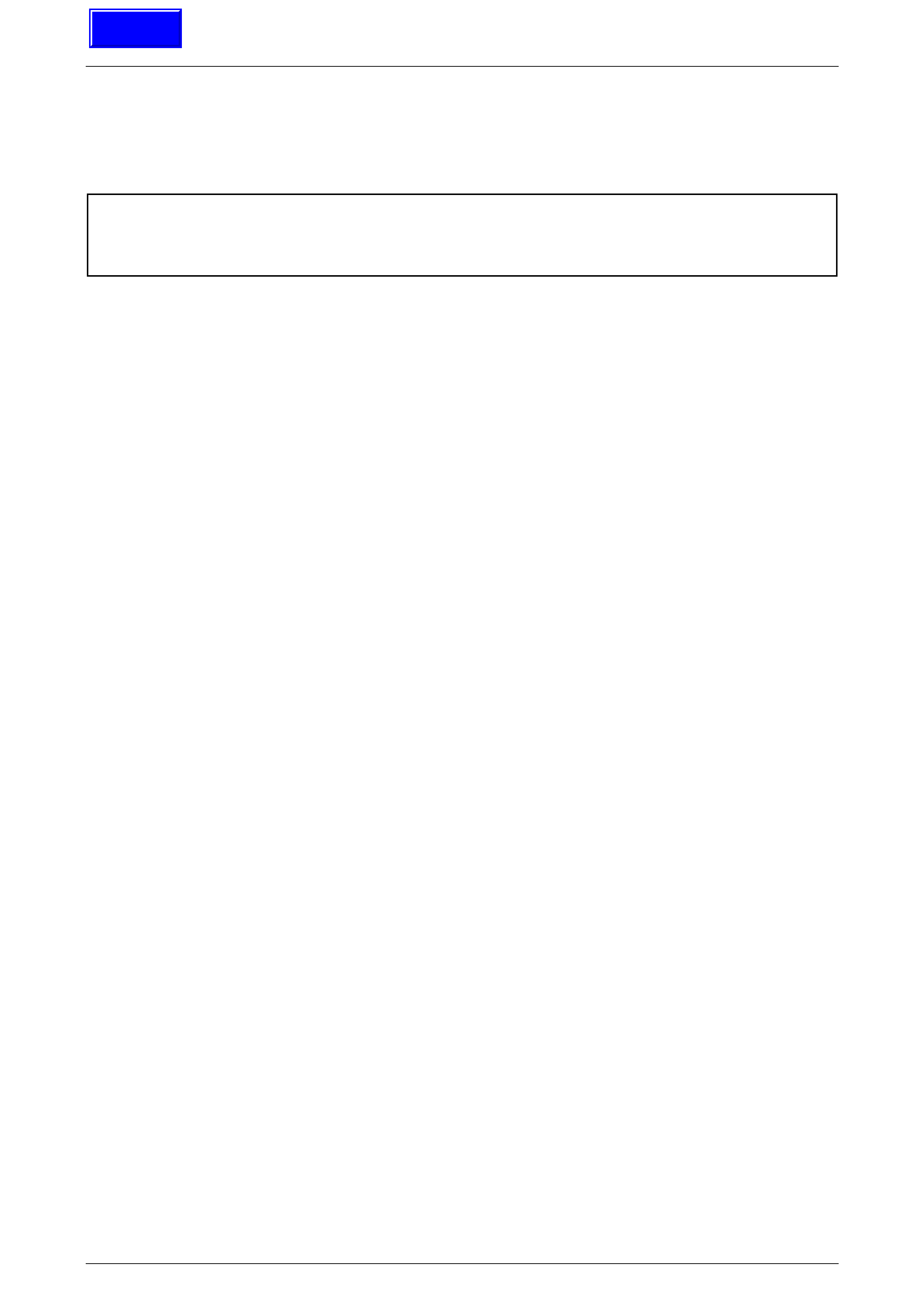
Service and Park B raki ng Syst em Page 5A–1
Page 5A–1
Section 5A
Service and Park Braking System
ATTENTION
Before performing any service operation or other procedure described in this Section, refer to Section 00
Warnings, Cautions and Notes for correct workshop practices with regard to safety and/or property damage.
1 General Information............................................................................................................................... 2
1.1 General Description ...............................................................................................................................................3
Master Cylinder ......................................................................................................................................................3
Construction .......................................................................................................................................................3
Operation............................................................................................................................................................5
2 Service Operations................................................................................................................................ 9
2.1 Front Brake Disc.....................................................................................................................................................9
Remove ...................................................................................................................................................................9
Inspection .............................................................................................................................................................10
Brake Disc and Hub Indexing..............................................................................................................................10
Front Hub Runout Check..................................................................................................................................10
Reinstall ................................................................................................................................................................11
2.2 Front Brake Disc Shield.......................................................................................................................................12
Remove .................................................................................................................................................................12
Reinstall ................................................................................................................................................................12
2.3 Pressure Differential Warning Switch ................................................................................................................13
Remove .................................................................................................................................................................13
Test........................................................................................................................................................................13
Reinstall ................................................................................................................................................................14
2.4 Master Cylinder ....................................................................................................................................................15
Remove .................................................................................................................................................................15
Disassemble.....................................................................................................................................................15
Clean and Inspect.................................................................................................................................................17
Reassemble......................................................................................................................................................18
Reinstall ................................................................................................................................................................23
2.5 Brake Booster.......................................................................................................................................................24
3 Specifications....................................................................................................................................... 25
Brake Fluid............................................................................................................................................................25
Master Cylinder ....................................................................................................................................................25
Front Disc..............................................................................................................................................................25
Booster..................................................................................................................................................................25
4 Torque Wrench Specifications........................................................................................................... 26