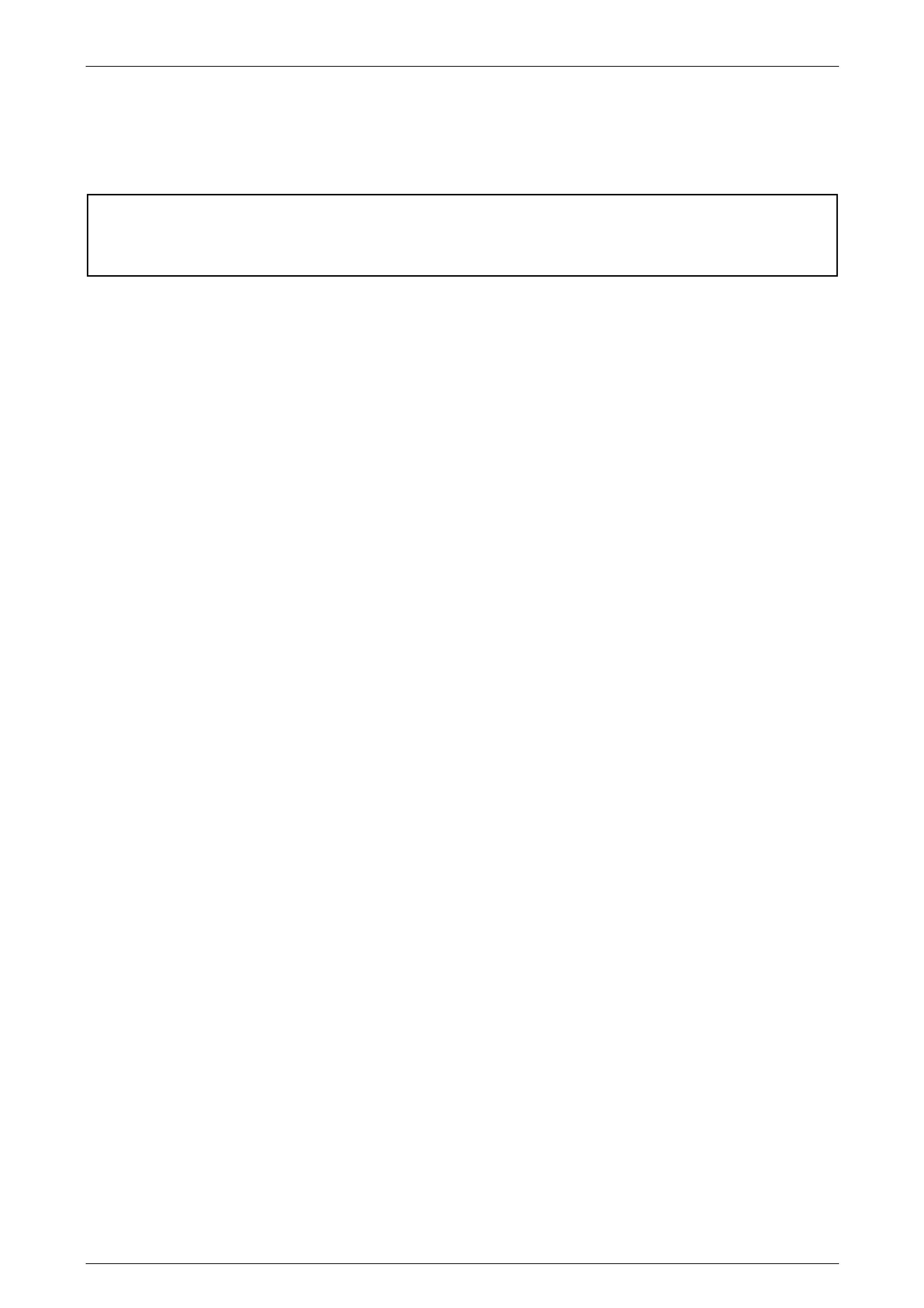
Rear Propeller Shaft and Universal Joints 4C1 – 1
4C1 – 1
Section 4C1
Rear Propeller Shaft & Universal Joints
ATTENTION
Before performing any Service Operation or other procedure described in this Section, refer to Section 00
Warnings, Cautions and Notes for correct workshop practices with regard to safety and/or property damage.
1 General Information ...............................................................................................................................3
2 Service Operations.................................................................................................................................7
2.1 Propeller Shaft ....................................................................................................................................................... 7
Remove................................................................................................................................................................... 7
All VZ.................................................................................................................................................................. 7
All VZ With IRS Except AWD Wagon................................................................................................................. 8
VZ AWD Wagon............................................................................................................................................... 10
VZ AWD With Leaf Spring Rear Suspension ................................................................................................... 11
Reinstall................................................................................................................................................................ 12
All VZ With IRS Except AWD Models............................................................................................................... 12
VZ AWD Wagon............................................................................................................................................... 13
VZ With Leaf Spring Rear Suspension............................................................................................................. 14
2.2 Rubber Coupling.................................................................................................................................................. 15
Replace................................................................................................................................................................. 15
2.3 Centre Constant Velocity Joint (Plunge Type) – AWD Wagon......................................................................... 17
Remove................................................................................................................................................................. 17
Disassemble......................................................................................................................................................... 20
Inspect .................................................................................................................................................................. 21
Propeller Shaft and Boot.................................................................................................................................. 21
Constant Velocity Joint..................................................................................................................................... 21
Reassemble.......................................................................................................................................................... 22
Method 1 .......................................................................................................................................................... 22
Method 2 .......................................................................................................................................................... 22
Reinstall................................................................................................................................................................ 23
2.4 Centre Constant Velocity Joint (Fixed Type) – Live Axle Models.................................................................... 26
Remove................................................................................................................................................................. 26
Inspect .................................................................................................................................................................. 28
Reassemble.......................................................................................................................................................... 29
Reinstall................................................................................................................................................................ 31
2.5 Centre Bearing Assembly ................................................................................................................................... 33
All VZ With V6 Engine and IRS (Except AWD Wagon)...................................................................................... 33
Remove............................................................................................................................................................ 33
Reinstall ........................................................................................................................................................... 35
AWD Wagon Models............................................................................................................................................ 37
Remove............................................................................................................................................................ 37
Reinstall ........................................................................................................................................................... 38
All VZ With a Live Axle........................................................................................................................................ 39
Remove............................................................................................................................................................ 39
Replace............................................................................................................................................................ 41