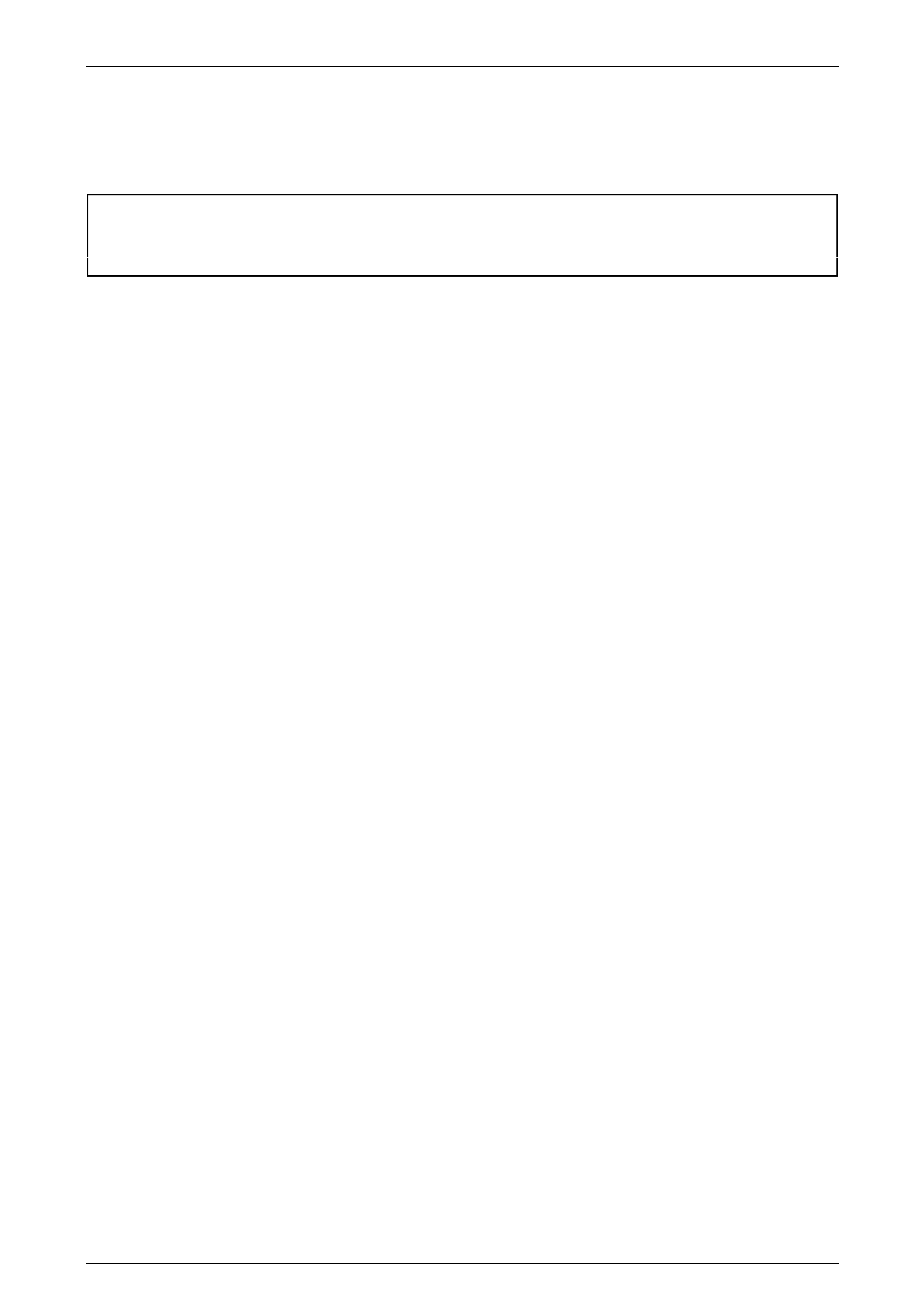
Charging System – GEN IV V8 Page 6D4-1–1
Page 6D4-1–1
Section 6D4-1
Charging System – GEN IV V8
ATTENTION
Before performing any Service Operation or other procedure described in this Section, refer to Section 00
Warnings, Cautions And Notes for correct workshop practices with regard to safety and/or property damage.
1 General Information ...............................................................................................................................2
1.1 Operation................................................................................................................................................................ 5
Circuit Overview..................................................................................................................................................... 5
Warning Lamp Conditions .................................................................................................................................... 5
Circuit Diagram...................................................................................................................................................... 6
2 Service Operations.................................................................................................................................7
2.1 Safety Precautions................................................................................................................................................. 7
2.2 Maintenance and On-vehicle Testing................................................................................................................... 8
Regulating Voltage Test........................................................................................................................................ 8
3 Major Service Operations....................................................................................................................10
3.1 Generator.............................................................................................................................................................. 10
Remove................................................................................................................................................................. 10
Disassemble......................................................................................................................................................... 12
Precautions ...................................................................................................................................................... 12
Check the rotor................................................................................................................................................. 14
Check the stator............................................................................................................................................... 15
Reassemble.......................................................................................................................................................... 16
Reinstall................................................................................................................................................................ 17
4 Diagnosis ..............................................................................................................................................18
5 Specifications.......................................................................................................................................19
6 Torque Wrench Specifications............................................................................................................20