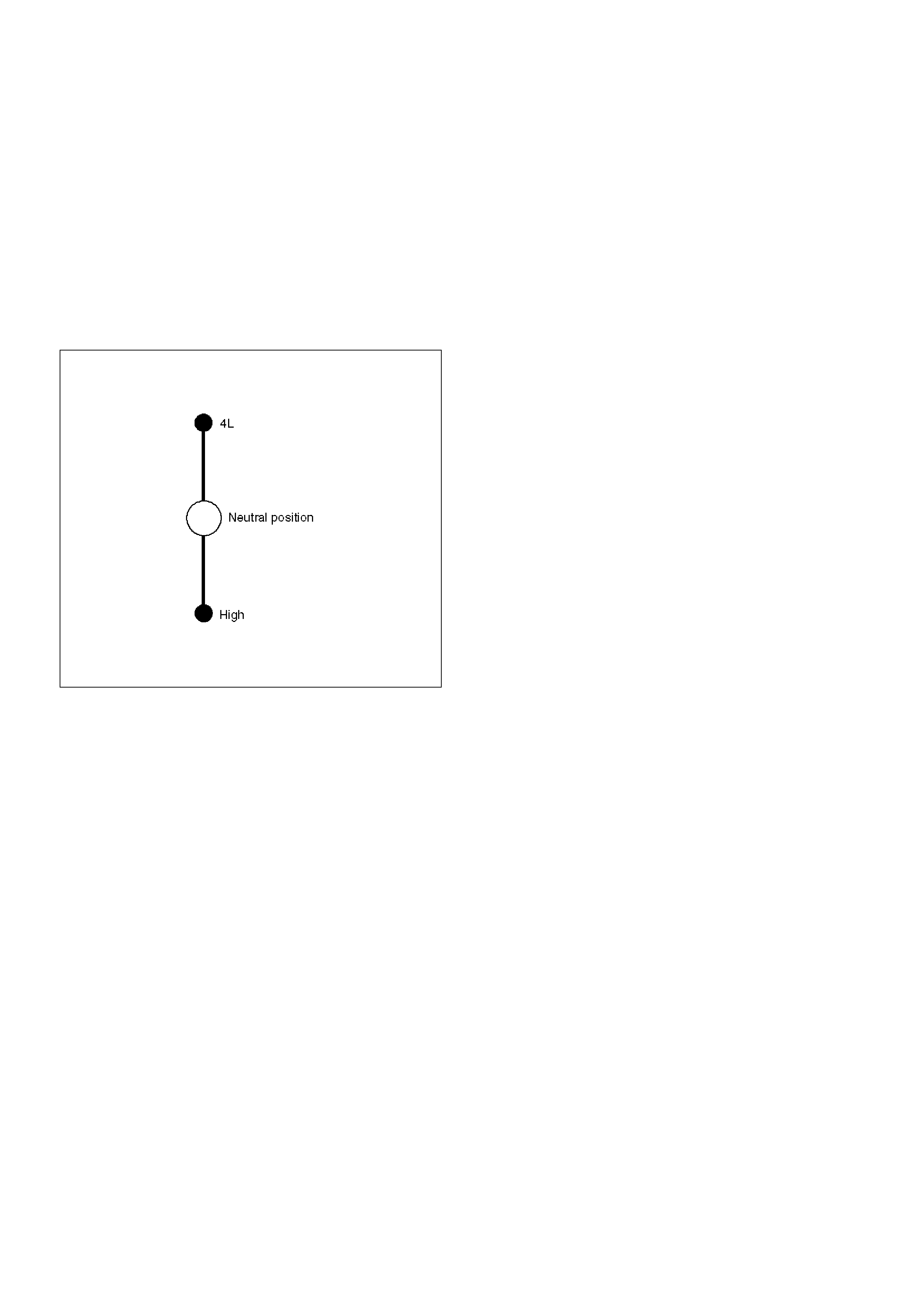
How to Clear The Trouble Code
The trouble codes saved to the control unit can be
deleted by the following procedure if the starter switch is
being in the OFF position.
1. Shift the transfer lever to the neutral position
between HIGH and 4L, and short-circuit the
self-diagnostic connector.
NOTE: The neutral position between HIGH and 4L
refers to the point that turns off the TOD indicator lamps.
(However, be sure to check the position before
short-circuiting the self-diagnostic connector.)
C07RW011
2. Turn on the starter switch while maintaining the
state of step 1, and step on the brake pedal five
times within five seconds from the first step on.
(Note that “five times” includes the first step on).
(The TOD indicator lamps display the 4L mode
whenever the brake pedal is stepped on.)
3. If the conditions shown in steps 1 and 2 are met, the
trouble codes saved to the control unit are cleared.
(After the codes are completely deleted, the code 12
that indicates the normal condition is continuously
displayed.)
Precautions on Diagnosis
Replacement of Control Unit
The control unit itself rarely fails. In most cases, the
harnesses have failed (i.e. short-circuit) to cause
secondary troubles. Other cases include that the cause
has been unknown due to intermittent occurrence of
troubles and the troubles are removed accidentally
along with replacement of control unit, resulting in
misjudgment of cause. Therefore, before replacing the
control unit, check the connector joints and whether the
unspecified current flows in the control unit due to
short-circuit between harnesses.
Intermittent Failures
Troubles which are intermittently observed are mostly
attributable to temporary imperfect connection of
harnesses and connectors.
When such troubles are found, check the associated
circuit according to the following procedure.
1. Check whether improper connectors are plugged in
or connector terminals are completely engaged.
2. Check whether the terminals are deformed or
damaged. If yes, remove the deformation or
damage and connect the terminals securely.
3. It is likely that wires in the harness are falsely
broken. Therefore, in examination of failed harness
circuit, shake the harness for check to such extent
that the harness will not be damaged.
Test Run of Failed TOD Vehicle
If the TOD indicator lamps experienced faulty operation
even once in the past, the failed portion can be
identified by use of the procedure “Diagnosis from
Trouble Codes” or “Trouble Diagnosis Depending on
The Status of TOD Indicator”. If the troubles that are
only recognized as abnormal phenomena of the vehicle
by the driver are observed, conduct the test run in the
following procedure to reproduce the faulty phenomena
and diagnose the fault for each fault.
1. Start the engine, and check that the TOD indicator
lamps are turned on for about two seconds for initial
check; the CHECK lamp goes off; and the TOD
indicator lamps display the specified drive mode. (If
the CHECK lamp starts blinking, read the trouble
codes and identify the failed portion.)
2. While keeping the vehicle standstill, operate the
4WD switch and shift the transfer lever to change
the modes: 2H mode®TOD mode®4L mode®TOD
mode®2H mode. Check that the TOD indicator
lamps correctly display the status whenever the
mode is changed. If the transition status is
displayed during the shift operation, run the vehicle
a little to complete shifting.
3. Slowly start the vehicle in the TOD mode, and add
the power to accelerate to at least 40 km/h and
maintain the speed for about two minutes. Apply
the brake to completely stop the vehicle. Repeat
this test pattern at least three times.
4. Turn the steering to the right end (or left end) in the
TOD mode, and slowly start the vehicle and make a
circle five times. Next, conduct the same test in the
2H mode.
5. Slowly start the vehicle in the TOD mode, and
accelerate to at least 40 km/h. Keep the established
speed, carefully change the mode in the sequence
“TOD mode®2H mode ®TOD mode” while
checking that the shift is complete in each mode
change. After the test, apply the brake to
completely stop the vehicle.