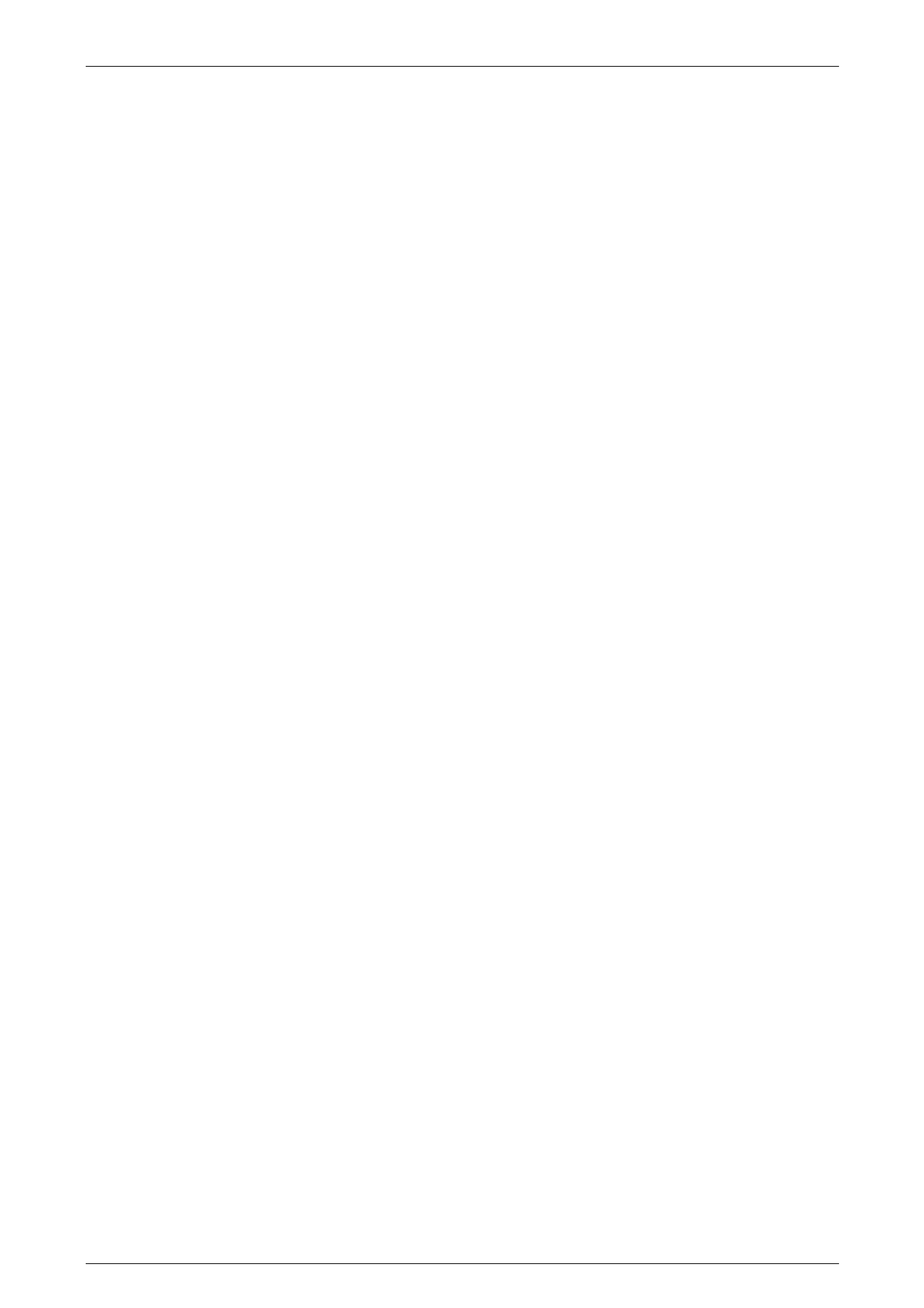
Occupant Protection System Page 12M–4
Page 12M–4
2.9 Left-hand Pretensioner DTCs ............................................................................................................................. 76
DTC 49 – Left Hand Pretensioner Circuit Short to Battery............................................................................... 76
Introduction ...................................................................................................................................................... 76
Circuit Description............................................................................................................................................ 76
Test Description ............................................................................................................................................... 76
Diagnostic Table Notes .................................................................................................................................... 76
Diagnostic Table............................................................................................................................................... 77
DTC 50 – Left Hand Pretensioner Circuit Short to Ground .............................................................................. 78
Introduction ...................................................................................................................................................... 78
Circuit Description............................................................................................................................................ 78
Test Description ............................................................................................................................................... 78
Diagnostic Table Notes .................................................................................................................................... 78
Diagnostic Table............................................................................................................................................... 79
DTC 51 – Left Hand Pretensioner Circuit Capacitance Too High ....................................................................80
Introduction ...................................................................................................................................................... 80
Circuit Description............................................................................................................................................ 80
Action Required................................................................................................................................................ 80
DTC 52 – Left Hand Pretensioner Circuit Capacitance Too Low.....................................................................81
Introduction ...................................................................................................................................................... 81
Circuit Description............................................................................................................................................ 81
Action Required................................................................................................................................................ 81
DTC 53 – Left Hand Pretensioner Circuit Resistance Too High....................................................................... 82
Introduction ...................................................................................................................................................... 82
Circuit Description............................................................................................................................................ 82
Test Description ............................................................................................................................................... 82
Diagnostic Table Notes .................................................................................................................................... 82
Diagnostic Table............................................................................................................................................... 83
DTC 54 – Left Hand Pretensioner Circuit Resistance Too Low ....................................................................... 84
Introduction ...................................................................................................................................................... 84
Circuit Description............................................................................................................................................ 84
Test Description ............................................................................................................................................... 84
Diagnostic Table Notes .................................................................................................................................... 84
Diagnostic Table............................................................................................................................................... 85
DTC 247 – Left Hand Pretensioner Circuit Power Stage Error......................................................................... 86
Introduction ...................................................................................................................................................... 86
Circuit Description............................................................................................................................................ 86
Action Required................................................................................................................................................ 86
Diagnostic Table Notes .................................................................................................................................... 86
Diagnostic Table............................................................................................................................................... 87
2.10 Right-hand Pretensioner DTCs........................................................................................................................... 88
DTC 65 – Right Hand Pretensioner Circuit Short to Battery ............................................................................ 88
Introduction ...................................................................................................................................................... 88
Circuit Description............................................................................................................................................ 88
Test Description ............................................................................................................................................... 88
Diagnostic Table Notes .................................................................................................................................... 88
Diagnostic Table............................................................................................................................................... 89
DTC 66 – Right Hand Pretensioner Circuit Short to Ground............................................................................ 90
Introduction ...................................................................................................................................................... 90
Circuit Description............................................................................................................................................ 90
Test Description ............................................................................................................................................... 90
Diagnostic Table Notes .................................................................................................................................... 90
Diagnostic Table............................................................................................................................................... 91
DTC 67 – Right Hand Pretensioner Circuit Capacitance Too High.................................................................. 92
Introduction ...................................................................................................................................................... 92
Circuit Description............................................................................................................................................ 92
Action Required................................................................................................................................................ 92
DTC 68 – Right Hand Pretensioner Circuit Capacitance Too Low................................................................... 93
Introduction ...................................................................................................................................................... 93
Circuit Description............................................................................................................................................ 93
Action Required................................................................................................................................................ 93