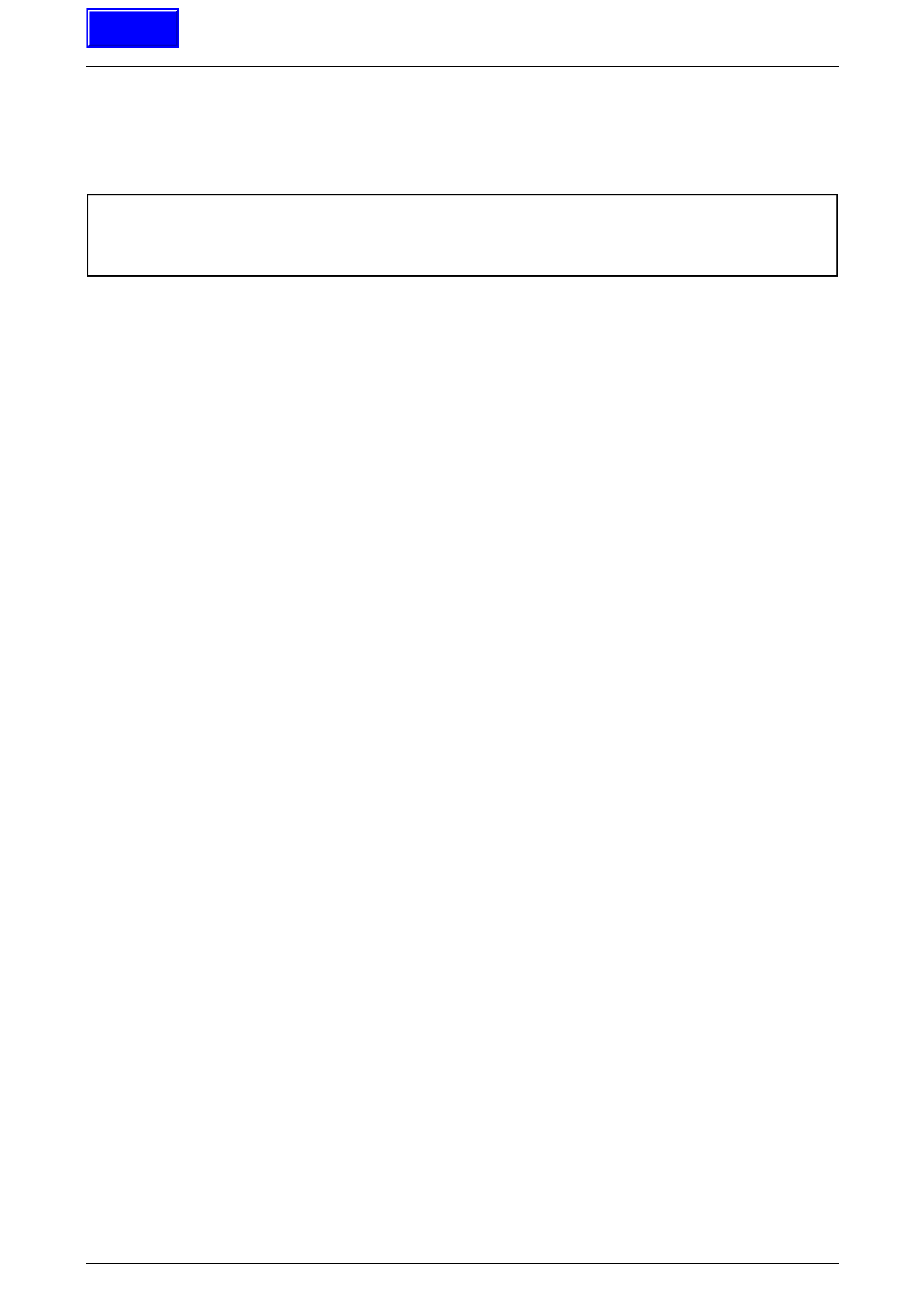
Fuel System Page 8A1–1
Page 8A1–1
Section 8A1
Fuel System
ATTENTION
Before performing any service operation or other procedure described in this Section, refer to Section 00
Warnings, Cautions and Notes for correct workshop practices with regard to safety and/or property damage.
1 General Information ...............................................................................................................................3
1.1 Modular Fuel Pump and Sender Assembly ......................................................................................................... 3
Fuel Pump .............................................................................................................................................................. 4
Single Turbine Fuel Pump.................................................................................................................................. 4
Single Line Fuel Delivery System......................................................................................................................... 5
Pressure Regulator................................................................................................................................................ 6
Fuel Level Sender Assembly ................................................................................................................................ 6
Rollover Valve........................................................................................................................................................ 7
1.2 Fuel Filler Cap........................................................................................................................................................ 8
1.3 System Components............................................................................................................................................. 9
V6 Engine ............................................................................................................................................................. 10
GEN III V8 Engine................................................................................................................................................. 11
2 System Checks.....................................................................................................................................12
2.1 Fuel System Depressurisation............................................................................................................................ 12
Repressurise........................................................................................................................................................ 13
2.2 Fuel Pressure Test............................................................................................................................................... 14
Installation............................................................................................................................................................ 14
Test ....................................................................................................................................................................... 15
Removal................................................................................................................................................................ 15
2.3 Fuel Leak Test...................................................................................................................................................... 16
V6 Engine ............................................................................................................................................................. 16
GEN III V8 Engine................................................................................................................................................. 17
3 Service Operations...............................................................................................................................18
3.1 Quick-connect Fittings........................................................................................................................................ 18
Quick-connect Fittings (Metal Collar) ................................................................................................................ 18
Remove............................................................................................................................................................ 18
Reinstall ........................................................................................................................................................... 19
Quick-connect Fittings (Plastic Collar).............................................................................................................. 20
Remove............................................................................................................................................................ 20
Reinstall ........................................................................................................................................................... 22
Tool No. AU533 .................................................................................................................................................... 23
Remove............................................................................................................................................................ 23
Reinstall ........................................................................................................................................................... 25
Tool Nos. 7370 and 7371 ..................................................................................................................................... 26
Remove............................................................................................................................................................ 26
Reinstall ........................................................................................................................................................... 26
3.2 Fuel Tank.............................................................................................................................................................. 27
Remove................................................................................................................................................................. 27
Reinstall................................................................................................................................................................ 31