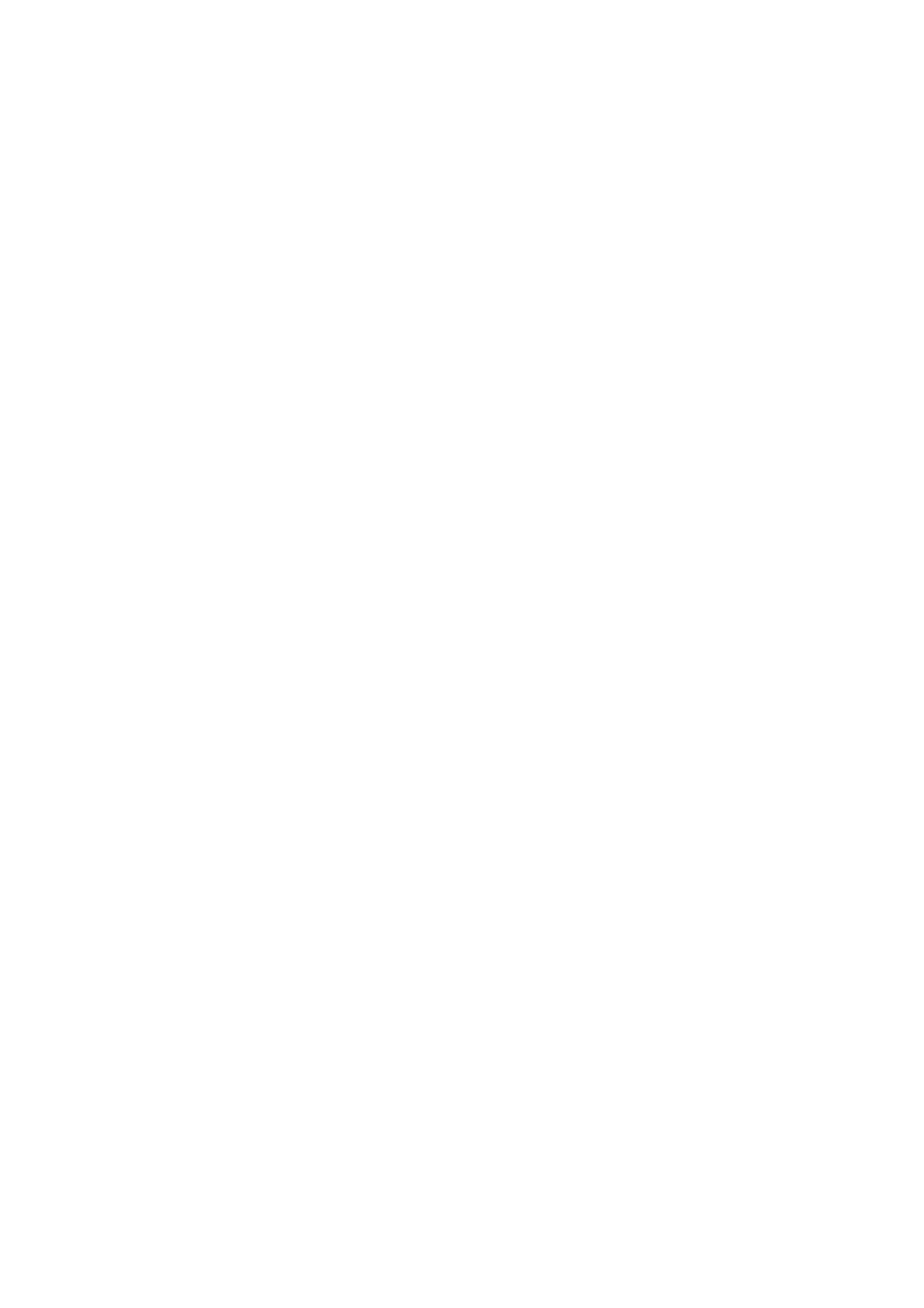
Clear DTC
NOTE: If you clear the DTC (Diagnostic Trouble
Codes) you will not be able to read any codes recorded
during the last occurrence.
