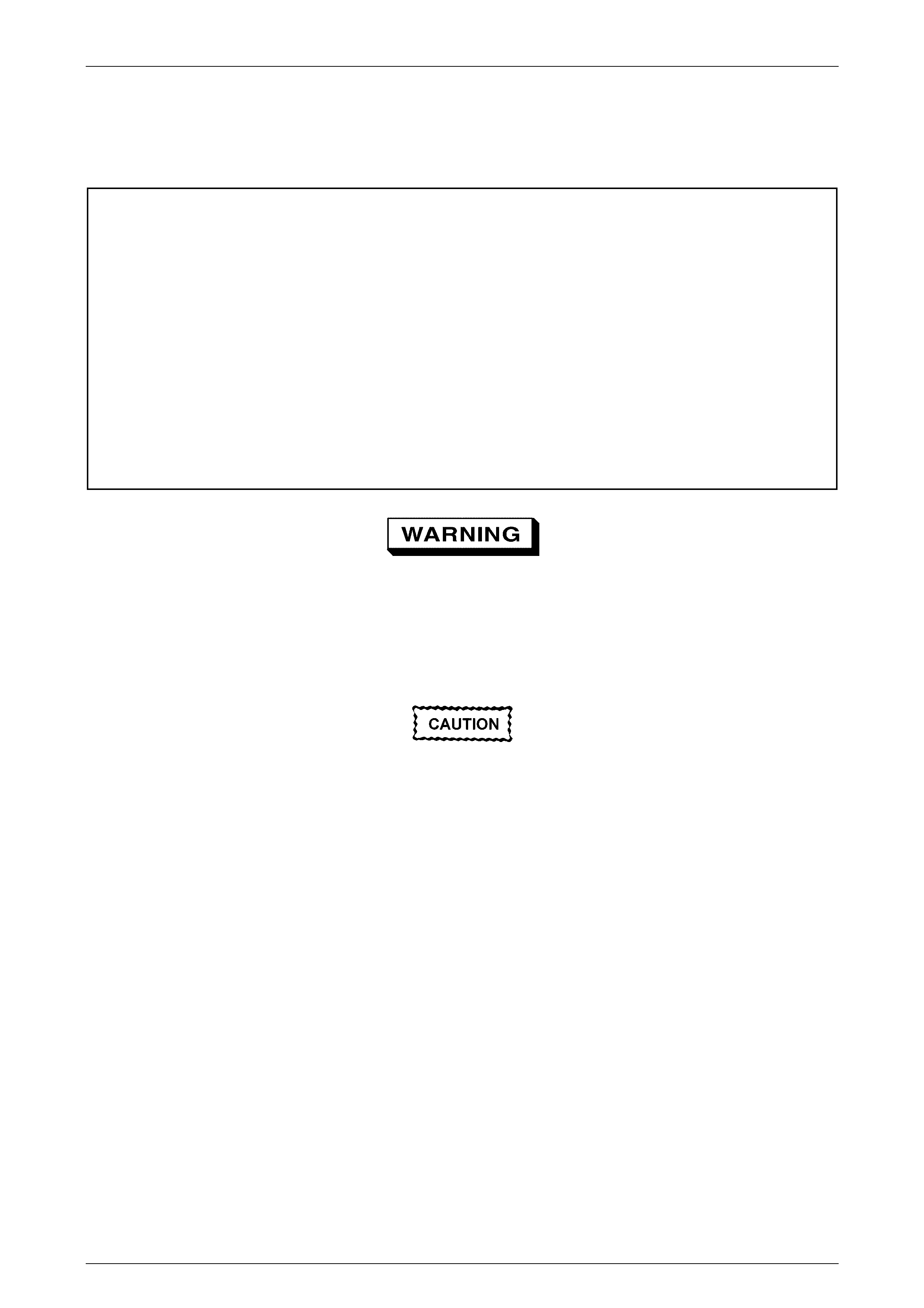
Rear Suspension Page 4A-14
Page 4A-14
2.4 Rear Suspension Crossmember
LT Section No. – 07-150
ATTENTION
The following fasteners MUST be replaced when performing these operations:
!
!!
! Rear suspension crossmember rear mount to under body attaching bolt.
!
!!
! Rear suspension crossmember front mounting bolt.
!
!!
! Differential carrier to rear suspension crossmember attaching bolts.
The following fasteners have either micro encapsulation or incorporate a mechanical thread lock and should
only be used once. If in doubt, replacement is recommended when performing this operation:
" Rear suspension crossmember front mounting brace to under body attaching bolts.
" Additional control arm inner shaft attaching nut.
" Rear suspension control arm to rear suspension crossmember attaching nut.
The following fasteners MUST be at curb height before final tightening:
•
••
• Rear suspension control arm to rear suspension crossmember attaching nut.
•
••
• Shock absorber lower mounting bolt.
Whenever any component that forms part of
the ABS – TC is disturbed during Service
Operations, it is vital that the complete ABS
system be checked, using the detailed
procedure. Refer to Section 5B AW D ABS – TC
in the MY 2004 AWD Wagon Service
Information.
Before disturbing the rear suspension
crossmember mounting bolts, an alignment
procedure is required on installation and a
special tool is required for this purpose. If this
tool is not available, then the crossmember
cannot be correctly aligned and steering
and/or handling abnormalities will result.
Remove
Apart from the items mentioned here, refer to 2.5 Rear Suspension Crossmember, R emove, in Section 4A Rear
Suspension, in the MY 2003 VY and V2 Series Service Information:
1 For removal of the exhaust system necessary for this operation, refer to Section 8B, Exhaust System, in the MY
2004 AWD Wagon Service Information for details relating to the removal and installation of the exhaust
components (including heat shields).
2 To remove the rear propeller shaft assembly, refer to Section 4C1 Rear Propeller Shaft, in the MY 2004 AWD
Wagon Service Information.
3 When removing the rear mount to underbody bolts, a spacer is located betwe en the mount and the underbody
surface.
4 For those MY 2004 AWD Wagon models fitted with the automatic level ride suspension, there are specific
procedures relating to the system air pressure and the treatment of the rear shock absorbers. For these
procedures, refer to the noted operations in Section 4A Rear Suspension, in the MY 2004 WK Series Service
Information:
3.4 Relieving System Air Pressure
3.7 Level Ride Shock Absorber