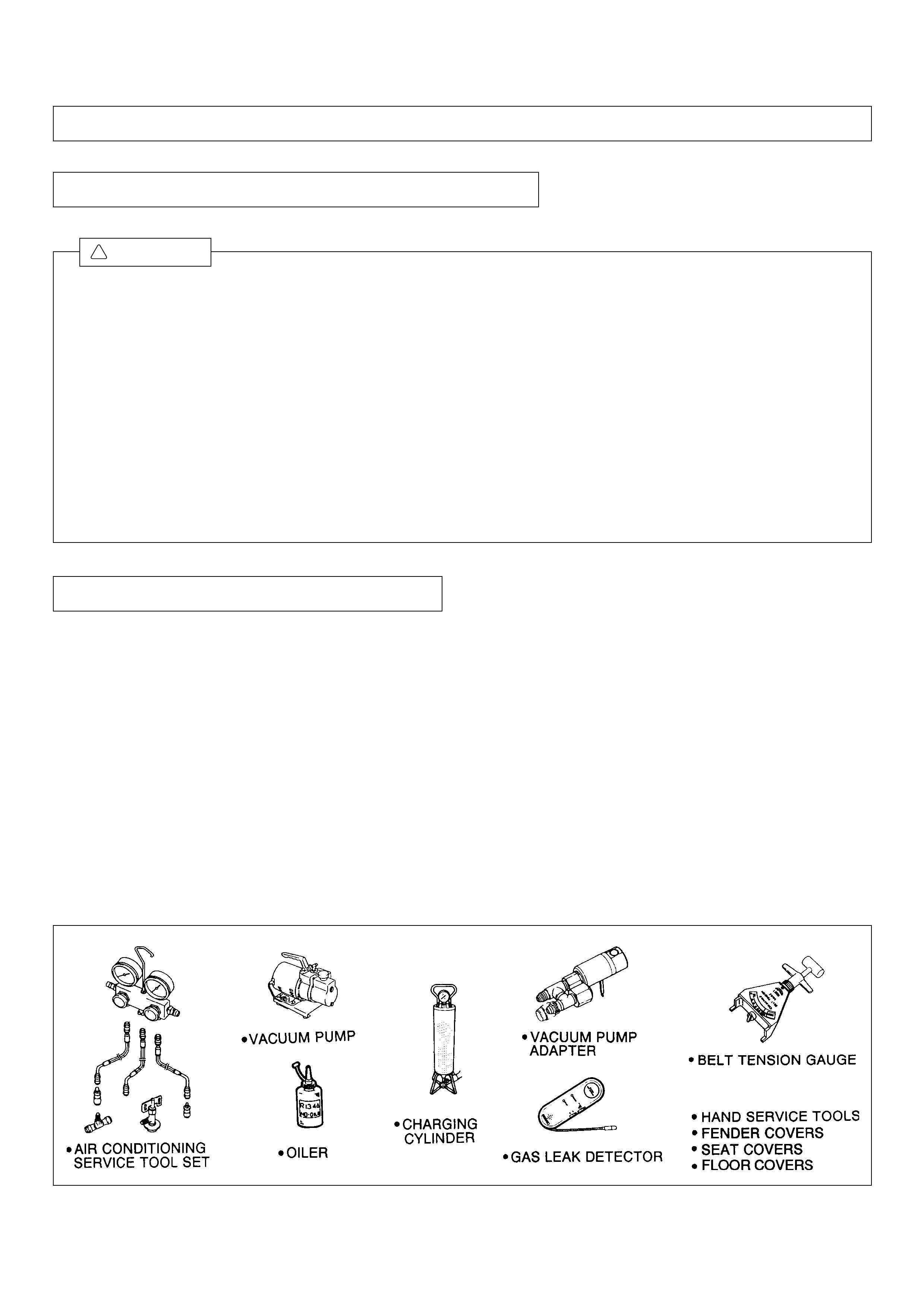
– 1 –
1. GENERAL INFORMATION
1-1 PRECAUTIONS DURING INSTALLATION
1. The contents given in “WARNING” and “CAUTION “ in this manual must be adhered to during installation. If they
are ignored, not only the functions of the air conditioning are hindered, but also personal injury or damage to the
vehicle may result. Always carry out the installation in accordance with the “WARNING” and “CAUTION” as noted.
2. Safety Precautions
(a) If installation is carried out by more than two persons, always pay attention to co-worker’s safety.
(b) When the engine is running, make sure that sufficient ventilation is provided.
(c) Take special care when working with heated, rotating, sliding, or moving parts, to prevent bodily injury.
(d) When raising the vehicle, refer to the appropriate manufacturer’s service manual.
(e) For heavy duty trucks, when tilting the cabin forward, refer to the service manual provided by the vehicle’s
manufacturer to prevent damage or personal injury. Make sure the cabin is locked down after it has been tilted
forward to prevent it from closing.
1-2 INSTALLATION PREPARATION
(1) Prior to installing the air conditioning, check the following for damage or malfunctions.
(a) Internal and external trim and bodywork.
(b) Engine idle speed.
(c) Engine cooling system.
(d) All vehicle functions. (Headlights, indicators, horn, etc.)
(2) Air Conditioning parts preparation
(a) Make sure that the correct kit has been selected for the installation.
(b) When unpacking the kit, lay out all parts in order of installation and check for missing or damaged parts.
(c) When installing the air conditioning, use fender covers, floor covers and seat covers for protection.
[INSTALLATION TOOLS]
WARNING
!