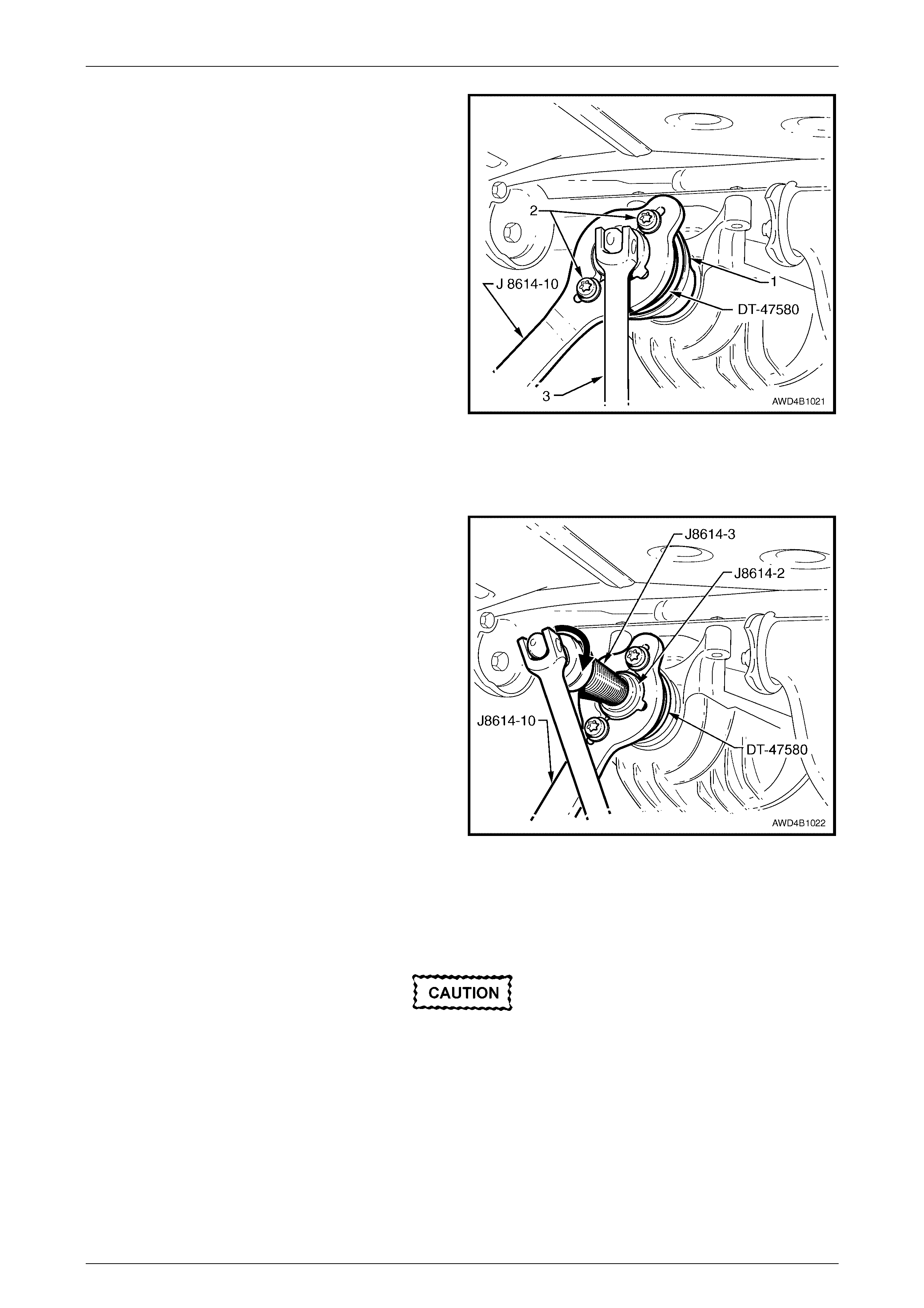
Rear Final Drive & Driveshafts Page 4B1–20
Page 4B1–20
6 Install packing flange, Tool No. DT-47580 into the
pinion flange recess, aligning the holes with those in
the pinion flange.
7 Using two of the propeller shaft constant velocity joint
bolts (2), with flat washers, secure the holding bar,
Tool No. J8614-10 (part of Tool No. J 8614-O1) to the
pinion flange (1). The central recesses in the holding
tool should face inw ard.
8 While anchoring Tool No. J8614-10, loosen the pinion
flange retaining nut, using a commercially available,
30 mm deep socket and socket bar (3), until end play
can be felt in the pinion shaft.
NOTE
A suitable length of pipe installed over the end of
the socket bar will reduce the effort required to
loosen the pinion flange nut.
9 Check the oil seal and differential side bearing pre-
load using the spring scale and pulley, as detailed in
steps 4a and 4b. Record oil seal and side bearing pre-
load for later use.
Figure 4B1 – 29
10 Place drain tray beneath differential carrier.
11 With Tool Nos J8614-10 and DT-47580 still installed,
thread the forcing screw, Tool No. J8614-3, into the
adaptor, Tool No. J8614-2. Install this sub-assembly
into holding bar, Tool No. J8614-10, then rotate
through 45° to locate in the recesses in J8614-10.
12 While holding J8614-10, use a socket and bar to rotate
the forcing screw J8614-3 in the direction shown, to
remove the pinion flange.
13 Remove the tools from the pinion flange, then carefully
set the pinion flange to one side to avoid damage to
the flanged seal surface.
Figure 4B1 – 30
14 Ensure that pinion shaft thread is free from thread sealant, burrs, oil, dirt or grease, then coat splines and seal
surface of a new pinion flange with the recommended final drive lubricant.
15 Install the new pinion flange and a new retaining nut.
The new pinion flange will be an interference
fit on the pinion shaft splines and should only
be pulled into place by tightening the
retaining nut. During installation, do not,
under any circumstances use force or
hammer the flange onto the pinion splines.
16 Tighten flange retaining nut gradually until pinion shaft end play is reduced to approximately 0.50 mm.
17 Attach pulley to the new pinion flange and using spring balance, check pre-load. Continue tightening nut while
alternatively turning pinion to seat bearings, until the pre-load figure recorded previously (Step 4b) is reached.
Further increase this original pre-load reading by 0.5 Nm.