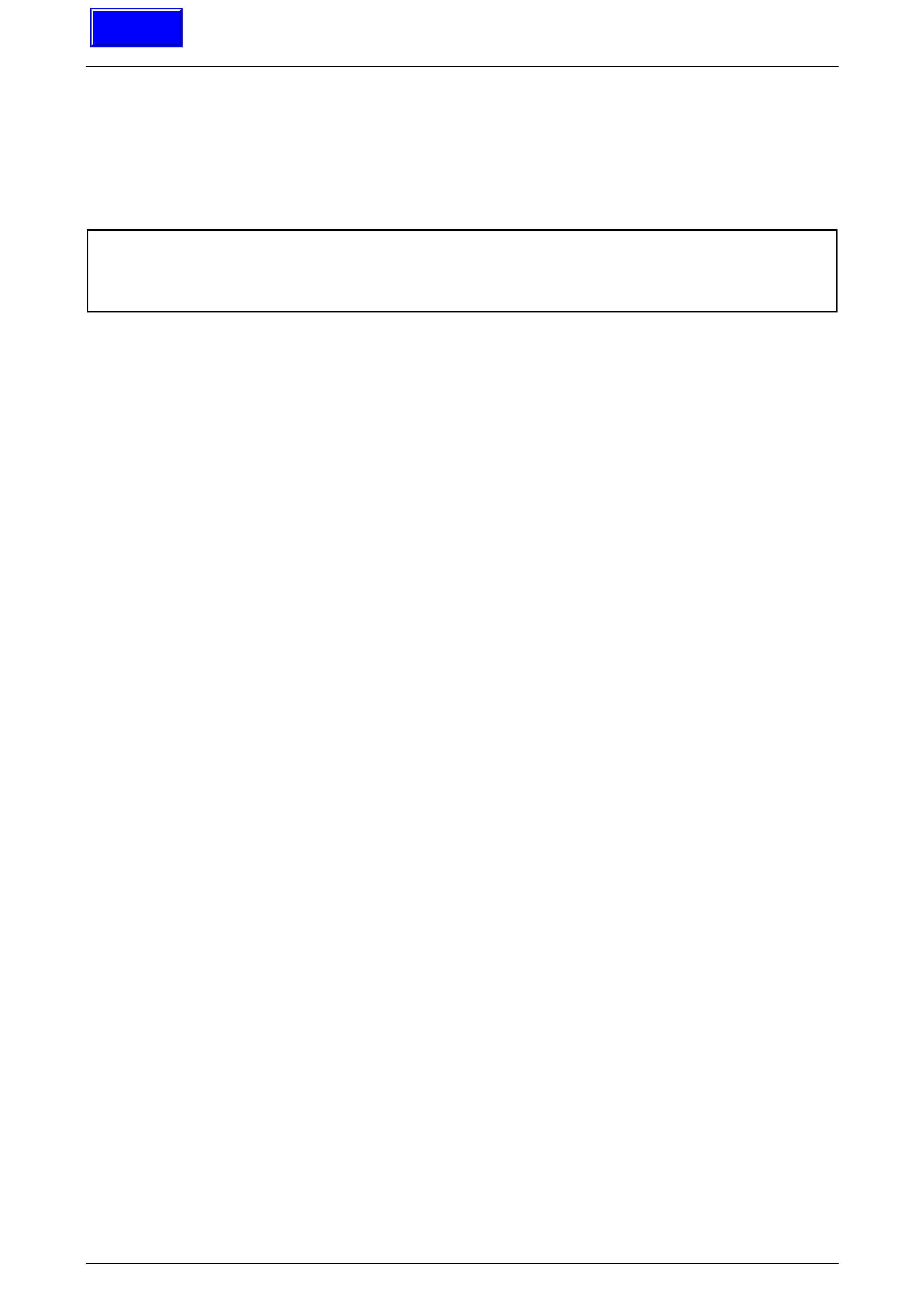
Powertrain Management – Diagnostic Tables – GEN III V8 Engine Page 6C3-2A-1
Page 6C3-2A-1
Section 6C3-2A
Powertrain Management – Diagnostic Tables -
GEN III V8 Engine
ATTENTION
Before performing any Service Operation or other procedure described in this Section, refer to Section 00
Warnings, Cautions And Notes for correct workshop practices with regard to safety and/or property damage.
1 Introduction............................................................................................................................................ 3
1.1 Engine Diagnostic Trouble Codes (DTC).............................................................................................................3
1.2 PIM Diagnostic Trouble Codes (DTC)...................................................................................................................5
1.3 Automatic Transmission Diagnostic Trouble Codes (DTC)................................................................................6
1.4 PIM Connector – A5 ...............................................................................................................................................7
1.5 PIM Connector Terminal Definitions.....................................................................................................................8
2 General Diagnostic Tables.................................................................................................................... 9
2.1 On-Board Diagnostic (OBD) System Check.........................................................................................................9
Circuit Description...............................................................................................................................................9
Diagnostic Aids.................................................................................................................................................10
Test Description................................................................................................................................................10
On-Board Diagnostic System Check – Diagnostic Table..................................................................................11
2.1 Data Link Connector Diagnosis..........................................................................................................................12
Circuit Description.............................................................................................................................................13
Diagnostic Aids.................................................................................................................................................13
Test Description................................................................................................................................................13
Data Link Connector – Diagnostic Table..........................................................................................................14
3 Diagnostic Trouble Code Tables........................................................................................................ 16
DTC P0481 – Cooling Fan High Speed Relay Control ..................................................................................................16
Circuit Description.............................................................................................................................................16
Conditions for Running the DTC.......................................................................................................................17
Conditions for Setting the DTC.........................................................................................................................17
Action Taken When the DTC Sets....................................................................................................................17
Conditions for Clearing the MIL/DTC................................................................................................................17
Diagnostic Aids.................................................................................................................................................17
Test Description................................................................................................................................................17
P0481 – Cooling Fan High Speed Relay Control – Diagnostic Table...............................................................18
DTC U1000 – No Class 2 Serial Data..............................................................................................................................20
Circuit Description.............................................................................................................................................21
Conditions for Running the DTC.......................................................................................................................21
Conditions for Setting the DTC.........................................................................................................................21
Action Taken When the DTC Sets....................................................................................................................21
Conditions for Clearing the DTC.......................................................................................................................21
Diagnostic Aids.................................................................................................................................................21
Test Description................................................................................................................................................21
DTC U1000 – No Class 2 Serial Data – Diagnostic Table................................................................................21
DTC U1001 – No Serial Data from PCM..........................................................................................................................22
Circuit Description.............................................................................................................................................23
Conditions for Running the DTC.......................................................................................................................23
Conditions for Setting the DTC.........................................................................................................................23
Action Taken When the DTC Sets....................................................................................................................23
Conditions for Clearing the MIL/DTC................................................................................................................23