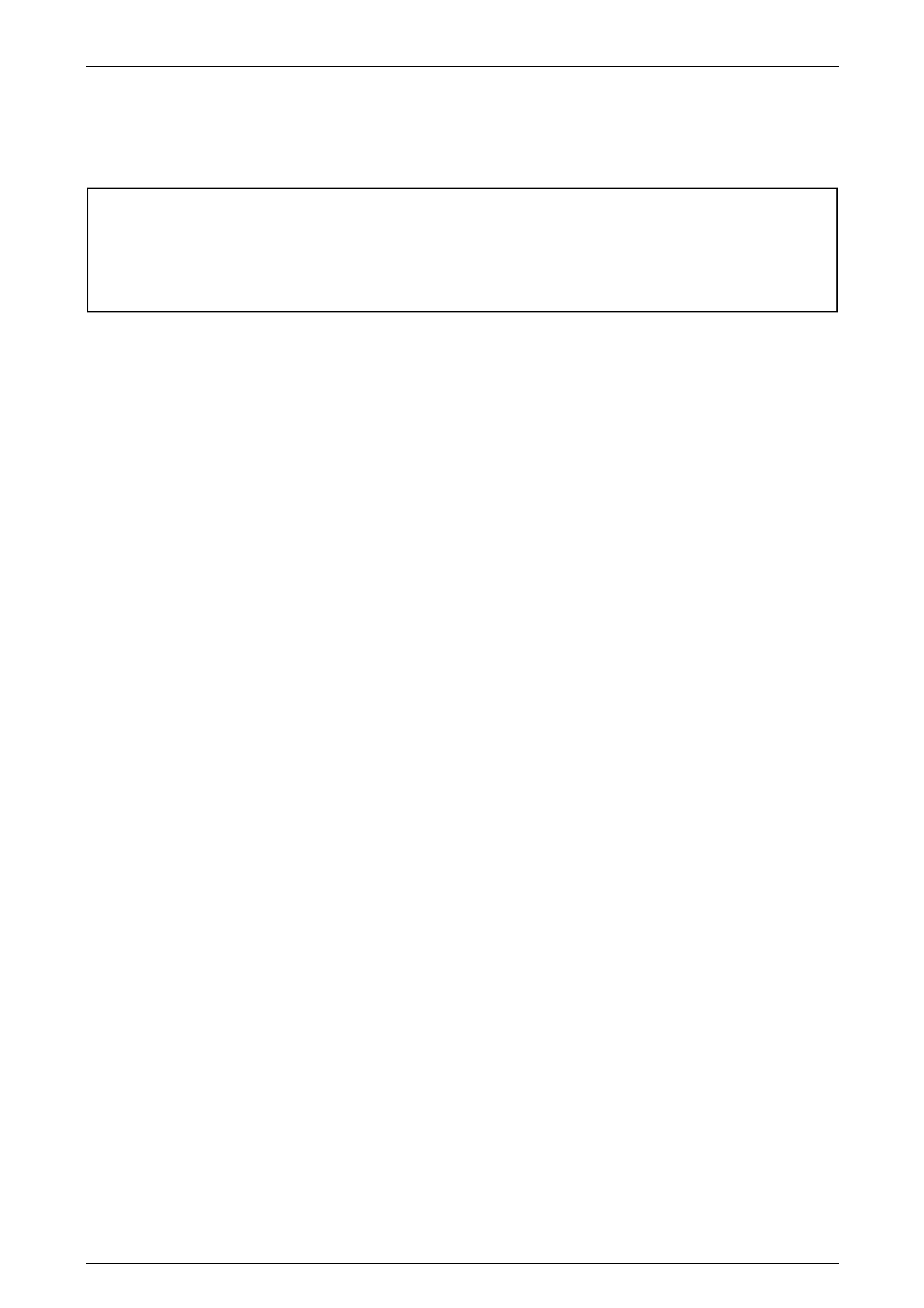
Suspension Page C-1
Page C-1
Section C
Suspension
ATTENTION
HSV vehicles are equipped with a Supplemental Restraint System (SRS). An SRS consists of seat belt pre-
tensioners (fitted to all front seats), a d river’s-side air bag, a passeng er’s-side air bag and left and right h and
side air bags. Refer to CAUTIONS, Section 12M Occupant Protection System in th e MY 2005 VZ Series Ser vice
Information before performing any service operation on or around SRS components, the steering mechanism
or wiring. Failure to follow the CAUTIONS could result in personal injury or unnecessary SRS system repairs.
1 Purpose...................................................................................................................................................2
2 Front Suspension...................................................................................................................................3
2.1 General Information............................................................................................................................................... 3
2.2 Service Intervals .................................................................................................................................................... 4
2.3 Service Operations................................................................................................................................................ 5
2.4 Front Suspension Components............................................................................................................................ 6
Front Strut Detail.................................................................................................................................................... 6
Front Spring Detail................................................................................................................................................. 6
Front Stabiliser Bar Detail..................................................................................................................................... 7
3 Rear Suspension....................................................................................................................................8
3.1 General Information............................................................................................................................................... 8
3.2 Service Operations................................................................................................................................................ 9
3.3 Rear Suspension Components........................................................................................................................... 10
Rear Spring Detail................................................................................................................................................ 10
Rear Shock Absorber Detail................................................................................................................................ 10
Rear Stabiliser Bar Detail.................................................................................................................................... 11
4 Suspension Ohlins Supplement.........................................................................................................12
4.1 General Information............................................................................................................................................. 12
4.2 Servicing/Inspection and Maintenance.............................................................................................................. 13
Inspection Points................................................................................................................................................. 13
5 Rear Final Drive and Drive Shafts.......................................................................................................17
5.1 General Information............................................................................................................................................. 17
5.2 Major Service Operations.................................................................................................................................... 18
Final Drive Assembly Unit Repair....................................................................................................................... 18
Reassemble ..................................................................................................................................................... 18
5.3 Pinion Flange ....................................................................................................................................................... 24
Replace (Vehicles With a Rear Rubber Coupling)............................................................................................. 24
Using Old Oil Seal............................................................................................................................................ 24
6 Suspension Service Alignment Data..................................................................................................27
Rear Suspension Service Alignment Data......................................................................................................... 27
Front Suspension Service Alignment Data........................................................................................................ 27
Service Information ............................................................................................................................................. 28
7 Special Tools ........................................................................................................................................29