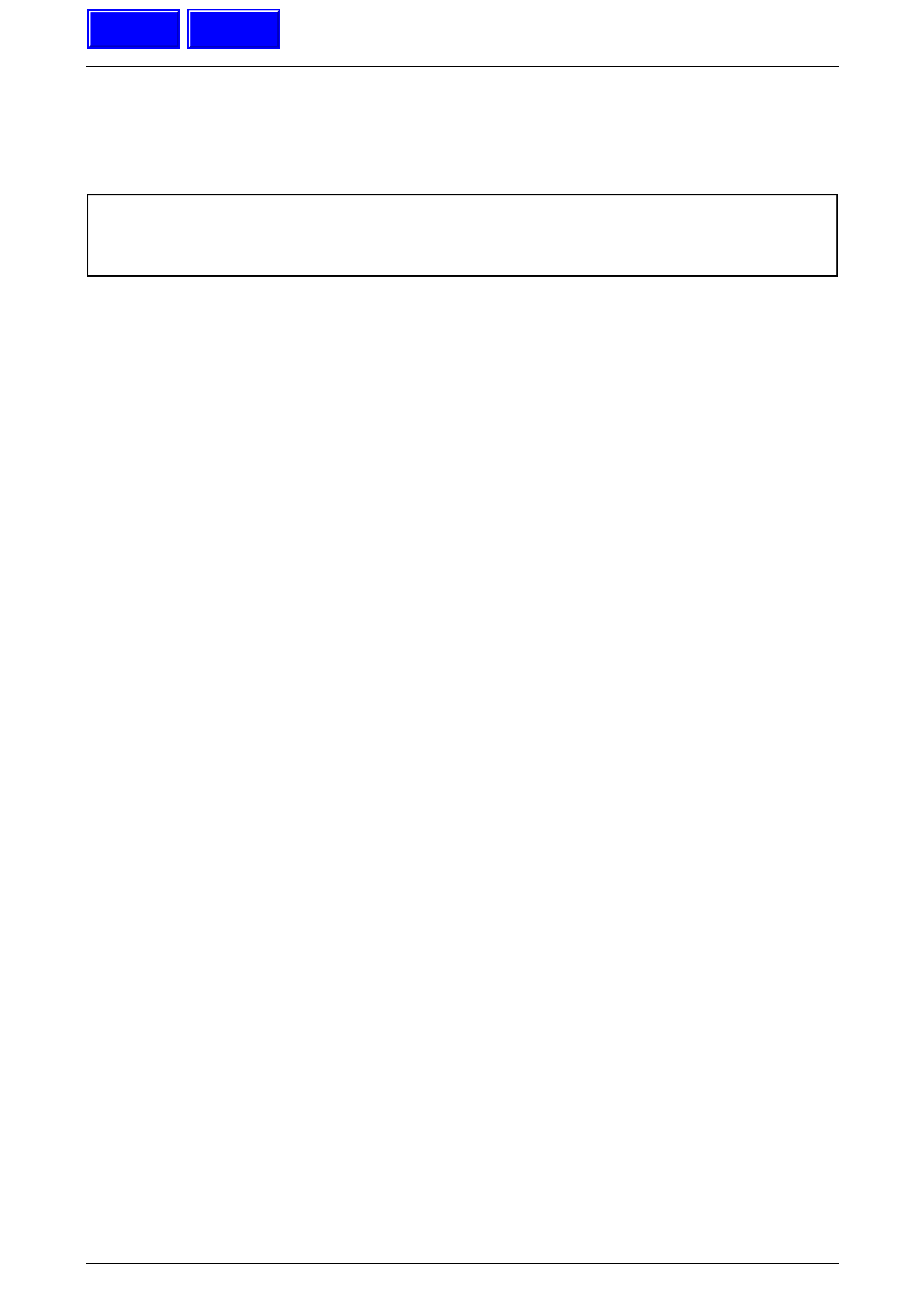
Engine Mechanical – HSV – Gen IV V8 Page 6A4–1
Page 6A4–1
Section 6A4 -
Engine Mechanical – HSV – Gen IV V8
ATTENTION
Before performing any service operation or other procedure described in this Section, refer to Section 00
Warnings, Cautions and Notes for correct workshop practices with regard to safety and/or property damage.
1 General Information ...............................................................................................................................3
1.1 Engine View............................................................................................................................................................ 4
Left-hand Side........................................................................................................................................................ 4
Lower Front of Engine...........................................................................................................................................5
Intake Manifold – Upper Engine............................................................................................................................ 6
1.2 Engine Number ...................................................................................................................................................... 7
1.3 Engine Construction.............................................................................................................................................. 8
Cylinder Block........................................................................................................................................................ 8
Pistons and Connecting Rods.............................................................................................................................. 9
Camshaft and Drive ............................................................................................................................................. 10
Intake Manifold..................................................................................................................................................... 10
1.4 Engine Lubrication Sy s t em................................................................................................................................. 11
Positive Crankcase Ventilation System............................................................................................................. 11
2 Minor Service Operations....................................................................................................................12
2.1 Manifold Absolute Pressure Sensor .................................................................................................................. 12
Remove................................................................................................................................................................. 12
Reinstall................................................................................................................................................................ 12
2.2 Intake Manifold..................................................................................................................................................... 13
Remove................................................................................................................................................................. 13
Disassemble......................................................................................................................................................... 19
Clean and Inspect................................................................................................................................................ 20
Reassemble.......................................................................................................................................................... 21
Reinstall................................................................................................................................................................ 22
2.3 Engine Valley Cover ............................................................................................................................................ 24
Remove................................................................................................................................................................. 24
Clean and Inspect................................................................................................................................................ 25
Reinstall................................................................................................................................................................ 25
2.4 Valve Rocker Arm Cover..................................................................................................................................... 26
Remove................................................................................................................................................................. 26
Clean and Inspect................................................................................................................................................ 30
Reinstall................................................................................................................................................................ 30
2.5 Cylinder Head Assembly..................................................................................................................................... 32
Remove................................................................................................................................................................. 32
Disassemble......................................................................................................................................................... 34
Clean and Inspect................................................................................................................................................ 35
Valve Springs................................................................................................................................................... 37
Valves .............................................................................................................................................................. 37
Valve Guides.................................................................................................................................................... 38
Oversize Valve Stem........................................................................................................................................ 39
Valve Seats...................................................................................................................................................... 39
Reassemble.......................................................................................................................................................... 40
Reinstall................................................................................................................................................................ 42
2.6 Engine Dress Cover............................................................................................................................................. 44
Remove................................................................................................................................................................. 44
Reinstall................................................................................................................................................................ 44