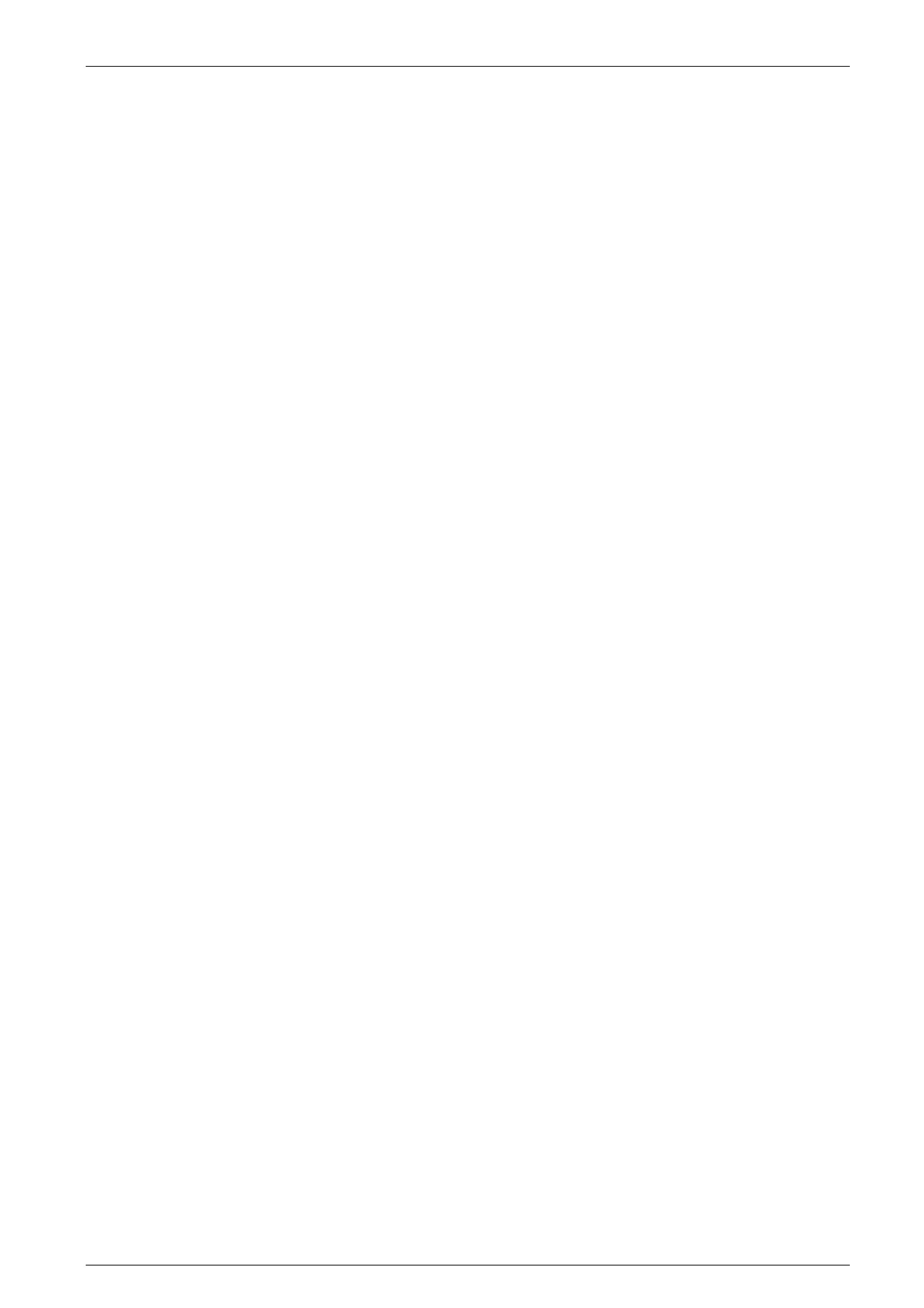
Dual Park Assist Page 12F2–2
Diagnostic Table Notes ....................................................................................................................................... 27
Diagnostic Table.................................................................................................................................................. 27
3.7 LED Circuit Test................................................................................................................................................... 28
Introduction.......................................................................................................................................................... 28
Circuit Description............................................................................................................................................... 28
Diagnostic Table Notes ....................................................................................................................................... 28
Diagnostic Table.................................................................................................................................................. 28
3.8 Transmission Park / Neutral Position Input Circuit Test.................................................................................. 29
V6 Engine ............................................................................................................................................................. 29
Introduction ...................................................................................................................................................... 29
Circuit Description............................................................................................................................................ 29
Test Description ............................................................................................................................................... 29
Diagnostic Table Notes .................................................................................................................................... 29
Diagnostic Table............................................................................................................................................... 29
V8 Engine ............................................................................................................................................................. 31
Introduction ...................................................................................................................................................... 31
Circuit Description............................................................................................................................................ 31
Test Description ............................................................................................................................................... 31
Diagnostic Table Notes .................................................................................................................................... 31
Diagnostic Table............................................................................................................................................... 31
3.9 Transmission Reverse Position Input Circuit Test........................................................................................... 33
4 Speed Auto Transmission................................................................................................................................ 33
Introduction ...................................................................................................................................................... 33
Circuit Description............................................................................................................................................ 33
Test Description ............................................................................................................................................... 33
Diagnostic Table Notes .................................................................................................................................... 33
Diagnostic Table............................................................................................................................................... 33
5 Speed Auto Transmission................................................................................................................................ 35
Introduction ...................................................................................................................................................... 35
Circuit Description............................................................................................................................................ 35
Test Description ............................................................................................................................................... 35
Diagnostic Table Notes .................................................................................................................................... 35
Diagnostic Table............................................................................................................................................... 35
3.10 Speed Signal Input Circuit Test.......................................................................................................................... 37
Introduction.......................................................................................................................................................... 37
Circuit Description............................................................................................................................................... 37
Diagnostic Table Notes ....................................................................................................................................... 37
Diagnostic Table.................................................................................................................................................. 37
3.11 No Audible Tone From Front Alarm................................................................................................................... 38
Introduction.......................................................................................................................................................... 38
Circuit Description............................................................................................................................................... 38
Diagnostic Table Notes ....................................................................................................................................... 38
Diagnostic Table.................................................................................................................................................. 38
3.12 No Audible Tone From Rear Alarm .................................................................................................................... 39
Introduction.......................................................................................................................................................... 39
Circuit Description............................................................................................................................................... 39
Diagnostic Table Notes ....................................................................................................................................... 39
Diagnostic Table.................................................................................................................................................. 39
3.13 Front Object Sensor Circuit Test........................................................................................................................ 40
Introduction.......................................................................................................................................................... 40
Circuit Description............................................................................................................................................... 40
Test Descriptions................................................................................................................................................. 40
Diagnostic Table Notes ....................................................................................................................................... 40
Diagnostic Table.................................................................................................................................................. 40
3.14 Rear Object Sensor Circuit Test......................................................................................................................... 42
Introduction.......................................................................................................................................................... 42
Circuit Description............................................................................................................................................... 42
Test Description................................................................................................................................................... 42
Diagnostic Table Notes ....................................................................................................................................... 42
Diagnostic Table.................................................................................................................................................. 42
Page 12F2–2