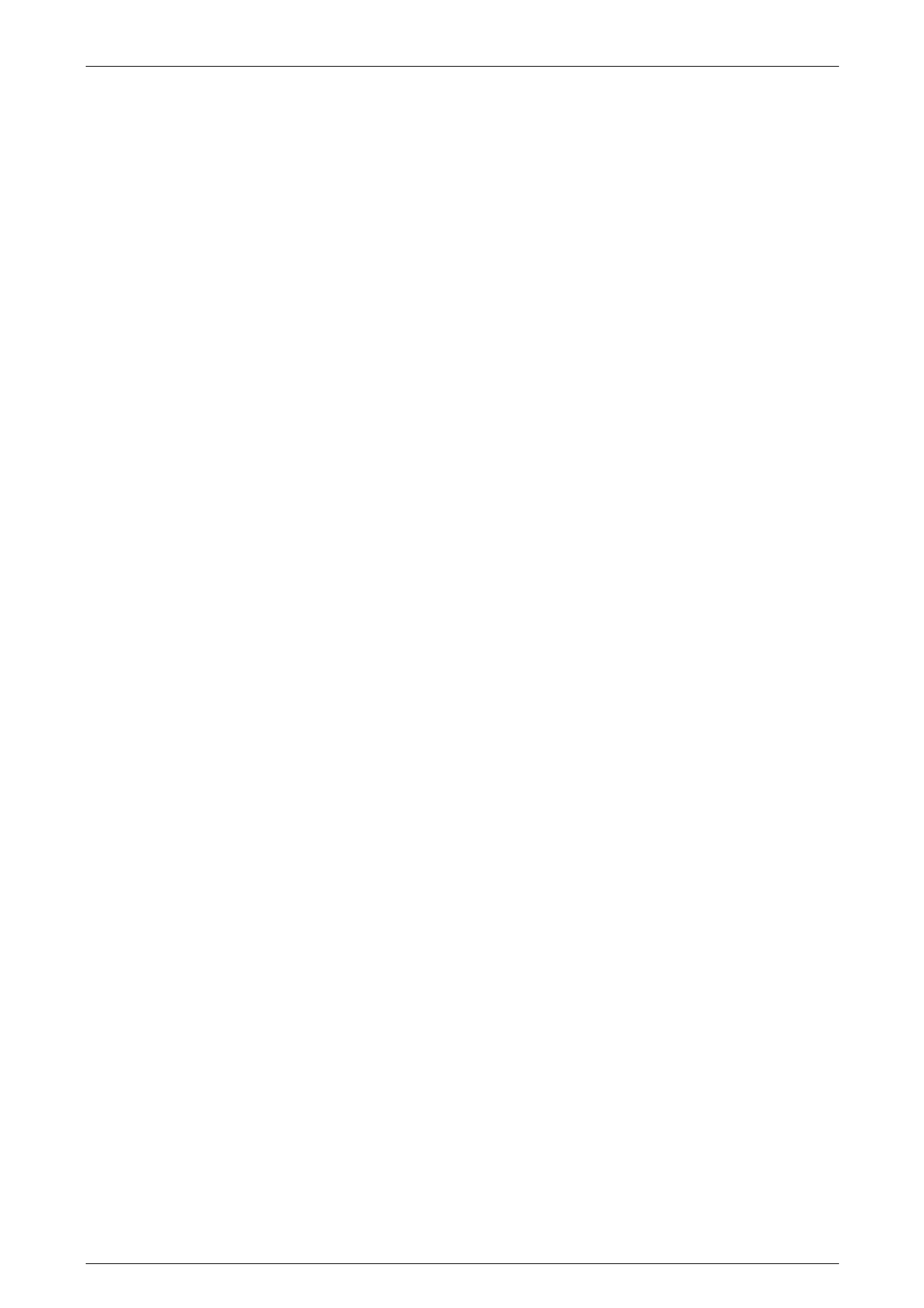
Section 12P Wiring Diagrams - Utility, Regular Cab, Crew Cab and Regular & Crew Cab AWD Page 12P–2
Page 12P–2
4 Diagnostic Tests...................................................................................................................................18
4.1 Testing For Voltage ............................................................................................................................................. 18
4.2 Testing For Continuity......................................................................................................................................... 19
4.3 Testing For Voltage Drop.................................................................................................................................... 20
4.4 Testing For Short To Ground.............................................................................................................................. 21
Using A Test Light Or Voltmeter......................................................................................................................... 21
Using A Self-Powered Test Light Or Ohmmeter................................................................................................ 22
Using A Short Finder........................................................................................................................................... 22
Using A Compass................................................................................................................................................ 22
Using A Circuit Breaker....................................................................................................................................... 22
4.5 Operating A Short Finder.................................................................................................................................... 23
Measuring Current............................................................................................................................................... 24
4.6 Detecting Intermittent Electrical Faults ............................................................................................................. 25
Diagnostic Procedure.......................................................................................................................................... 25
Checking Terminal Contact................................................................................................................................. 25
Meter Connections............................................................................................................................................... 26
Additional Information....................................................................................................................................... 26
5 Wiring Repair Procedures...................................................................................................................27
5.1 General Information............................................................................................................................................. 27
5.2 Performing Wiring Harness Repairs .................................................................................................................. 28
Soldering .............................................................................................................................................................. 28
The Five Points To Soldering.............................................................................................................................. 28
Step 1 Soldering Preparation ....................................................................................................................... 28
Step 2 Iron Preparation ................................................................................................................................ 29
Step 3 Forming a Heat Bridge...................................................................................................................... 29
Step 4 Soldering Iron Removal..................................................................................................................... 29
Step 5 Prevent Job Movement ..................................................................................................................... 30
Joining Wire ......................................................................................................................................................... 30
Twist Joint........................................................................................................................................................ 30
Splice Joint....................................................................................................................................................... 30
The Y Junction ................................................................................................................................................. 31
The T Junction.................................................................................................................................................. 31
5.3 Splicing Wiring Using Splice Clips..................................................................................................................... 32
Step 1 Open the Harness................................................................................................................................. 32
Step 2 Cut the Wire.......................................................................................................................................... 32
Step 3 Select the Correct Size and Type of Wire........................................................................................... 32
Step 4 Strip the Insulation............................................................................................................................... 33
Metric Size ....................................................................................................................................................... 33
AWG................................................................................................................................................................. 33
Step 5 Crimping the Joint................................................................................................................................ 34
Step 6 Solder.................................................................................................................................................... 36
Step 7 Tape the Splice..................................................................................................................................... 37
5.4 ABS And SRS Wiring Repair............................................................................................................................... 38
ABS And SRS Wire Pigtail Repair ...................................................................................................................... 38
Wiring Repair........................................................................................................................................................ 38
Step 1 Open the Harness............................................................................................................................. 39
Step 2 Cut the Wire...................................................................................................................................... 39
Step 3 Select the Correct Size and Type of Wire ......................................................................................... 39
Step 4 Strip the Insulation ............................................................................................................................ 40
Step 5 Select and Position the Splice Sleeve............................................................................................... 40
Step 6 Insert First Wire Into Splice Sleeve and Crimp..................................................................................40
Step 7 Crimp the Second Wire in the Splice................................................................................................. 41
Step 8 Shrink the Insulation around the Splice............................................................................................. 41
Step 9 Close the Harness............................................................................................................................. 41
ABS And SRS Wiring Splice Repair................................................................................................................... 41