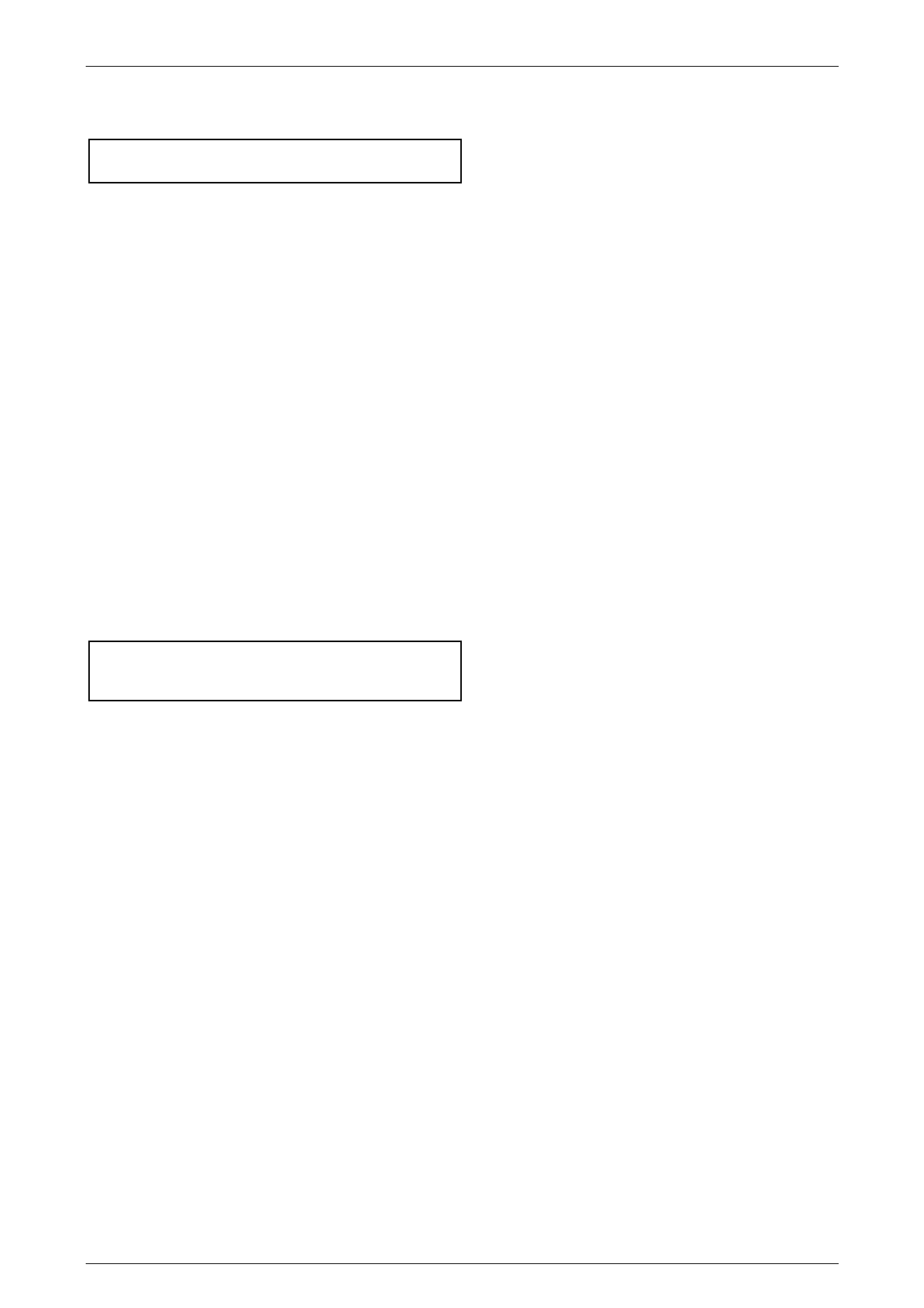
Automatic Transmission – On-Vehicle Servicing Page 7C4-13
Page 7C4-17
3 Install the nut securing the external manual shaft lever, then tighten to the correct torque specification, while
holding the lever with an adjustable wrench.
Transmission external manual shaft
lever nut torque specification................................15 Nm
4 Reinstall the wiring harness connector but do not install the CPA at this time, as the switch must be adjusted first.
5 Reinstall the shift selector cable fitting to the external manual shaft lever pin, then check the cable adjustment.
Refer to Cable Adjust in 2.2 Shift Selector Cable, in this Section.
6 Adjust the neutral start and back-up lamp switch position as described in the next procedure.
7 Reinstall the front propeller shaft, refer to Section 4C2 Propeller Shaft & Universal Joints, in the MY 2004 AWD
Wagon S ervice Information.
Adjust
1 With the vehicle still raised, rotate the neutral start and back-up lamp switch body, back and forth until a central
position is attained, then lightly tighten the front bolt to retain.
2 With the ignition switched to the ON position, check that the engine can only be started in both the Park and
Neutral selector positions. A further minor switch adjustment may be required to achieve this state.
3 Also check that the back-up lamps illuminat e when Rev erse range is sel ect ed.
4 After the switch adjustment, tighten the switch retaining screws to the correct torque specification.
NOTE
To gain access to the rear screw, it will be
necessary to remove the wiring harness
connector once again.
Neutral start and back-up
lamp switch retaining screw
torque specific atio n ..............................................25 Nm
5 Following the bolt tightening procedure, reinstall the wiring harness connector and engage the security slide and
the CPA lock.
6 Lower the vehicle to the ground and check the operation of the NSBU lamp switch. The vehicle should only start in
either ‘P’ (Park) or ‘N’ (Neutral) ranges and the Back-up lamps should only illuminate when the ‘R’ (Reverse) range
is selected.
Test
1 Check the shift selector cable adjustment. Refer to Cable Adjust, in 2.2 Shift Selector Cable, in this Section.
2 Check that the neutral start and back-up lamp switch is adjusted correctly. Refer to Adjust, in 2.3 Neutral Start and
Back-up Lamp Switch, in this Section.
3 With the ignition switch in the ON position and the instrument active, check that the display in the Multi Function
Display (MFD) in the instrument displays 'P' when the selector is in the Park position.
4 Move the shift selector lever through each of the range positions and check that the MFD shows that the selected
range is displayed .
5 Check that the engine will only crank when the Park and Neutral positions are selected.
6 Check that, when Reverse is selected, the back-up lamps are activated.
7 If any of the checks detailed in Steps 3 to 6 fails, refer to Instrument Panel Gear Indicator Check, in
Section 6C3-2C Functional Checks, in the MY 2003 VY and V2 Series Service Information.