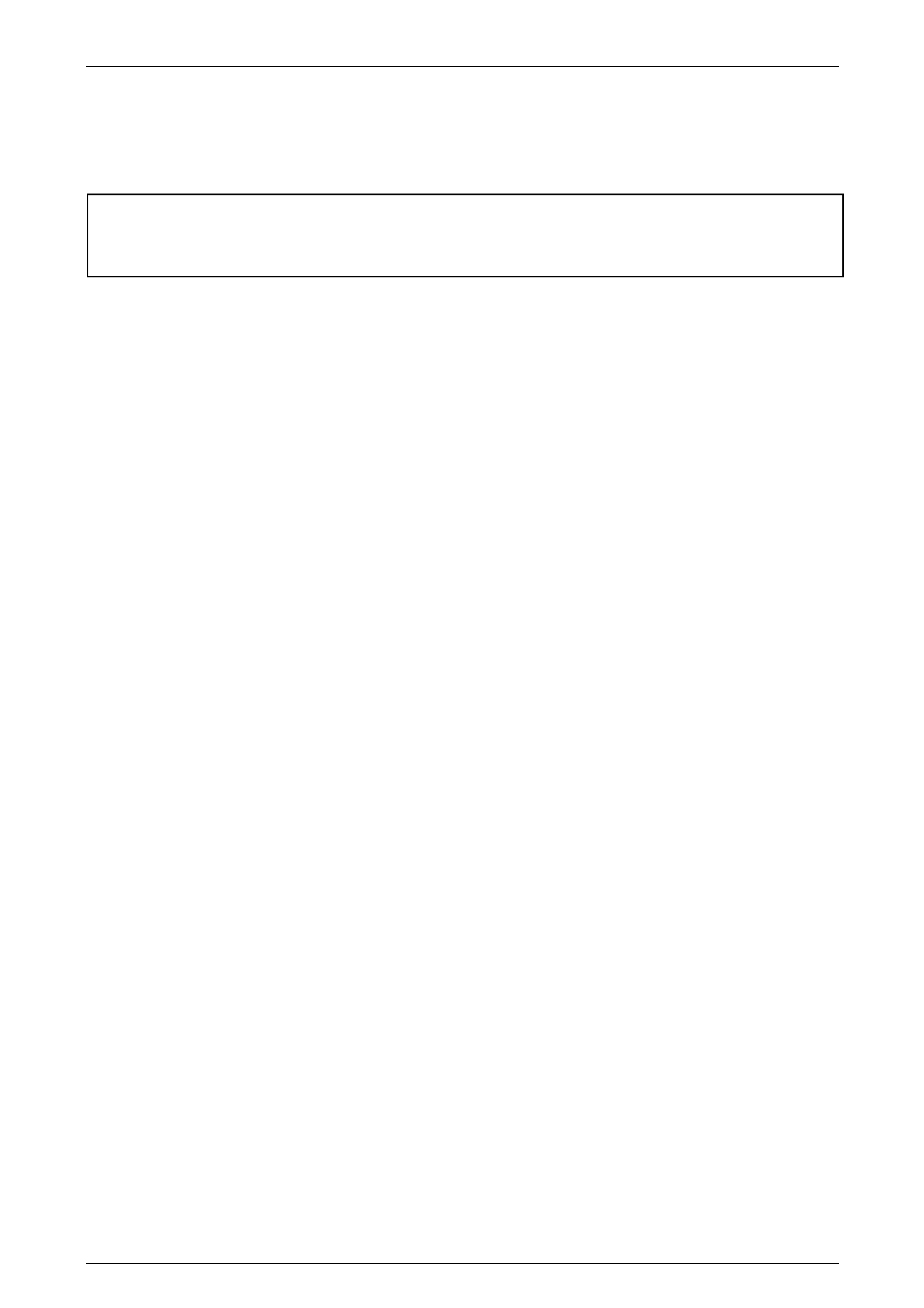
Charging System – V6 Page 6D1-1-1
Section 6D1-1
Charging System – V6
ATTENTION
Before performing any service operations or other procedure described in this Section, refer to Section 00
Warnings, Cautions and Notes for correct workshop practices with regard to safety and / or property damage.
1 General Information...............................................................................................................................3
1.1 Components........................................................................................................................................................... 3
Generator................................................................................................................................................................ 3
Generator Types ................................................................................................................................................ 3
Voltage Regulator.................................................................................................................................................. 4
1.2 System Operation .................................................................................................................................................. 5
Operation ........................................................................................................................................................... 5
Alternator Warning ............................................................................................................................................. 5
2 Diagnosis ................................................................................................................................................6
2.1 Diagnostic General Information............................................................................................................................ 6
Basic Diagnostic Tools Required......................................................................................................................... 6
2.2 Tech 2 Data List ..................................................................................................................................................... 7
2.3 Diagnostic Systems Check................................................................................................................................... 8
2.4 Wiring Diagram ...................................................................................................................................................... 9
2.5 Charging System Inoperative / Malfunctioning................................................................................................. 10
Diagnostic Table Notes .................................................................................................................................... 10
Diagnostic Table 100A Generator.................................................................................................................... 10
Diagnostic Table 120A Generator.................................................................................................................... 10
3 Minor Service Operations....................................................................................................................11
3.1 Safety Precautions............................................................................................................................................... 11
3.2 Maintenance......................................................................................................................................................... 12
Regular Checks.................................................................................................................................................... 12
Lubrication........................................................................................................................................................ 12
3.3 On-vehicle Testing............................................................................................................................................... 13
On-vehicle Checks 100A Generator ................................................................................................................... 13
Prerequisites .................................................................................................................................................... 13
Generator Test................................................................................................................................................. 13
On-vehicle Checks 120A Generator ................................................................................................................... 16
Prerequisites .................................................................................................................................................... 16
Generator Test................................................................................................................................................. 16
Charging Circuit Voltage Drop Test................................................................................................................... 19
Prerequisites .................................................................................................................................................... 19
Voltage Drop Test ............................................................................................................................................ 19
4 Major Service Operations....................................................................................................................20
4.1 Generator.............................................................................................................................................................. 20
Remove................................................................................................................................................................. 20
Reinstall................................................................................................................................................................ 21
4.2 Generator Mounting Bracket............................................................................................................................... 22
Remove................................................................................................................................................................. 22
Reinstall................................................................................................................................................................ 22
4.3 Drive Belt Routing................................................................................................................................................ 23
Without Air Conditioning .................................................................................................................................... 23
With Air Conditioning.......................................................................................................................................... 24
Page 6D1-1–1