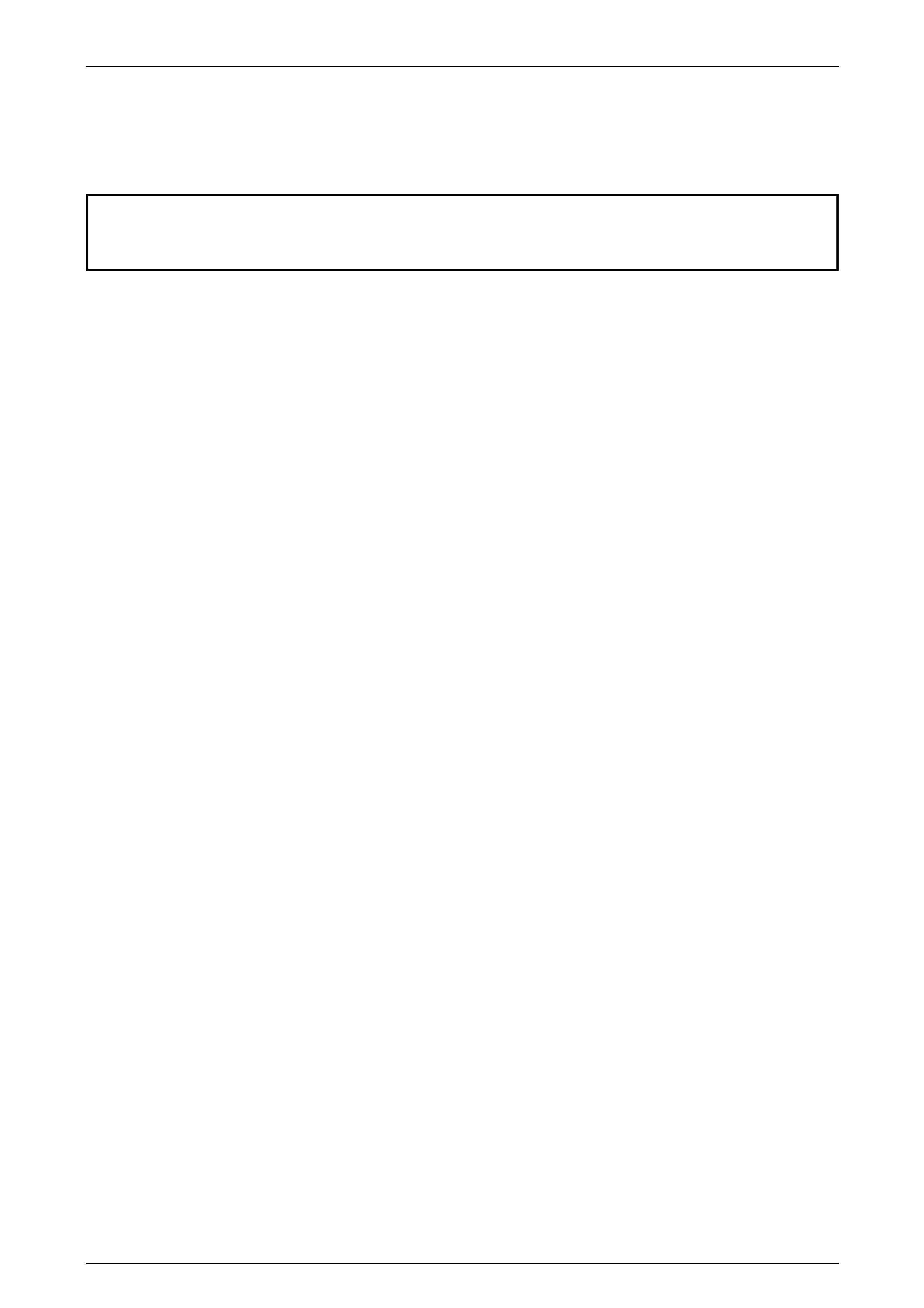
Front Suspension Page 3A – 1
Section 3A
Front Suspension
IMPORTANT
Before performing any Service Operation or other procedure described in this Section, refer to 00 Warnings,
Cautions and Notes for correct workshop practices with regard to safety and/or property damage.
1 General Description...............................................................................................................................2
2 Service Operations.................................................................................................................................4
2.1 Service Notes and Cautions.................................................................................................................................. 4
2.2 Jacking Precautions.............................................................................................................................................. 5
2.3 Wheel Alignment Checking and Adjustment....................................................................................................... 6
Preliminary Inspection .......................................................................................................................................... 6
Caster Adjustment................................................................................................................................................. 6
Camber Adjustment............................................................................................................................................... 7
Toe Adjustment...................................................................................................................................................... 8
2.4 Suspension and Trim Height, Check.................................................................................................................... 9
Preliminary Inspection .......................................................................................................................................... 9
Procedure............................................................................................................................................................. 10
Front and Rear Suspen sion Height Comparison .............................................................................................. 10
2.5 Front Strut Assembly .......................................................................................................................................... 11
Remove................................................................................................................................................................. 11
Disassemble......................................................................................................................................................... 12
Reinstall................................................................................................................................................................ 13
2.6 Stabiliser Bar Link ............................................................................................................................................... 15
Remove................................................................................................................................................................. 15
Reinstall................................................................................................................................................................ 16
3 Specifications.......................................................................................................................................17
Front Spring Details............................................................................................................................................. 17
Front Stabiliser Bar Details................................................................................................................................. 17
Front Strut Details................................................................................................................................................ 18
Suspension and Trim Height Specifications..................................................................................................... 18
Front Wheel Alignment........................................................................................................................................ 20
4 Torque Wrench Specifications............................................................................................................21
5 Special Tools ........................................................................................................................................22
Page 3A-1