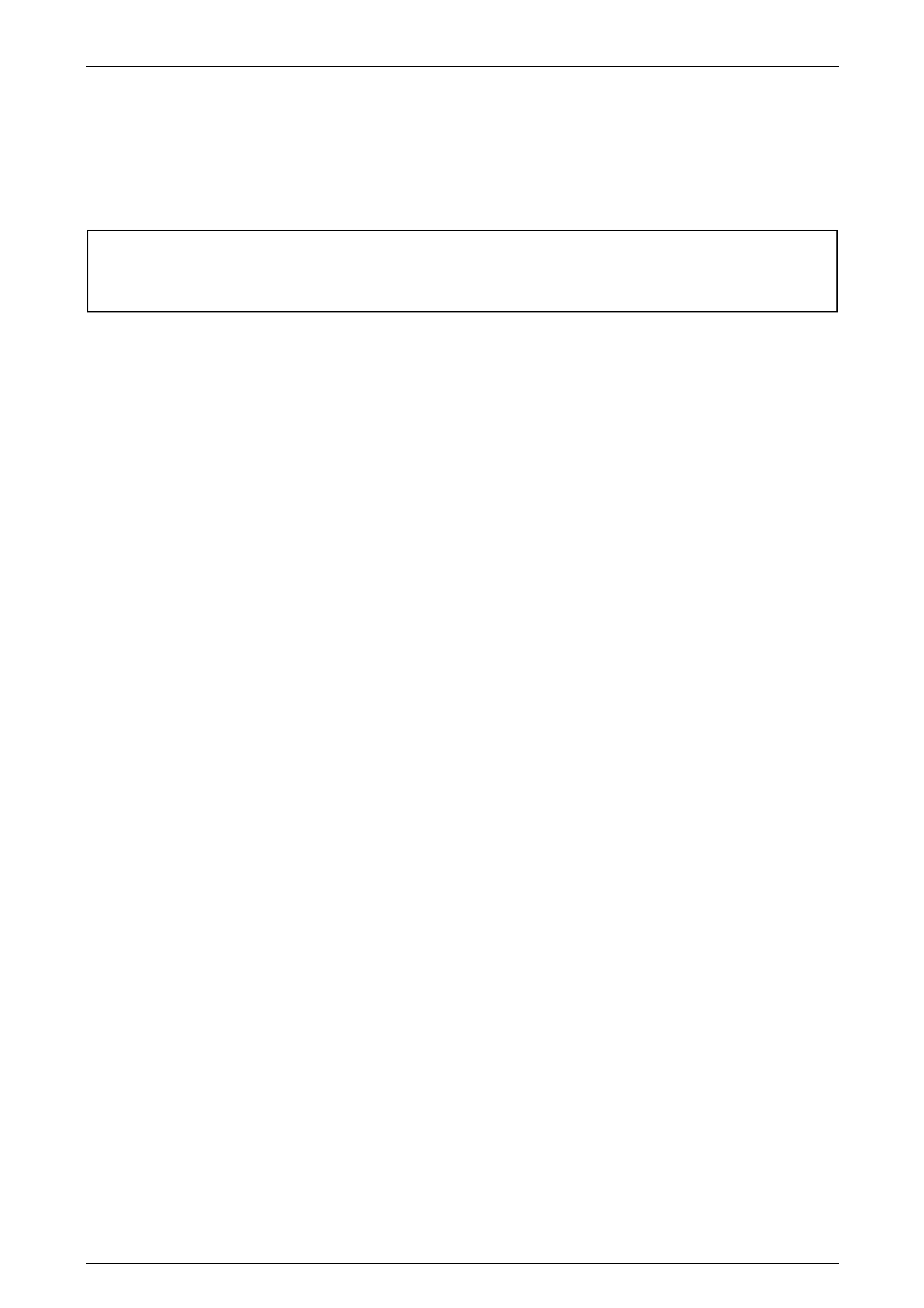
HVAC Climate Control (Manual A/C) – Description and Operation Page 2A-1
Page 2A-1
Section 2A
HVAC Climate Control (Manual A/C) –
Description and Operation
ATTENTION
Before performing any service operation or other procedure described in this Section, refer to Section 00
Warnings, Cautions and Notes for correct workshop practices with regard to safety and / or property damage.
1 General Information ...............................................................................................................................3
1.1 Caution Label......................................................................................................................................................... 3
2 General Description ...............................................................................................................................4
2.1 Air Flow................................................................................................................................................................... 4
2.2 HVAC Inlet and Outlet Ducts................................................................................................................................. 5
Inlet ......................................................................................................................................................................... 5
Air Distribution Ducts............................................................................................................................................ 6
Cabin Ventilation Outlets ...................................................................................................................................... 7
Body Ventilation Outlets....................................................................................................................................... 8
Outlet Assembly................................................................................................................................................. 8
2.3 Heater.................................................................................................................................................................... 10
Water Valve Assembly – V6 ................................................................................................................................ 10
Water Valve Assembly – GEN III V8.................................................................................................................... 10
Heater Operation – Auto A/C – V6...................................................................................................................... 10
Full Cold........................................................................................................................................................... 10
Warm................................................................................................................................................................ 12
Full Hot............................................................................................................................................................. 13
Heater Operation – Auto A/C – GEN III V8 ......................................................................................................... 14
Full Cold........................................................................................................................................................... 14
Warm................................................................................................................................................................ 16
Full Hot............................................................................................................................................................. 17
Under-hood Heater Components – V6............................................................................................................... 18
Under-hood Heater Components – GEN III V8................................................................................................... 19
2.4 Air-conditioning Refrigerant Circuit................................................................................................................... 20
2.5 Vacuum Circuit..................................................................................................................................................... 21
Solenoid Pack and Vacuum Lines...................................................................................................................... 21
Vacuum Circuit Schematic.................................................................................................................................. 22
2.6 Heating, Ventilation and Air-conditioning (HVAC) Unit.................................................................................... 23
General Description............................................................................................................................................. 23
Assembled Views – Auto A/C........................................................................................................................... 24
Exploded View – Auto A/C............................................................................................................................... 26
Evaporator............................................................................................................................................................ 27
Heater Core........................................................................................................................................................... 28
Blower Motor and Fan Assembly ....................................................................................................................... 28
Electronic Blower Motor Controller.................................................................................................................... 29
Air Mix Doors and Motor ..................................................................................................................................... 29
Air Mix Doors.................................................................................................................................................... 29
Air Mix Door Motor ........................................................................................................................................... 29
Motor and Door Configurations ........................................................................................................................ 29
Air Mix Door Motor/Door Calibration................................................................................................................. 30
Vacuum Actuators............................................................................................................................................... 30
Single-stage Actuator....................................................................................................................................... 31
Two-stage Actuators ........................................................................................................................................ 31
Vacuum Solenoid Pack ....................................................................................................................................... 32