NOTE: To use the DTC again to identify a problem, you
will need to reproduce the fault or the problem. This
may require a new test drive or just turning the ignition
on (this depends on the nature of the fault).
1.IF you have a Tech2:
1.Connect the Tech2 if it is still not connected
GOTHROUGH Tech2 OBD II CONNECTION.
2.Push “F1= Clear DTC Info” in the Application
Menu and answer “Yes” to the question “Do you
want to clear DTC's?”
aWhen a malfunction remains as it is the
Tech2 displays“4L30E CODES NOT
CLEARED”. This means that the problem
is still there or that the recovery was not
done. Please GOTO DTC CHECK.
bWhen a malfunction has been repaired and
the recovery is done. The Tech2
displays“4L30E CODES CLEARED”.
2.IF you have no Tech2:
To clear the DTC, remove Fuse “Stop, A/T CONT”
(C–14, 15A) for at least 10 seconds.
DTC Check
1.Diagnostic Trouble Codes (DTC) have been
identified by Tech2.
2.You have written the list of the DTCs. The order of
the malfunctions has no meanings for this PCM.
Usually only one or two malfunctions should be set
for a given problem.
3.Check directly the DTCs you identified. The DTCs
are sorted by number. Refer to Diagnostic Trouble
Code (DTC) Identification in this section.
PCM Precaution
The PCM can be damaged by:
1. Electrostatic discharge
2. The short circuit of some terminals to voltage or to
ground.
Electrostatic Discharge Damage Description:
1. Electronic components used to control systems are
often designed to carry very low voltage, and are
very susceptible to damage caused by electrostatic
discharge. It is possible for less than 100 volts of
static electricity to cause damage to some electronic
components. By comparison, it takes as much as
4,000 volts for a person to even feel the zap of a
static discharge.
2. There are several ways for a person to become
statically charged. The most common methods of
charging are by friction and induction. An example
of charging by friction is a person sliding across a
car seat, in which a charge of as much as 25,000
volts can build up. Charging by induction occurs
when a person with well insulated shoes stands
near a highly charged object and momentarily
touches ground. Charges for the same polarity are
drained off, leaving the person highly charged with
the opposite polarity. Static charges of either type
can cause damage, therefore, it is important to use
care when handling and testing electronic
components.
NOTE: To prevent possible electrostatic discharge
damage:
1. Do not touch the PCM connector pins or soldered
components on the PCM circuit board.
2. Be sure to follow the guidelines listed below if
servicing any of these electronic components:
3. Do not open the replacement part package until it is
time to install the part.
4. Avoid touching electrical terminals of the part.
5. Before removing the part from its package, ground
the package to a known good ground on the vehicle.
6. Always touch a known good ground before handling
the part. This step should be repeated before
installing the part if the part has been handled
while sliding across the seat, while sitting down from
a standing position or while walking some distance.
Information On PCM
1. The Powertrain Control Module (PCM) is located in
the center console and is the control center of the
electronic transmission control system.
2. The PCM must be maintained at a temperature
below 85°C (185°F) at all times. This is most
essential if the vehicle is put through a paint baking
process. The PCM will become inoperative if its
temperature exceeds 85°C (185°F). Therefore, it is
recommended that the PCM be removed or that
temporary insulation be placed around the PCM
during the time the vehicle is in a paint oven or other
high temperature process.
3. The PCM is designed to process the various inputs
and then respond by sending the appropriate
electrical signals to control transmission upshift,
downshift, shift feel and torque converter clutch
engagement.
4. The PCM constantly interprets information from the
various sensors, and controls the systems that
affect transmission and vehicle performance. By
analyzing operational problems, the PCM is able to
perform a diagnostic function by displaying DTC(s)
and aid the technician in making repairs.