached to one side of the holder. The exit port directs fuel
into the reservoir jet pump (8), which is moulded integral to
the reservoir assembly. This pump forces extra fuel into the
reservoir through a one way flapper valve (9) connected at
the base of the reservoir.
Figure 8A1 – 4
Fuel Limiter Vent Valve
A fuel limiter vent valve is incorporated into the modular fuel pump and sender cover assembly. This valve controls the
fuel tank fill level by closing the primary vent from the fuel tank and prevents fuel from exiting the fuel tank via the EVAP
vapor pipe to the canister. The valve also provides fuel spillage protection in the event of a vehicle rollover by closing the
vapor path from the fuel tank to the EVAP canister.
Fuel Tank Pressure Sensor
A fuel tank pressure sensor is mounted to the cover of the modular fuel tank and sender assembly. When the Powertrain
Control Module (PCM) commands a vacuum into the fuel system to check for leaks, a potential voltage is induced by the
sensor and this voltage will fluctuate according to the pressure change in the fuel tank. The change in voltage is
monitored by the PCM through a circuit carried through the body wiring harness and fuel tank wiring harness.
Pressure Regulator
The fuel pressure regulator is a diaphragm-operated relief
valve located in the modular fuel pump and sender assembly.
Its principal function is to maintain a controlled pressure at
the injectors at all times by regulating fuel flow into the fuel
feed line.
Fuel flows from the fuel pump, into the fuel filter and is
allowed to exit the filter into the fuel feed line or the fuel
pressure regulator entry port. From here, fuel flows under
pressure into the pressure regulator at location A. When fuel
pressure builds in the fuel feed line, the diaphragm and
valve (1) inside the fuel pressure regulator is progressively
pushed out, allowing fuel to exit through the regulator port at
location B. The valve is otherwise held closed by mechanical
spring pressure applied from side C. Fuel exiting the
regulator is directed into the reservoir jet pump to provide
continuous fuel circulation.
Figure 8A1 – 5